Quicktakes Newsletter Series
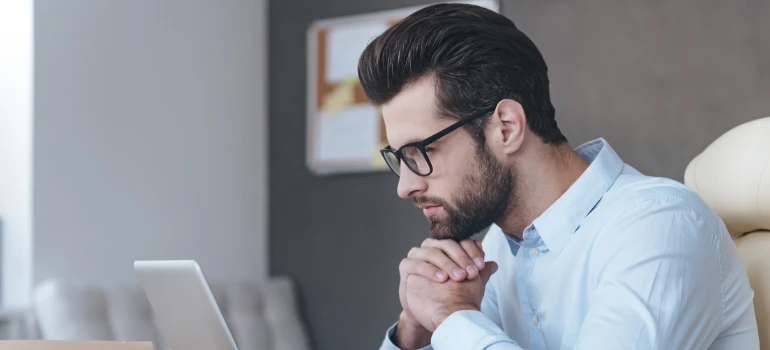
Like this information?
Subscribe to stay connected.
QuickTakes
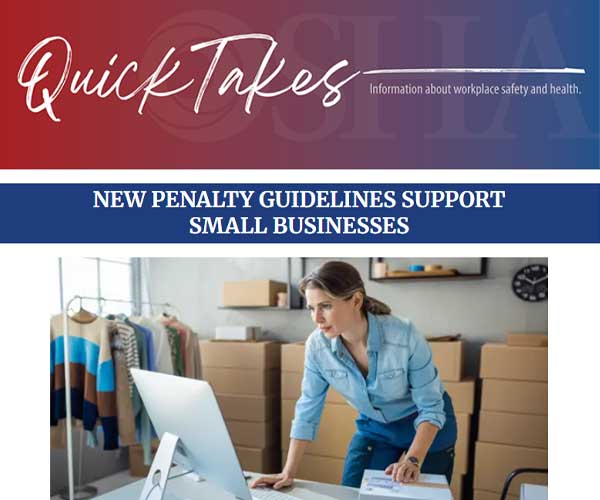
Monthly newsletter featuring compliance assistance, training and other workplace safety and health resources.
Información Rápida
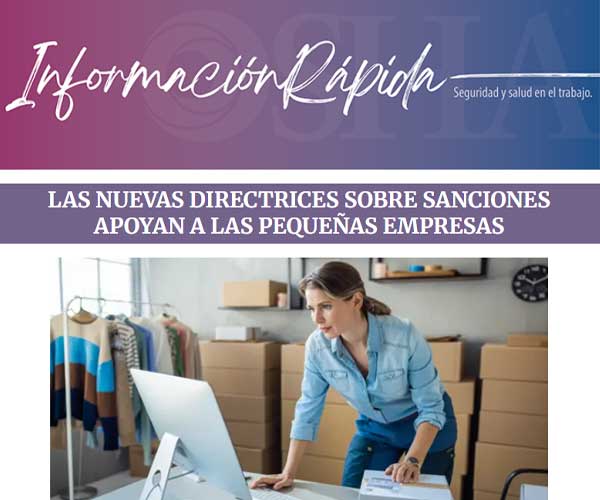
Boletín mensual que ofrece asistencia en materia de cumplimiento, capacitación y otros recursos de seguridad y salud en el lugar de trabajo.
DYK?
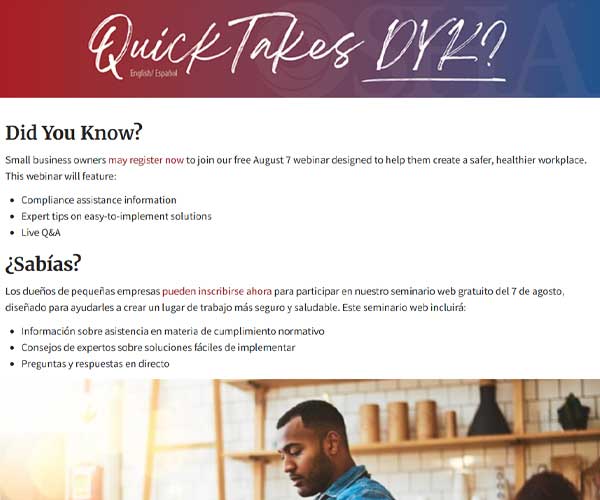
Short, informative bulletin spotlighting timely workplace safety events and resources/Boletín breve e informativo que destaca eventos y recursos importantes sobre seguridad en el lugar de trabajo.
Past Issues/Ediciones anteriores
2025
Issue |
---|
July 21, 2025 |
June 18, 2025 |
May 19, 2025 |
April 21, 2025 |
April 2, 2025 |
January 16, 2025 |
2024
2023
2025
Date | Issue |
---|---|
August 13, 2025 | DYK? Combustible Dust Hazards |
August 12, 2025 | DYK? Whistleblower Protection Webinar |
August 8, 2025 | DYK? Job Safety Analysis Webinar |
August 5, 2025 | DYK? Safe + Sound Week |
July 29, 2025 | DYK? Small Business Webinar |
July 28, 2025 | DYK? Heat Safety |
July 24, 2025 | DYK? Meeting Employers Where They Are |
July 22, 2025 | DYK? Heat Safety |
July 16, 2025 | DYK? Heat Safety |
July 11, 2025 | DYK? Safe + Sound Week |
July 7, 2025 | DYK? Heat Safety |
July 2, 2025 | DYK? Fireworks Safety |
July 1, 2025 | DYK? Heat Safety |
June 23, 2025 | DYK? Heat Safety |
June 13, 2025 | DYK? Whistleblower Webinar |
June 12, 2025 | DYK? GHS Meeting |
June 5, 2025 | DYK? Letters of Interpretation |
May 20, 2025 | DYK? Mental Health Awareness Month |
April 28, 2025 | DYK? Workers Memorial Day |
April 25, 2025 | DYK? Heat Rule Hearing |
March 19, 2025 | DYK? Tornado Recovery |
January 13, 2025 | DYK?: Instagram and Facebook |
January 8, 2025 | DYK?: Winter Weather Hazards |
January 7, 2025 | DYK?: Chemical Exposure Data |
2024
2023
2025
Issue |
---|
21 de julio, 2025 |
18 de junio, 2025 |
19 de mayo, 2025 |
21 de abril, 2025 |
2 de abril, 2025 |
16 de enero, 2025 |
2024
2023
2025
Issue |
---|
July 14, 2025 |