Woodworking eTool
Rough Mill Equipment » Table Saws
Table saws are used for straight sawing. Depending on the blade, they cut either across (crosscut) or with (ripsaw) the grain of the wood.
Operator Involvement
With the hand-fed saws, the operator adjusts the height and angle of the blade. Then, holding the stock, the operator pushes it into the blade. A guide is used to maintain a straight cut at the desired width. At the end of the cutting stroke, the operator either changes positions or pushes the stock past the blade. Self-feed or power table saws are equipped with rollers or a conveyor system to hold the lumber and force-feed it into the saw blade.
Potential Hazard
-
Point of operation - Injuries can occur if an operator's hands slip as he or she is feeding the stock into the saw or if the operator holds his or her hands too close to the blades while cutting. The operator can also be injured when removing scrap or finished pieces from the table.
Possible Solutions
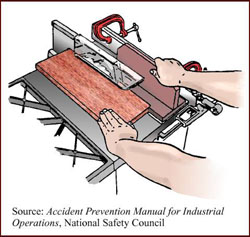
Engineering Controls
-
Ripsaws and crosscut saws. Enclose the portion of the saw above the table with a self-adjusting guard (Fig. 1). The guard must adjust to the thickness of the material being cut and remain in contact with it [29 CFR 1910.213 (c)(1) and (d)(1)]. Hinge the guard so that the blades can be easily changed.
-
Attach a brake to the motor's arbor to stop the saw from coasting after it has been cut off, or have the operator remain at the saw station once the motor is shut off until the blade stops turning.
Work Practices
-
Keep hands out of the line of the cut.
-
Use a push stick for small pieces of wood and for pushing stock past the blade. [29 CFR 1910.213(s)(9)].
Potential Hazard
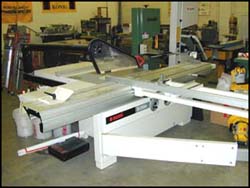
- Other moving parts - Contact with the blade under the table, or with the power transmission apparatus (if not enclosed), may occur.
Possible Solution
Engineering Controls
- Always guard the portion of the blade below the table. Operators must be protected from possible contact when reaching under the table [29 CFR 1910.213(a)(12)].
Potential Hazard
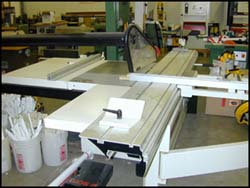
-
Kickbacks (that is, when the blade catches the stock and throws it back toward the operator) are another major cause of injury. Kickbacks can result if the blade height is not correct or if the blade is not properly maintained. Kickbacks are more likely to occur when ripping, rather than crosscutting. Kickbacks also can occur if safe-guards are not used or if poor-quality lumber is cut.
Possible Solution
Engineering Controls
- For ripsaws, use a spreader to prevent material from squeezing the saw or kicking back during ripping [29 CFR 1910.213(c)(2)]. Use anti-kickback fingers to hold the stock down in the event that the saw kicks back the material [29 CFR 1910.213(c)(3)].
Work Practices
-
Use proper blade for cutting action (for example, don't use crosscut blade for ripping).
-
Operate saw at speed specified by the manufacturer.
-
Maintain and sharpen blade [29 CFR 1910.213(s)(2)].
-
Leave sufficient clearance for stock.
-
Stand to side of the saw blade to avoid injury due to kickback.
-
Guide stock parallel to the rip fence to minimize the potential for kickback.
-
Avoid crosscutting long boards on table saws. Considerable hand pressure is required close to the saw blade, and the boards create a safety hazard to other people.
-
Use a filler piece between the fence and the saw blade when necessary (e.g., when there is little clearance on the fence side).
-
Properly support all pieces of stock, including the cut and uncut ends, scrap, and finished product.
Potential Hazard
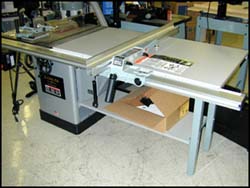
- Flying particles - Wood chips, splinters, and broken saw teeth may be thrown by the cutting action of the blade.
Possible Solution
Work Practices
- Remove cracked saw blades from service [29 CFR 1910.213(s)(7)].