Poultry Processing Industry eTool
Poultry Processing Industry
In July 2024, poultry workers involved in avian influenza culling operations became infected with H5N1. In addition, H5N1 has been detected in dairy cattle and a small number of dairy workers who were exposed to infected animals have contracted the infection.
Workers should avoid unprotected exposure to dead animals/birds, animal waste, bedding, raw milk/uncooked animal products, or materials touched by, or close to animals with suspected or confirmed avian influenza. Workers who have unprotected exposure (no gloves, eye protection, or other personal protective equipment) with infected animals or their products (e.g., raw milk, raw cheeses, raw eggs) are at risk of infection.
Poultry and farm workers should avoid touching their face, nose, eyes, or mouth after touching farm animals or surfaces that may be contaminated with animal byproducts that may contain the virus.
For more information about how to protect yourself from Avian Influenza, see: Avian Influenza - Overview and H5N1 (Avian Influenza) in Dairy Cattle.
CAUTION Hazardous Industry
Since 1975, workers in this industry have consistently suffered injuries and illnesses at a rate more than twice the national average.
This eTool* focuses on identifying and controlling major hazards that contributed to the high rates of injuries. Other serious hazards are also discussed.
See OSHA's Workers' Rights page for more information on rights and protections.
Select a task from the illustration below to learn which hazards exist and possible solutions for controlling them.
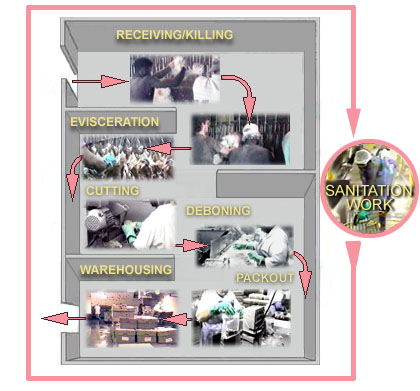
NOTE: Some manual tasks described may not be applicable to all facilities due to automation.
*eTools are stand-alone, interactive, highly illustrated web-based training tools on occupational safety and health topics. Some use expert system modules, which enable users to answer questions and receive reliable advice on how OSHA regulations apply to their work site. Some provide guidance information for developing a comprehensive safety and health program and include other recommended practices that often go beyond specific OSHA requirements. As indicated in the disclaimer, eTools do not create new OSHA requirements.