QuickTakes / Información Rápida
Stay informed on workplace safety and health by joining over 370,000 subscribers who rely on QuickTakes and Información Rápida for essential updates.
Manténgase informado sobre la seguridad y la salud en el trabajo uniéndose a más de 370,000 suscriptores que confían en QuickTakes e Información Rápida para obtener actualizaciones esenciales.
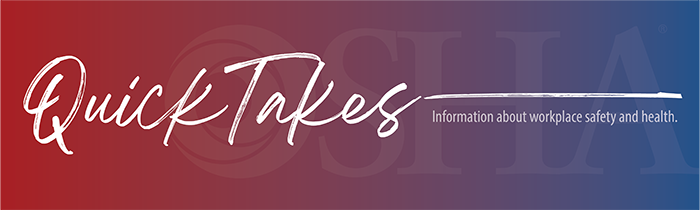
QuickTakes (English) | Did You Know? (Bilingual) Subscribe
OSHA COVID-19 Resources for the Food Processing Industries
Posters
- Steps to Protect Cleaning Staff During COVID-19 (Spanish).
- Steps to Reducing Worker Exposure to COVID-19 in Fish and Seafood Processing and Packaging Facilities.
- 9 Steps to Reducing Worker Exposure to COVID-19 in Meat, Poultry, and Pork Processing and Packaging Facilities.
Videos
Other Guidance
- Joint OSHA-FDA guidance: Employee Health and Food Safety Checklist for Human and Animal Food Operations During the COVID-19 Pandemic.
- Joint OSHA-CDC guidance, developed in consultation with FDA: Seafood Processing Workers and Employers.
- Joint OSHA-CDC guidance: Meat and Poultry Processing Workers and Employers (Spanish).
- COVID-19 Guidance on the Use of Cloth Face Coverings while Working Indoors in Hot and Humid Conditions.
OSHA COVID-19 Resources for Service Providing Industries
Alerts
- COVID-19 Guidance for In-Home Repair Services (Spanish).
- COVID-19 Guidance for Restaurants Resuming Dine-In Service (Spanish).
- COVID-19 Guidance for Food Truck Workers (Spanish).
- COVID-19 Guidance for Hair and Nail Salon Workers (Spanish).
- Retail Pharmacies (Spanish).
- Rideshare, Taxi, and Car Service Workers (Spanish).
- Restaurants & Beverage Vendors Offering Takeout or Curbside Pickup (Spanish).
- Package Delivery Workforce (Spanish).
- Retail Workers (Spanish).
Posters
- Steps to Protect Cleaning Staff During COVID-19 (Spanish).
- Steps to Protect Automotive Service Workers from Exposure to Coronavirus (Spanish).
Videos
OSHA COVID-19 Resources for the Healthcare Industry
Alerts
Posters
- Steps to Protect Cleaning Staff During COVID-19 (Spanish).
- Seven Steps to Correctly Wear a Respirator at Work (Spanish).
Other Guidance
- Respiratory Protection in Long-Term Care Facilities.
- Understanding Compliance with OSHA’s Respiratory Protection Standard During the Coronavirus Disease 2019 (COVID-19) Pandemic.
Enforcement Memoranda
- Temporary Enforcement Guidance - Tight-Fitting Powered Air Purifying Respirators (PAPRs) Used During the Coronavirus Disease 2019 (COVID-19) Pandemic.
- Enforcement Guidance on Decontamination of Filtering Facepiece Respirators in Healthcare During the Coronavirus Disease 2019 (COVID-19) Pandemic.
- Expanded Temporary Enforcement Guidance on Respiratory Protection Fit-Testing for N95 Filtering Facepieces in All Industries During the Coronavirus Disease 2019 (COVID-19) Pandemic.
- Enforcement Guidance for Use of Respiratory Protection Equipment Certified under Standards of Other Countries During the Coronavirus Disease 2019 (COVID-19) Pandemic.
- Enforcement Guidance for Respiratory Protection and the N95 Shortage Due to the Coronavirus Disease 2019 (COVID-19) Pandemic.
- Temporary Enforcement Guidance - Healthcare Respiratory Protection Annual Fit-Testing for N95 Filtering Facepieces During the COVID-19 Outbreak.
OSHA COVID-19 Resources for the Construction Industry
Alerts
Posters
- Ten Steps All Workplaces Can Take to Reduce Risk of Exposure to Coronavirus.
- Seven Steps to Correctly Wear a Respirator at Work.
Other Guidance
OSHA COVID-19 Resources for the Warehousing and Delivery Industries
Past Issues/Ediciones anteriores
2025
Issue |
---|
June 18, 2025 |
May 19, 2025 |
April 21, 2025 |
April 2, 2025 |
January 16, 2025 |
2024
2023
2025
Date | Issue |
---|---|
July 11, 2025 | DYK? Safe + Sound Week |
July 7, 2025 | DYK? Heat Safety |
July 2, 2025 | DYK? Fireworks Safety |
July 1, 2025 | DYK? Heat Safety |
June 23, 2025 | DYK? Heat Safety |
June 13, 2025 | DYK? Whistleblower Webinar |
June 12, 2025 | DYK? GHS Meeting |
June 5, 2025 | DYK? Letters of Interpretation |
May 20, 2025 | DYK? Mental Health Awareness Month |
April 28, 2025 | DYK? Workers Memorial Day |
April 25, 2025 | DYK? Heat Rule Hearing |
March 19, 2025 | DYK? Tornado Recovery |
January 13, 2025 | DYK?: Instagram and Facebook |
January 8, 2025 | DYK?: Winter Weather Hazards |
January 7, 2025 | DYK?: Chemical Exposure Data |
2024
2023
2025
Issue |
---|
18 de junio, 2025 |
19 de mayo, 2025 |
21 de abril, 2025 |
2 de abril, 2025 |
16 de enero, 2025 |