Poultry Processing Industry eTool
Tasks » Sanitation Worker
Sanitation Fatality
A sanitation worker at a poultry plant was cleaning out a chiller. The motor that powers the paddles inside the chiller was accidentally turned on by a coworker who was cleaning a different chiller. Neither the main power control nor the chiller control box had been locked or tagged out in accordance with 29 CFR 1910.147, The control of hazardous energy (lockout/tagout). The employee was struck by and caught between the rotating paddle blades and the interior wall of the chiller. He died of severe chest injuries approximately 28 hours after the accident.
Sanitation Fatality
In preparation for the next day's work, a clean-up crew was using a high pressure water hose to clean machines in a feather picking room. One of the two employees was preparing to wash down a feather picking machine, and the other was washing down a scalder machine. The first employee cranked open his machine to get inside and wash out feathers that had lodged throughout the machine during the feather picking process. Electric cords were pinched between the metal crank and the metal frame of this machine, and the insulation on the cords was pierced. As a result, an energized conductor was contacting the metal frame of the machine. Because the machine was turned off at the time, the employees were unaware of the condition of the cord. The first employee then moved between the two machines to begin the wash down. When he contacted the energized machine frame, he was electrocuted. His coworker received an electric shock when he tried to pull the first employee from the area. The second employee was hospitalized for his injury.
The job of a sanitation worker is one of the most hazardous jobs in the poultry processing industry. Sanitation workers may work a regular production shift, or they may be part of a special sanitation or cleaning crew.
The focus of sanitation workers who work a regular production shift is cleaning the machinery and floors. They move product to allow cleaning and use high pressure water hoses and squeegees to clean the floors. This type of job is frequently an entry-level position. Workers who hold these jobs do not have the experience needed to be familiar with the many hazards of the equipment and the environment in which they work. They need extensive training.
The daily sanitation or clean-up crew has the responsibility of cleaning all product contact surfaces throughout the plant to comply with requirements of the Food Safety and Inspection Service (FSIS), U.S. Department of Agriculture. If the clean-up crew has not done a satisfactory job, the FSIS inspector will not allow the plant to begin a production shift.
When the sanitation crew must remove guards or components to effectively clean processing equipment, and this action (or any other action) exposes crew members to hazardous energy, the equipment must be isolated from its energy source(s), and the energy isolation devices must be locked out or tagged out. In some situations, the equipment must be re-energized for a limited period of time for testing or repositioning purposed. During the testing or positioning period, a sequence of steps must be followed to maintain the integrity of employee protection, and alternative protection, such as removing workers from the machine area, must be provided to prevent employee exposure to machine hazards. Once the testing/positioning activity is completed, the equipment again must be de-energized and locked or tagged out and before undertaking further cleaning activities.
Depending on the part of the country in which the plant is located, the sanitation crew may be plant employees or they may work for a contractor. Again, they may be entry-level employees who need extra training to become familiar with the hazards of their work and ways to lessen the hazards.
An additional condition that may contribute to the hazardous nature of the work is that the crew may receive 8 hours' pay regardless of how early they finish the job. This gives them an incentive to work as fast as possible and may even contribute to taking short-cuts such as not locking or tagging out equipment.
The sanitation worker is exposed to most of the safety and health hazards throughout the plant, including:
Hazardous Situation
As workers remove blades from cutting equipment, they may receive cuts or lacerations. Any cut not treated at once will normally become infected as a result of working with poultry.
Possible Solutions
- Implement equipment lockout/tagout procedures,
- Provide cut-resistant gloves to workers who remove blades from equipment, and
- Clean and disinfect all cuts immediately.
Hazardous Situation
Sanitation workers cleaning powered equipment can get caught in the equipment if the motor is turned on. An example is getting caught in the paddles of chillers. Serious injury or death can result.
Possible Solutions
- Use the following effective protection for minor cleaning jobs that are routine, repetitive and performed as an essential part of the production process:
- Implement energy control (lockout/tagout) procedures.
- Proper use of interlocked barrier guards/gates.
- Use of properly designed control switches or buttons that are placed in the open/off safe positions when the devices are under the exclusive control of the employee performing the task.
- Train employees about the location and use of the control circuit devices.
- Implement equipment energy control (lockout/tagout) procedures for all other cleaning jobs.
Hazardous Situation
Employees climb on ladders or equipment to adequately reach all surfaces for cleaning. Falls can result in fractures or contusions.
Possible Solutions
- Make sure platforms or portable ladders are the appropriate size and height for the job and in good condition.
- Prohibit climbing on equipment.
Hazardous Situation
Employees trip over drain covers that have been removed during cleaning. Strains, sprains, and possible fractures may result.
Possible Solutions
- Replace drain covers as soon as the area is cleaned.
Hazardous Situation
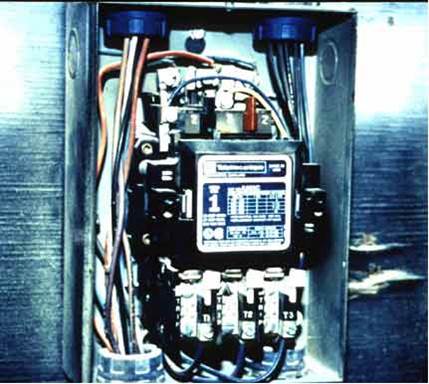
Employees may experience electrical shock from water contacting electrical connections or switch boxes or from improper reassembly of electric connections after disassembly for cleaning.
Possible Solutions
- Lockout and tag the electric circuit when it is possible to do so.
- Use and maintain proper wiring and grounding.
- Keep all electrical boxes covered.
- Use equipment approved for wet locations.
- Institute a regular inspection program looking for worn or improperly maintained electrical fixtures and equipment.
Hazardous Situation
Employees use chemicals, such as cleaners, that can cause skin or eye irritation or burns.
Possible Solutions
- Train employees on the hazards of the cleaners that they use.
- Provide gloves, protective eyewear, and other protective equipment to prevent skin and eye contact.
- Evaluate new application and chemical delivery systems prior to use so hazards and appropriate protective equipment can be identified.