Hurricane eMatrix
Hurricane eMatrix » General Recommendations for Working in All Impacted Areas
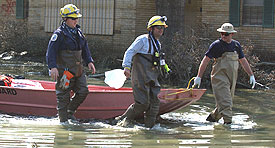
This picture shows actual disaster site work conditions and may not illustrate proper safety and health procedures.
Introduction
Response and recovery work in hurricane-impacted areas presents safety and health hazards that should be properly identified, evaluated, and controlled in a systematic manner to reduce or eliminate occupational safety and health risks to response and recovery workers. This Matrix provides information on assessing and controlling the hazards common to most response and recovery work in hurricane-impacted areas. Although this document was developed from data and experiences arising out of response and recovery work following Hurricanes Katrina and Rita, this document may also be applied to response and recovery work following future hurricanes, floods, and other natural disasters.
Response and recovery workers in hurricane-impacted areas encounter hazards ranging from contact with live electrical equipment to animal bites. This Matrix outlines hazard-specific considerations for monitoring exposures, implementing engineering controls, establishing work practices, requiring the use of PPE, and providing necessary training. Employers can use the general recommendations outlined below and the task- and operation-specific activity sheets to evaluate the work their workers will do and to eliminate or control the hazards to which they may be exposed. This section concludes with a list of online resources that address health and safety concerns in a hurricane response zone.
Limitations and Disclaimer
The Matrix does not provide an in-depth analysis of OSHA standards and regulations and cannot address all hazards. It does not increase or diminish any OSHA requirements or employer obligation under those requirements. It is intended as a guide and quick reference for employers and response and recovery workers. The Matrix captures major activities involved in hurricane response and recovery, highlights many of the hazards associated with them, and recommends "best practices." Employers must evaluate the specific hazards associated with the job/operation at the site where the work is being performed.
Employers are responsible for providing a safe and healthful workplace for their workers. OSHA's role is to assure the safety and health of America's workers by setting and enforcing standards; providing training, outreach, and education; establishing partnerships; and encouraging continual improvement in workplace safety and health.
The Hazard Exposure and Risk Assessment Matrix for Hurricane Response and Recovery Work provides a general overview of particular topics related to current OSHA standards. It does not alter or determine compliance responsibilities in OSHA standards or the Occupational Safety and Health Act of 1970, or the equivalent State Plan standards and requirements. Because interpretations and enforcement policy may change over time, you should consult current OSHA/State Plan administrative interpretations and decisions by the Occupational Safety and Health Review Commission and the courts for additional guidance on OSHA compliance requirements. Employers should modify their procedures as appropriate when additional, relevant information becomes available.
Best Practices for Hurricane Response and Recovery Operations
Worksite Evaluation
Evaluate the work site to identify if safety or health hazards such as the following are present: fall, electrocution, noise, cut/laceration hazards; high ambient temperatures; hazardous substances; or infectious materials.
Exposure Monitoring
As appropriate, conduct task-specific exposure monitoring during response and recovery activities as follows:
-
When required by a specific standard (e.g., as specified in OSHA standards for lead, asbestos, benzene, and noise).
-
When exposure is reasonably anticipated to be greater than the "action level," as required by an individual OSHA substance-specific standard. This is recommended for assessing exposure to other chemicals that response and recovery workers may be exposed to. Screening data, previous sampling results, and anecdotal information may be evaluated to assess an worker's anticipated exposure.
(Note: If not otherwise established by a standard, the "action level" can be defined as 50% of an established occupational exposure level. OSHA sets occupational exposure limits called Permissible Exposure Limits (PELs), which are legal requirements. Other organizations set occupational exposure guidelines, which are non-mandatory recommendations.)
Occupational exposure levels are set to protect workers from the short- and long-term harmful health effects that may be associated with chemical (e.g., vapors, particulates, fibers) and physical agents (e.g., heat, noise, vibration). Exposure limits may be expressed as 8-hour time-weighted averages, or may be expressed for shorter exposures, such as ceiling levels or 15-minute short-term exposure levels.
-
When necessary to assess and evaluate specific worker exposure or to investigate and resolve worker complaints or concerns.
-
To verify the adequacy of the implemented hazard control methods.
Consider the contaminants normally associated with the task/operation and those associated with the site conditions resulting from the effects of the hurricane (e.g., release of unknown chemicals, entry into confined spaces that may now be permit-required). Ask workers about how they perform the task/operation, to obtain useful information about the equipment and materials used and the conditions under which the task/operation is performed.
When specific chemical and physical hazards may be present and the risk of overexposure cannot be conclusively ruled out, employers may confirm their presence or absence by screening for them using direct reading instruments (e.g., oxygen meters, combustible gas indicators, and noise meters) or by collecting and analyzing grab samples. Although the results from grab samples and direct reading instruments can be used to estimate individual exposures, use full-shift or short-term personal monitoring as the primary means of assessing individual exposure. Include in sampling documentation a clear description of the task/operation being done, how the samples were collected, and an evaluation of the results. Report sampling results, monitoring data, and any resulting follow-up to workers and their representatives in accordance with the requirements of any applicable standards. When a sample characterizes the exposure of one or more response and recovery workers involved in a task, get contact information for all of the individuals involved, so that each can be notified of the results and of any follow-up medical surveillance recommended.
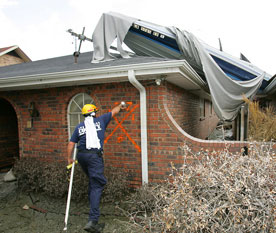
This picture shows actual disaster site work conditions and may not illustrate proper safety and health procedures.
As past emergency response activities have demonstrated, it is important to share hazard and exposure monitoring data among response and recovery organizations. OSHA has posted summaries of its sampling data and exposure information for Hurricanes Katrina/Rita/Wilma on the OSHA Website. To assist employers and response and recovery workers in assessing risk and making decisions about exposure controls such as personal protective equipment (PPE) and respiratory protection, OSHA has included a detailed discussion of Agency sampling data in the Summary of Activity Sampling Data and Safety and Health Monitoring Information. This information has also been included, where appropriate, in individual Matrix activity sheets. Data may also be shared at interagency coordination centers, such as the Joint Field Offices (JFOs), and be used to support the event-specific policies and protocols identified in an incident or site-specific health and safety plan (HASP). Follow the procedures outlined in the HASP to ensure that response and recovery safety and health hazards are consistently addressed and information is collected and shared appropriately.
Other agencies, such as the EPA and State environmental and public health agencies, have also posted sampling data on their websites. When evaluating sampling data from other agencies, note that occupational exposure data needs to be interpreted in the proper context. It has different risk implications from environmental and public health data, which is collected for comparison with exposure levels established to protect the public or environment.
Hazard Control
Mitigate hazards according to the hierarchy of controls listed below:
- Elimination or substitution: Whenever possible, eliminate the hazard from the work area (e.g., repair or remove fallen electrical power lines before allowing other work to proceed in the area). Although desirable, elimination and substitution may not be options for most airborne/chemical hazards created by a natural disaster.
- Engineering controls: Take steps to reduce or eliminate exposure to a hazard, such as by guarding the pinch points associated with a machine's moving parts, providing ventilation to a permit-required confined space, using heavy equipment with temperature-controlled cabs, and placing barriers around the swing radius of rotating heavy equipment.
-
Work practice or administrative controls: Implement work procedures that reduce the probability of exposure. For example, use well-rested crews and daylight hours to perform higher hazard or unfamiliar tasks, take frequent breaks during hot weather, remove non-essential personnel from the area during certain task/operations, and decontaminate equipment and personnel after contact with contaminated floodwater or chemicals. When possible, use water to suppress dust and work up-wind in dusty conditions. Where extensive hot work is performed in the form of cutting and burning, use extended length torch handles to increase the distance from the individual's breathing zone to the generation of toxic fumes.
Performing specific Job Hazard Analyses (JHAs) often will identify important work practice controls. OSHA provides additional assistance on developing JHAs. See Job Hazards Analysis (OSHA Publication 3071, 2002).
-
Personal protective equipment (PPE): If other controls are not available, infeasible, or do not provide sufficient protection, select and use PPE appropriate for the hazard and level of exposure. OSHA provides additional assistance on selecting and using PPE. See OSHA's Personal Protective Equipment (PPE) Safety and Health Topics Page.
Work Practices
The following work practices provide for basic safety, sanitation, and good housekeeping. These practices minimize exposure to health hazards and contaminants during most activities.
- Establish and maintain evacuation routes and an alerting system to notify individuals in case an evacuation becomes necessary.
- Provide, maintain, and inspect fire protection and suppression equipment for the fire hazards in the work area.
- Ensure that first aid supplies and services, and medical care are readily available.
- Drink water from sources proven to be safe for drinking.
- Do not consume food or beverages that were exposed to floodwaters or perishables that may have spoiled. Additionally, do not eat, drink, or smoke in areas containing debris, floodwaters, or sludge.
- Wash hands before eating, drinking, smoking, or using the restroom. If potable water is not available, use hand sanitizer or commercial sanitizing wipes.
- Minimize accumulation of trash and keep garbage in closed containers.
- Use insect repellent containing DEET or Picaridin to prevent insect bites.
- Minimize the creation or disturbance of dust and work upwind of dusty activities when possible.
- Provide prompt first aid for cuts and scrapes. Antibiotic resistant bacteria can result in severe injury and illness. Wash and sanitize cuts and scrapes without delay and report the injury to your supervisor. Bandage/cover cuts and scrapes and keep them from coming in contact with polluted or contaminated floodwater. Seek medical help at the first sign of infection.
Recommended Personal Gear
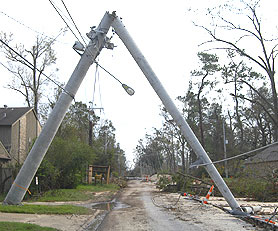
This picture shows actual disaster site work conditions and may not illustrate proper safety and health procedures.
- Ensure you have personal information such as immunization record and blood type.
- Consider bringing the following gear:
- Rain gear
- Changes of clothing appropriate for the location, weather, and assignment
- Toiletries (in plastic rather than glass bottles)
- Alcohol-based hand sanitizer
- Flashlight with spare batteries
- Prescription medicine for expected length of stay (with considerable safety margin)
- Over-the-counter medications for minor illnesses (e.g., pain reliever, allergy medication, hydrocortisone cream, antibiotic cream, bandages)
- Sunscreen (SPF-15 or higher)
- Lip salve
- Insect repellent
- Cap or hat for sun and rain
- Extra pair of glasses or contacts (If you wear contacts, anticipate dusty conditions at disaster sites)
- Sun glasses
Personal Protective Equipment (PPE)
Assess the workplace hazards, select PPE that will protect workers from these hazards, and ensure that workers use the PPE selected. Equipment must be properly fitted to the worker. Train workers in the use, operation, and limitations of equipment, as well as how to put on and remove the equipment properly (i.e., donning and doffing techniques). Inspect equipment before each use and repair or replace as needed (e.g., when ripped, torn). Maintain and store PPE in a clean and sanitary manner. Maintain adequate supplies for timely replacement of lost, worn, or broken PPE. (For additional OSHA guidance on selecting and using PPE, see OSHA's Personal Protective Equipment (PPE) Safety and Health Topics Page.
General PPE recommended for all response/recovery tasks:
- Foot protection: ANSI-approved protective footwear for the activity being performed. Give special consideration to water protection in wet or flooded areas.
- Eye protection: Safety glasses with side shields. (OSHA has published additional guidance on the selection and use of face and eye protection; this is available on OSHA's Eye and Face Protection Safety and Health Topics Page.
- Head protection: Hard hats or helmets in areas where overhead or electrical hazards exist.
- Appropriate work clothing: Clothing appropriate for protecting individuals from hazards in the general work environment that may cause cuts, abrasions, irritation, or overexposure to sunlight. Consideration should be given to heat and cold stress issues.
- Hand protection: Gloves specific to job hazards (e.g., heavy-duty leather work gloves for handling debris with sharp edges and/or chemical protective gloves appropriate for chemicals potentially contacted). See the OSHA Fact Sheet on the this topic for additional OSHA-published guidance on hand hygiene and glove use in hurricane-affected areas.
Provide the following additional PPE, as required:
- Eye and face protection (specialty): Goggles, full-face shields, or other suitable protection as needed to protect against flying objects and liquid splash hazards.
- High-visibility apparel: High-visibility safety apparel and headwear compliant with ANSI/ISEA 107-2004, along with other traffic safety measures, in areas where vehicles or heavy equipment are used. This is especially important when working in temporary roadway work zones. (See the OSHA Fact Sheet on this topic for additional OSHA-published materials on work zone traffic safety.)
- Hand protection (specialty): Appropriate gloves suitable for the tasks being performed (balancing dexterity with protection). Considerations include biological hazards (bloodborne pathogens), chemical hazards, and physical hazards (abrasions, cuts, punctures, and heat). Vibration-dampening gloves should be used when vibration hazards exist (e.g., during jackhammer use)
- Work clothing and gear (specialty): Lanyards, harnesses, and supports for fall protection, and chemical protective clothing where contact with chemicals may occur.
- Leg protection: Snake boots or snake gaiters to protect against snakebites in areas where snakes are indigenous. Chaps when using chain saws.
-
Respiratory protection: The mandatory use of respirators requires compliance with the OSHA respiratory protection standard (29 CFR 1910.134), including the development of a written respiratory protection program that describes how respirators will be cleaned, maintained, and stored; a filter or cartridge change out schedule based on the work expected; and how workers will receive medical evaluations, training, and fit testing. Voluntary use of respirators must conform to Appendix D of 29 CFR 1910.134.
While it is the employer's responsibility to determine the appropriate respiratory protection for a given situation, the following general guidance can be used in making risk assessment decisions for hurricane response activities. When airborne contaminants exceed, or may reasonably be expected to exceed, allowable exposure limits, evaluate the hazard to determine exposure, and provide appropriate respiratory protection.
- Where nuisance levels (exposures below the PEL) of dust or mold are present, use of a NIOSH-approved N, R, or P95 filtering facepiece is recommended. Those with a layer of activated carbon provide an additional level of comfort for workers by controlling nuisance odors.
- Where contaminants such as lead, asbestos, or silica are present, respirators appropriate for the anticipated level of exposure are required. These could include, at a minimum:
- N, R, or P100 air-purifying respirators for lead and asbestos, and
-
N, R, or P95 air-purifying respirators for crystalline silica; N, R, or P100 will provide additional protection for documented over exposures.
-
Where other contaminants exist, specific filters or cartridges appropriate to the contaminant must be used; combination cartridges and filters must be used, as necessary.
In all cases, surgical masks and dust masks that are not NIOSH-approved are not considered suitable respiratory protective devices.
Additional OSHA-published guidance on the use of respirators is available on OSHA's Respiratory Protection Safety and Health Topics Page.
See also the NIOSH Respirator Selection Logic 2004 publication.
-
Photo courtesy of FEMA.
This picture shows actual disaster site work conditions and may not illustrate proper safety and health procedures.Protection from drowning: Workers working on, over, or near water that presents a drowning hazard (e.g., because of the flow rate, the depth, or the presence of rocks) must wear appropriate personal floatation devices (PFDs), approved by the US Coast Guard. Additional devices-such as a lifesaving skiff and a ring buoy-must be provided in accordance with 29 CFR 1926.106.
-
Hearing protection: Workers should wear earmuffs and/or earplugs when working around potential noise sources. Hearing protection must be worn when noise levels exceed 90 dBA.
When hurricane recovery tasks or operations are covered by OSHA's General Industry Standards, OSHA requires that individuals who have standard threshold shifts use hearing protection when noise levels exceed 85 dBA. A useful "rule of thumb:" if you cannot hold a conversation in a normal speaking voice with a person who is standing at arms length (approximately 3 feet), the noise level may exceed 90 dBA. (See OSHA's Occupational Noise Exposure Safety and Health Topics Page for additional OSHA-published information on noise and hearing conservation programs.)
Specialized PPE ensembles and procedures are required for protecting workers involved in activities that expose them to other hazards for which additional protection and procedures are needed (e.g., structural firefighting, confined-space entry, response to hazardous materials releases, asbestos abatement, lead abatement, welding, cutting, and burning). Evaluate working conditions, provide any additional training to address the hazard, and assign appropriate PPE in accordance with applicable standards (e.g., OSHA, NFPA).
Training
Train workers engaged in hurricane response and recovery operations to recognize and avoid the hazards to which they may be exposed while performing their jobs. This training may be composed of the following elements:
- Job-specific training necessary for workers to develop the skills needed to perform their assigned task/operation.
- Task- or operation-specific training on how to perform the job safely, including any training mandated by specific standards. This may include training/information related to hazard communication, hazardous waste cleanup and emergency response, selection and use of PPE, work with lead and asbestos, use of tools, and working safely at elevations.
- Training about the general hazards, conditions, and work expected to be performed. Training should be conducted before workers are deployed. Discuss common stressors for response and recovery workers, such as extended work shifts, acclimatization issues, less than ideal sleeping and eating conditions, and critical incident stress concerns.
- Site-specific training that covers the hazardous conditions and exposures that workers may encounter at a particular location. Identify specific controls such as specialized equipment, work practices, and additional PPE necessary for the particular job site. These controls may be identified in a Job Hazard Analysis (JHA) developed for the task or operation.
- Daily job briefings covering the day's work plan, anticipated hazards, and required exposure controls.
Maintain records of worker training and make these available for inspection by agencies having jurisdiction. Training records include training certificates, attendance rosters, and course curricula.
NOTE: Contracts with private employers to assist in the response and recovery should specify the particular safety and health training for which the contractor is responsible.
Medical Considerations
Medical screenings, physical exams and respirator clearances are required by certain OSHA standards for workers. Examples include workers who routinely use or are exposed to lead, asbestos, and other regulated chemicals, or are required to wear PPE (e.g., respirators) because of their jobs.
Evaluate the work that workers will be performing in hurricane-impacted areas. Use this information in consultation with a physician or other licensed health care professional, to identify any additional medical examinations, tests, or vaccinations required.
The Centers for Disease Prevention and Control (CDC) has published Interim Immunization Recommendations for Disaster Responders.
Recommendations for General Hazards Commonly Encountered during Hurricane Response and Recovery Operations
Certain hazards are commonly encountered in most hurricane response and recovery activities and require protective measures to control or mitigate their effects. In this section, engineering controls, work practices, and appropriate PPE are described for these common hazards. Hazards that are unique to specific hurricane response and recovery activities and their associated protective measures are separately addressed in the individual activity sheets.
Structural Instability
- Limit access/set up controlled access zones until the structure's stability and structural integrity are known.
- Conduct all necessary activities from outside damaged structures to the extent feasible.
- Ensure that a competent person evaluates the structure's stability when access is necessary. A competent person is able to recognize existing and predictable hazardous conditions and has the authority to take prompt corrective measures to eliminate the hazardous conditions.
- Install temporary structural support (shoring, bracing) adequate to protect response and recovery workers.
Contact with Downed Lines, Live Electrical Equipment, and Other Utilities (e.g., gas, water)
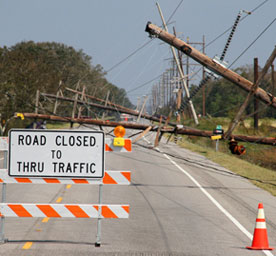
This picture shows actual disaster site work conditions and may not illustrate proper safety and health procedures.
- Identify the location of any energized electrical power circuit that workers (or their tools and equipment) could contact; post signs and advise individuals of the location, hazards, and protective work practices.
- Assume that electrical lines are energized until proven otherwise. Lines and other conductors may become reenergized without warning as utilities are evaluated and restored after a disaster. Ensure that workers are protected from electric shock by deenergizing and grounding circuits they might contact.
- Inspect the work area for downed conductors and do not go near, drive over, or otherwise come in contact with them.
- Downed electrical conductors can energize other objects, including fences, water pipes, bushes, trees, and telephone/CATV/fiber optic cables.
- Unless they are deenergized and visibly grounded, maintain proper distance from overhead electrical power lines (at least 10 feet) and/or provide insulating barriers.
- Deenergize circuits and use locks and/or tags to prevent circuits from becoming reenergized accidentally.
- Use ground-fault circuit interrupters on all outlets that are not part of permanent wiring.
- Guard live parts against accidental contact using approved cabinets or other approved enclosures.
- Inspect electrical cords or cables for external defects (such as loose parts, deformed or missing pins, or damage to outer jacket or insulation) and for evidence of possible internal damage (such as pinched or crushed outer jackets). Do not use damaged cords and cables.
- Use extension cords approved for the intended use (e.g., use heavy duty extension cords on work sites).
- Do not approach any gas leaks; if a gas leak is detected, secure spark-producing devices (e.g., engines, tools, electronic, and communications equipment) and evacuate the area until the leak is secured.
- Contact utility company to assist in locating, marking, and shutting off/purging utility lines that may pose a hazard or may be impacted; ensure that lines have been purged as needed before beginning work.
OSHA and CDC maintain web pages that address electrical hazards. These pages include:
- Working Safely Around Downed Electrical Wires. OSHA Fact Sheet.
- Protect Yourself and Others from Electrical Hazards After a Disaster. Centers for Disease Control and Protection (CDC).
Unexpected Start-up of Machines or Equipment, or Release of Stored Energy during Servicing and Maintaining Machines and Equipment
- Implement an existing energy control program or develop a site-specific program that addresses how workers will be protected from unexpected start-up and/or release of stored energy during servicing and maintaining machines and equipment.
- Where such hazards exist, train workers on the energy control program, as required by 29 CFR 1910.147(c)(7).
- Control procedures will include the following:
- Shutoff machines and equipment using established procedures.
- Ensure that each authorized worker places a lockout or tagout device on each energy isolating device.
- Relieve, disconnect, or restrain all potentially stored hazardous or residual energy.
- Verify isolation using test procedures before beginning work.
- Ensure that locks and tags are only removed by the authorized worker.
- Prior to returning machine or equipment to normal operation, replace and reactivate all safeguards and remove all locks and tags.
OSHA provides a fact sheet on Lockout/Tagout.
OSHA also has a Control of Hazardous Energy (Lockout/Tagout) Safety and Health Topics Page that provides employers and workers with additional information and useful online resources.
Noise
- Place generators, compressors, and other noisy equipment at a distance or behind a barrier.
- Move noisy operations to isolated areas or away from other tasks or operations.
- Locate work areas such as observation towers, office trailers, and break areas away from noisy operations.
- Keep unnecessary response and recovery workers out of areas near noisy operations.
- Provide enclosed cabs on heavy equipment.
- Collect noise monitoring data to determine if workers are exposed to noise levels that exceed 90 dBA.
- Use hearing protection as required when working around potential noise sources such as heavy equipment, debris chippers, chainsaws, and jackhammers. Hearing protection must be worn when noise levels exceed 90 dBA. (When hurricane recovery tasks or operations are covered by OSHA's General Industry Standards, OSHA requires that individuals who have standard threshold shifts use hearing protection when noise levels exceed 85 dBA.)
- A useful "rule of thumb:" if you cannot hold a conversation in a normal speaking voice with a person who is standing at arms length (approximately 3 feet), the noise level may exceed 90 dBA.
- Implement a hearing conservation program when noise levels exceed permissible levels in the workplace.
OSHA has a Occupational Noise Exposure Safety and Health Topics Page that provides employers and workers with additional information and useful online resources.
Fall from Heights and Through Openings
- Limit access/set up controlled access zones.
- Use fall protection systems: guardrails, safety nets, or fall arrest systems (as needed). A personal fall arrest system includes harnesses, lanyards, lifelines, connectors, anchorages, and anchor points.
- Cover or guard holes and openings as soon as they are created. Covers must support two times the weight (body, equipment, materials) that may be imposed. Permanently mark covers over holes "Danger – Opening."
Asbestos
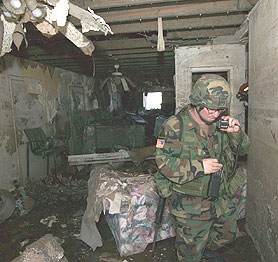
This picture shows actual disaster site work conditions and may not illustrate proper safety and health procedures.
- Consider the potential for Asbestos Containing Materials (ACM). Structures built before 1980 are more likely to contain ACM.
- If available, review the building operations and maintenance plan and ACM survey to determine the locations and types of ACM in building.
- Thermal system insulation (formed or spray-on) is the ACM of greatest concern for response and recovery worker exposure.
- Other materials that may contain asbestos include: vinyl floor tile, home siding & shingles, transite (including cement piping), flame retardant materials (e.g., gloves, curtains) and roof flashing.
- If building is suspected or known to contain asbestos-containing thermal system insulation, ensure a qualified individual, such as a competent person, a person certified as an asbestos inspector by the State, or a safety and health professional, inspects the building and evaluates the condition of the material prior to any remediation or cleanup of ACM or PACM by other response and recovery workers.
- If asbestos is located, do not disturb the material and isolate the area until the material can be visually inspected for integrity.
- If removal is necessary to complete work, ACM must be removed by workers who are trained to perform the class of abatement work they will conduct, using the methods identified in 29 CFR 1926.1101. ACM must be discarded in a landfill that has a permit to accept ACM.
- Based on the initial exposure assessment, select a respirator and other protective clothing for visual inspection, sampling, and subsequent abatement work.
- Workers who will be required to remove ACM must receive asbestos training, as outlined in 29 CFR 1926.1101, for the class of work they will perform. See 29 CFR 1926.1101(k)(9) for additional asbestos-specific training information.
- An asbestos-specific medical surveillance program, as outlined in 29 CFR 1926.1101(m), is required for workers working with asbestos for 30 or more days per year (1) who may be exposed at or above the permissible exposure limit or (2) who are likely to conduct Class I, II, or III asbestos abatement activities.
- OSHA provides several web pages that address asbestos hazards. These pages include:
Lead
- Identify building materials such as painted surfaces and pipes that may contain lead. Test materials as necessary
- Based on test results, perform an worker exposure assessment of the planned activities, that includes air monitoring and/or objective data, to determine if lead dust or fume may be generated at or above OSHA's action level (0.03 milligrams of lead per cubic meter of air (mg/m3))
- If so, then the activities must be done in compliance with 29 CFR 1926.62. This would include:
- Establishing a written lead compliance program
- Having a competent person conduct frequent and regular inspections of the jobsite, materials, and equipment
- Sampling worker exposures
- Using special equipment or methods to decrease lead-dust generation such as local exhaust ventilation, dust collection systems (on power tools), and good housekeeping practices
- Providing respiratory protection and protective work clothing
- Providing medical exams and blood tests before work begins and every six months, as necessary
- Ensuring that workers wash their hands and face before eating, drinking, and smoking
- Setting up and ensuring use of change areas and eating facilities that are separate from the work area
- Limiting the wearing of lead-contaminated clothing in eating areas or away from the job site
- During certain tasks, workers must be treated as if they are exposed above the OSHA PEL (0.05 mg/m3) until an exposure assessment, which includes air sampling, is performed. For each of these tasks, OSHA has identified an exposure level on which to base decisions until an exposure assessment is complete. If planned activities include any of the tasks below, you must provide the following items while the exposure assessment is being performed: respiratory protection and PPE identified in 29 CFR 1926.62(d)(2), change areas, hand washing facilities, training, and biological monitoring. These tasks include:
- Where lead coatings or paint are present: manual demolition, scraping, and sanding; heat gun applications; power tool cleaning (with or without dust collection systems); cleanup activities where dry expandable abrasives are used; rivet busting; abrasive blasting (including enclosure movement or removal); welding; cutting; and torch burning
- Spray painting with lead paint
- Using lead containing mortar
- Lead burning
- Workers shall be provided lead training before starting work involving lead exposures at or above the action level. See 29 CFR 1926.62(l) for additional lead-specific training information.
- Workers who may be exposed above the action level for lead for a single day must be enrolled in an initial medical monitoring program. Additionally, workers who are exposed to lead levels at or above the action level for more than 30 days in any consecutive 12 months must be enrolled in a medical surveillance program, as outlined in 29 CFR 1926.62(j).
- OSHA provides several web pages that address lead hazards. These pages include:
- Lead. OSHA Safety and Health Topics Page.
- Protecting Workers from Lead Hazards. OSHA Fact Sheet.
Impact Hazard to Eyes and Face from Flying Objects
- Use safety glasses with side shields to protect eyes from flying fragments, objects, large chips, and particles.
- Wear safety goggles, which form a protective seal around the eye, to protect against flying fragments, objects, large chips and particles when these could get under or around safety glasses (e.g., wind gusts).
- Use face shields when impact from flying objects, such as glass chips, could damage skin (due to their size, shape, velocity). Face shields protect a larger area of the face, but do not protect eyes from strong impacts. If a face shield is selected, eye protection (e.g., safety glasses or goggles) must be worn under the face shield.
- All eye and face protection should meet ANSI Z87.1 performance requirements.
- OSHA has a web page that provides information and online resources for selecting and using face and eye protection.
Manual Handling of Materials/Weight
- Use safe lifting practices; keep the weight as close to you as possible; and involve extra people or mechanical devices (e.g.,dollies or hoists) as needed.
- Take frequent rest breaks when lifting heavy or water-laden objects.
- OSHA has a web page that provides information and online resources on ergonomics and manual handling of materials and weights.
Discovery of Unknown Chemicals
- If hazardous chemical containers are found or leaking materials are detected, take self-protective measures (i.e., move to a safe distance upwind) and contact hazardous material response personnel (e.g., Environmental Protection Agency (EPA) or U.S. Coast Guard (USCG) personnel) for evaluation of the risk and removal before continuing work in the area.
- Evaluate the need to revise protective clothing, respirator, and glove selection.
- If personnel are likely to witness or discover a hazardous substance release such as a large spill of fuel, oil, corrosives, or other chemicals, train them under the Hazardous Waste Operations and Emergency Response (HAZWOPER) standard, 29 CFR 1910.120(q)(6) or 29 CFR 1926.65(q)(6).
- OSHA has several web pages that provide information and online resources on hazardous substances, hazard communications, and HAZWOPER. These pages include:
- Chemical Hazards and Toxic Substances. OSHA Safety and Health Topics Page.
- Hazard Communication. OSHA Safety and Health Topics Page.
- Hazardous Waste. OSHA Safety and Health Topics Page.
- The Application of HAZWOPER to Worksite Response and Cleanup Activities. OSHA.
Cuts and Lacerations
- Keep work areas and travel paths free of trip hazards when worker activities (or work areas) involve sharp items/debris.
- When cuts or lacerations occur, provide first aid and seek medical attention promptly if cut/laceration becomes infected.
- Use heavy-duty work gloves and sturdy clothing when shifting or moving materials.
- To prevent contact with contaminated water or blood/body fluids, cover cuts and lacerations with bandages and use fluid-proof gloves (e.g., latex, nitrile, rubber) and clothing to prevent penetration to the underlying skin. Cover fluid-proof gloves with heavy-duty work gloves if there is a potential for cuts and abrasions (e.g., moving debris).
- Report any exposure to blood or body fluids to your supervisor.
Slips, Trips, and Falls on Working Surfaces
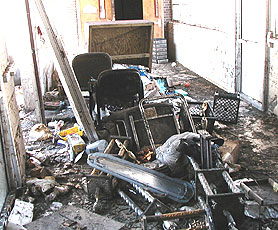
This picture shows actual disaster site work conditions and may not illustrate proper safety and health procedures.
- Establish travel paths or walkways through work areas. Keep them clear to minimize trip hazards. Remove dropped objects from pathways immediately.
- Ensure that additional equipment brought to the location does not create or pose additional slip, trip, and fall hazards.
- Keep electric cords and cables and pneumatic lines out of travel paths and walkways. If this is not feasible, protect the cord to avoid creating trip hazards and to prevent damage to the cords, cables, and lines.
- Establish barriers and/or mark areas around known hazards such as holes and overhead hazards.
- Take extra care when stepping onto unstable or uneven surfaces, and onto surfaces where the hazard cannot be seen (e.g., underwater surfaces).
- Clean up spilled material as soon as practical to avoid creating a slip hazard.
- Install steps and ramps and properly maintain them. Include slip-resistant treads and smooth handrails that will not cause punctures or lacerations.
- Provide sufficient lighting to safely illuminate work areas.
- OSHA has a web page that provides information and online resources on walking/working surfaces.
Personal Hygiene and General Decontamination
Hand Washing
- Wash hands for at least 10 seconds with soap and water (if available). This includes all surfaces such as the wrists, palms, backs of hands, fingers, and fingernails.
- If soap and/or water are not available, use alcohol-based products made for washing hands, such as hand sanitizer or sanitizing wipes. Wash all hand surfaces by gently rubbing. Allow hands to air dry.
- Clean the dirt from under your fingernails.
- Rinse the soap from your hands.
- Dry your hands completely with a clean towel. If towels are not available let your hands air-dry. When drying your hands using a towel, pat your skin rather than rubbing it to avoid chapping and cracking.
- Discard any disposable towels in the trash.
- OSHA provides a fact sheet on Hand Hygiene and Protective Gloves in Hurricane-Affected Areas.
Clothing, Tools, and Equipment Decontamination
- Clean contaminated clothing, tools and equipment (that can be decontaminated using water) with soap and clean water (if available). If only contaminated water is available, use a solution of the following ratio:
- 1/4-cup bleach.
- 1 gallon of water.
- Immerse equipment or tools in the cleaning solution for 10 minutes or, for larger objects, wipe objects with the solution and let stand for 10 minutes.
- Allow tools or equipment to drain and air dry.
- Immerse clothing in the cleaning solution for 10 minutes and gently swirl clothing every few minutes.
- Wring out as much moisture as possible from clothing before rinsing items.
- Allow clothes to thoroughly dry before using again.
- OSHA provides a fact sheet on general decontamination.
Decontaminating PPE and Equipment Used with Hazardous Substances
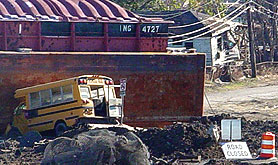
This picture shows actual disaster site work conditions and may not illustrate proper safety and health procedures.
- Minimize contact with hazardous substances (e.g., do not walk through areas of obvious contamination).
- Use remote sampling, handling, and container opening techniques where possible.
- Wear disposable outer garments and use disposable equipment where appropriate.
- Select a method of decontamination that is effective for the likely contaminate, the PPE material(s), and the type or level of PPE being worn. For many substances, washing with soap and rinsing with water will be effective. For some materials (e.g., dusts and particulates), consider vacuuming first and then washing and rinsing PPE.
- For emergency response and hazardous waste clean-up operations, select and mark the area where decontamination will occur. Ensure that it is upwind of the operation and immediately adjacent to the work site or "hot zone."
- Decontaminate and remove all PPE. Start with the PPE that is most contaminated and work towards the equipment that is the least contaminated. Do not remove respiratory protection until all outer garments are decontaminated and removed.
- Decontamination may be completed in stages, which may require a large decontamination area. If this is the case, the area should be covered with plastic sheeting or another waterproof barrier to reduce the amount of cross-contamination from foot traffic, wash/rinse splash and other decontamination steps.
- Discard all PPE and accumulated decontamination wash/rinse solutions in accordance with local, State, or Federal requirements.
- Once PPE is decontaminated and removed, wash areas covered by PPE. For example, if only hand protection was used, then washing and rinsing the hands would be sufficient. If the individual used Level B protection and was fully covered in dermal and respiratory protection, then the individual would need to shower.
- For certain contaminants, such as asbestos and lead, decontamination procedures are well defined and must be followed. They generally adhere to the steps noted above, but may require that the decontamination area be designed and constructed in a specific manner.
- See OSHA's Asbestos and Lead Safety and Health Topics Pages.
- For additional information on decontaminating PPE and equipment, see the Occupational Safety and Health Guidance Manual for Hazardous Waste Site Activities, Chapter 10.
Fatigue and Stress
- Provide adequate sleep, meal, and rest breaks to minimize accidents due to fatigue and stress.
- Conduct higher-hazard or new activities during daylight hours using well-rested workers.
- Consider that individuals may experience signs or symptoms of critical incident stress and provide appropriate services such as pre- and post-deployment briefings and access to behavioral health professionals.
- Provide resources and information that address psychological first-aid issues and assistance.
Heat Stress
- When possible, acclimatize response and recovery workers to hot and humid environments by gradually increasing their work period or workload over the course of several days.
- Reduce physical exertion levels by providing extra individuals.
- Schedule heavy work for cooler periods of the work shift (e.g., early mornings, cool/overcast days).
- When possible, provide temperature-controlled cabs for equipment operators.
- When possible, and where appropriate, use fans/ventilation to provide air movement for cooling.
- Take frequent rest/water breaks in areas that are shaded or air conditioned.
- Drink 4 to 8 ounces of water or sports drink every 20 minutes while working in hot, humid conditions.
- Limit fluids to no more that 1 ½ quarts per hour when working in hot, humid conditions. Do not drink more than a total of 12 quarts of fluid in 24 hours.
- Limit the intake of caffeinated and alcoholic beverages.
- Wear light-colored clothing.
- Know the signs and symptoms of heat stress; use the buddy system to monitor one another for these signs/symptoms.
- If someone shows signs of heat stress (exhaustion or stroke), request immediate medical attention, move the individual to a cooler area in the shade, loosen or remove restrictive or heavy clothing, provide cool drinking water, and fan and mist the person with water.
- Consider the use of personal cooling devices. Examples of cooling devices include cooling vests or suits that use circulating water or ice packs, and venturi cooling systems for air-supplied respirators or encapsulating suits.
- OSHA and NIOSH provide web pages that discuss heat stress.
Cold Stress
- Monitor ambient conditions (ambient temperature and wind velocity) and plan work activities so that outside work is conducted during the warmer parts of the day or rescheduled for days that are predicted to be warmer.
- When possible, move work indoors or to an area that is protected from the wind/precipitation.
- Wear layers of clothing that are windproof and waterproof. Consider keeping additional clothing with you and changing into dry clothing as soon as possible after work clothing becomes wet.
- Take frequent rest breaks in warm, sheltered spaces.
- Drink plenty of fluids to prevent dehydration and limit the intake of caffeinated beverages.
- Know the signs and symptoms of cold stress (pain and numbness in extremities, excessive fatigue, severe uncontrollable shivering, drowsiness, irritability) and use the buddy system to monitor one another for these signs/symptoms.
- If someone shows signs of cold stress (frostbite or hypothermia), request immediate medical attention, move the individual to a warmer area in a sheltered space, remove cold or wet clothing, provide warm fluids, and monitor the person.
- OSHA has several documents that discuss cold stress, hypothermia, and protective measures. These documents include:
Animal Bites, Stings, and Aggressive Behavior
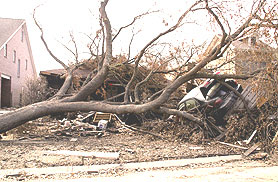
This picture shows actual disaster site work conditions and may not illustrate proper safety and health procedures.
- Use insect repellent containing DEET or Picaridin on exposed skin and wear long-sleeved pants and shirts.
- Discuss hazardous wildlife (e.g., alligators, poisonous snakes) concerns with personnel familiar with these matters (e.g., game wardens, animal control officers).
- Inspect areas for nests and stray animals.
- Remove all nearby sources of stagnant or standing water.
- Assume that all snakes are poisonous and that all animals are rabid.
- Be on guard for stray or wild animals, as they can exhibit unpredictable or aggressive behavior.
- Unless properly trained, do not attempt to take custody of animals—watch them from a safe distance while contacting animal rescue/control personnel.
- Be cautious about where you place your hands and feet. Do not put your hands in holes or under objects (e.g., lumber, scrap metal, overturned boats) without checking to see if snakes, insects, or other animals are present.
- Do not sit or lie down in areas where snakes, insects, or other animals could be present (e.g., wood piles, high vegetation).
- Wear proper foot gear, such as high-top leather boots and leather gloves when handling materials where snakes, insects, and other animals may have nested (e.g., firewood, lumber, rocks, construction debris).
- Inspect and shake out clothing and shoes before getting dressed.
- Deer ticks are carriers of Lyme disease. When working in high grass, cover exposed skin with long sleeves and pants as weather permits. Report all tick bites to medical personnel.
Contact with Poisonous Plants
- Train response and recovery workers on hazardous plant recognition.
- Keep rubbing alcohol accessible, as it may remove the oily resin from plants such as poison ivy up to 30 minutes after exposure.
- When appropriate, safely clear vegetation from areas were personnel are working and living (e.g., construction trailers, base camps).
- Use gloves and wear long pants and long-sleeved shirts when possibly contacting poisonous plants.
- Use a barrier cream formulated to protect against poison ivy/oak.
Sunburn
- Wear suntan lotion with a sun protection factor (SPF) of 15 or greater. Reapply as necessary to ensure protection throughout the work shift.
- When possible, wear a wide brim hat to protect exposed skin on face, head, and neck.
- When possible, set up work area in a shaded location.
- When possible, schedule tasks when individuals will not be exposed to direct sunlight such as during the early morning or late afternoon.
General References
The following references (CDC, NIOSH, NIH, NIEHS, EPA) may be consulted for additional information on safety and health issues during hurricane response and recovery activities.
- Hurricane Preparedness and Response. OSHA. Includes information such as news releases, public service announcements, fact sheets, frequently asked questions, and more.
- Cleanup Hazards. OSHA Fact Sheet, (September, 2005).
- Flood Cleanup. OSHA Fact Sheet, (September, 2005).
- Occupational Safety and Health Guidance Manual for Hazardous Waste Site Activities. National Institute for Occupational Safety and Health (NIOSH)/Occupational Safety and Health Administration (OSHA)/US Coast Guard (USCG)/Environmental Protection Agency (EPA), (1985).
- Safety Information for Response and Cleanup Workers. Centers for Disease Control and Prevention (CDC).
- Immunization Recommendations for Disaster Responders. Centers for Disease Control and Prevention (CDC), (September 10, 2008).
- Storm, Flood, and Hurricane Response - Guidance for Post-exposure Medical Screening of Workers Leaving Hurricane Disaster Recovery Areas. National Institute for Occupational Safety and Health (NIOSH), (June 18, 2010).
- Dealing with Debris and Damaged Buildings. Environmental Protection Agency (EPA), (August 13, 2009).
- Potential Environmental Health Hazards When Returning to Homes and Businesses. Environmental Protection Agency (EPA), (August 13, 2009).