Poultry Processing Industry eTool
Plant-Wide Hazards » Electrical Hazards
Specific OSHA Requirements
OSHA Requirements for the prevention of electrical hazards are contained in 29 CFR 1910 Subpart S, Electrical.
Paragraphs 29 CFR 1910.302 through 29 CFR 1910.308 cover Design Safety Standards for Electric Utilization Systems. 29 CFR 1910.331 through 29 CFR 1910.335 cover Electrical Safety-Related Work Practices.
Additional explanation of the OSHA requirements for electrical hazards can be found in OSHA's Small Business Safety and Health Handbook. OSHA Publication 2209, (2024) [Español OSHA Publication 4261, (2024)].
29 CFR 1910.137, Electrical protective equipment and 29 CFR 1910.147, The control of hazardous energy (lockout/tagout) are also applicable to the control of electrical hazards.
Controlling Electrical Hazards (PDF). OSHA Publication 3075, (2002). Gives an overview of the OSHA standards.
NOTE: Employers in states with state-run safety and health plans should check with their state agency. Their state may enforce standards that, while "as effective as federal standards," may not be identical to the federal requirements.
What are the hazards of electricity in the workplace?
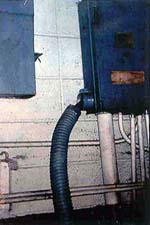
Electricity can result in:
- Electric shock,
- Electrocution,
- Burns (electrical or thermal contact),
- Fires,
- Explosions, and
- Indirectly, injury from a fall, from cuts, or from broken bones.
How does electric shock occur?
Electric shock occurs when the body becomes a part of an electric circuit. The electrical current must enter the body at one point and leave at another.
Electric shock normally occurs in 1 of 3 ways. Individuals - while in contact with the ground - must come in contact with:
- Both wires of the electric circuit, or
- One wire of an energized circuit and the ground, or
- A metallic part that has become "hot" by contact with an energized conductor
What are the causes of electrical accidents?
Summary: Fatal Electrocution in Poultry Processing Plant
Electrical accidents appear to be caused by a combination of 3 possible factors:
- Unsafe equipment and/or installation,
- Workplaces made unsafe by the environment, and
- Unsafe work practices.
In poultry processing facilities, the existence of wet environments greatly increases the risk of electrical accidents because water reduces the resistance of human skin to the passage of electricity. View examples.
OSHA's electrical standards help reduce the potential for death or serious injury by specifying safety aspects in the design and use of electrical equipment and systems. The standards cover only those parts of any electrical system that an employee would normally use or contact.
Motor Control Room
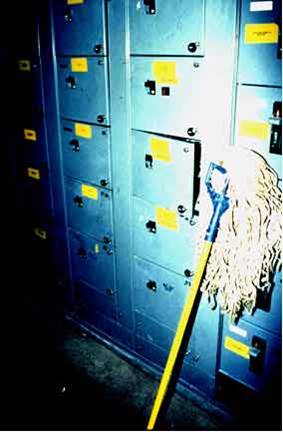
- Open eletrical panel in motor control room
- Wet mop stored at electrical disconnect
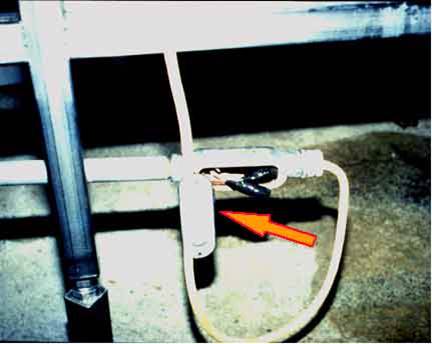
- Seal-tight cover not in place - wet area
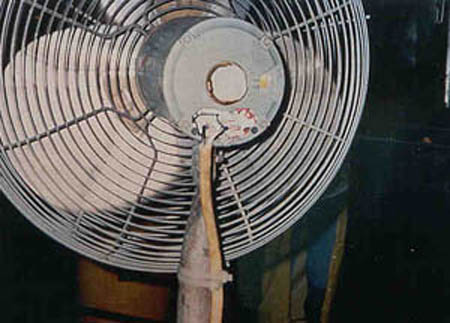
Fan
Methods of Protection
- Insulation
- Guarding
- Grounding
- Electrical protective devices
- Safe work practices
- Any material with high resistance to electric current - glass, mica, rubber, plastic.
- When intact and undamaged, prevents people from coming into accidental contact with current.
- Must be suitable for voltage and existing environmental conditions.
- Required for 50 or more volts.
- Methods
- Location - enclosure, screening, elevated area, or 8 feet or more above floor.
- Warning signs at entrances to guarded locations forbidding entrance of unqualified persons.
- Additional requirements for installations over 600 volts.
- Intentional creation of a low-resistance path to the earth in order to prevent buildup of voltages that may result in a personnel hazard.
- Reduces but does not eliminate possibility of shock, injury, or death.
- Types
- "Neutral conductor" or "grounded conductor"
- "Equipment ground"
- Designed to automatically limit or shut off the flow of electricity in the event of a ground-fault, overload, or short circuit.
- Types
- Fuses
- Circuit breakers
- Ground-fault circuit interrupters (GFCI)
- De-energizing electrical equipment before inspecting or making repairs.
- Using appropriate protective equipment.
- Using electric tools that are in good repair.
- Using good judgment when working near energized lines.
How can workers be protected from the hazards of electricity?
The basic means of protection include:
Electrical
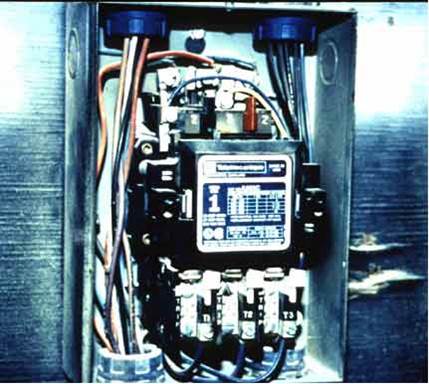
Open electrical box - 480 V. 3-phase
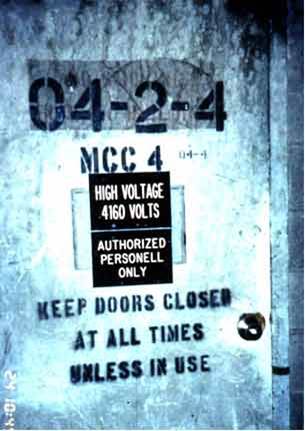
Motor control room not locked when voltage greater than 600 volts.
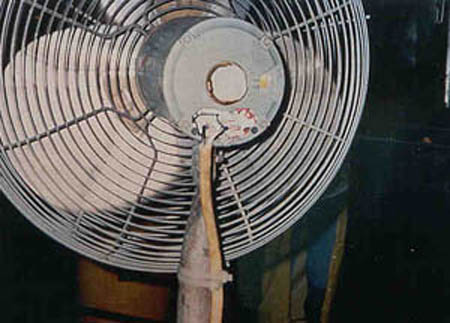
Fan
- Insulation - covering live parts with high-resistance material such as rubber or plastic. (Always check the insulation on power cords before connecting to a power source to be sure there are no exposed wires. Flexible cords, such as extension cords, are particularly likely to be damaged.) View example.
- Guarding exposed live parts from access by unqualified persons. View examples.
- Grounding, both system and equipment. (Never use equipment from which the grounding prong has been removed, or use an adapter to connect a 3-pronged tool to a 2-pronged outlet.) View example.
- Electrical protective devices – fuses, circuit breakers, and GFCIs. [The GFCI is intended to protect employees by interrupting the current quickly enough to prevent electrocution. If a GFCI detects a current difference (going to versus coming from electrical equipment) greater than 6 amperes, it will shut off electric power within 1/40 of a second.] View examples.
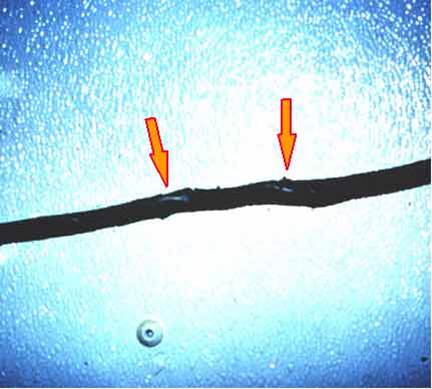
Damaged/repaired cord on a floor fan.
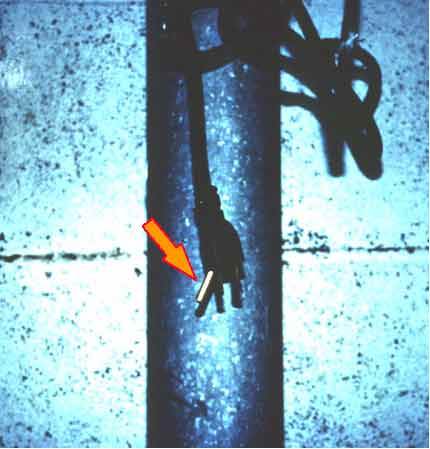
Ground pin broken on floor fan cord.
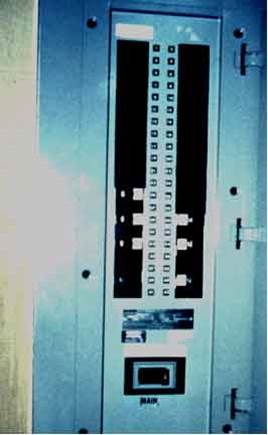
Breakers in panel not identified
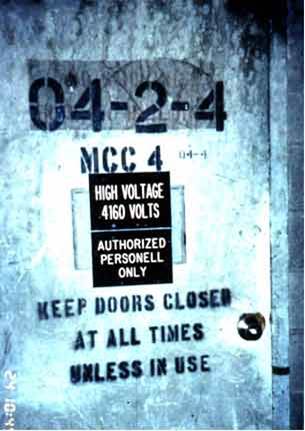
Circuit tester
Safe Work Practices
Employees working with electrical equipment need to use safe work practices, including:
Electrical
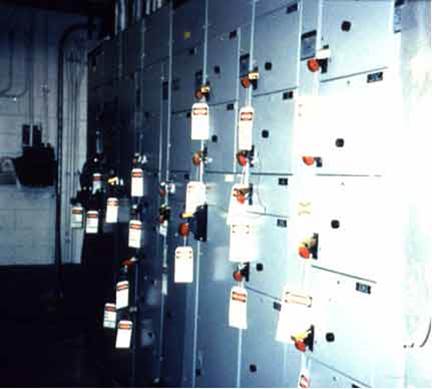
- Single lockout used for entire work crew
- No group lockout used
- Lockout/tagout hazards
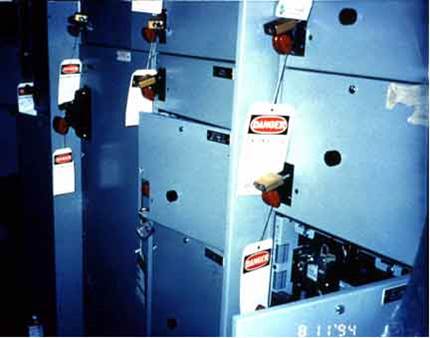
- Open live electrical circuits
- No group lockout used
- De-energizing and locking out and appropriately tagging electric equipment before inspecting or making repairs (View examples);
- Using electric tools that are in good repair; tools that are in questionable repair should be removed from service and tagged;
- Using good judgment when working near energized lines; unqualified employees and mechanical equipment must stay at least 10 feet away from overhead power lines; and
- Using appropriate protective equipment, such as rubber insulating gloves, hoods, sleeves, matting, blankets, line hose, and industrial protective helmets.
What training is required about electrical hazards?
Employees must be:
- Aware of the electrical hazards to which they are exposed;
- Trained in safety-related work practices, including lockout/tagout; and
- Trained in any other procedures necessary for safety from electrical hazards.
Maintenance employees who perform electrical repairs should be qualified electricians.