Woodworking eTool
Packaging/Shipping » Ergonomics
Products vary in weight - up to 100 pounds - and are shipped from the wood shop in a variety of containers. The shape, weight, and/or material of the package can greatly affect the stress that an employee experiences. Material is usually moved through the shop on pallet jacks.
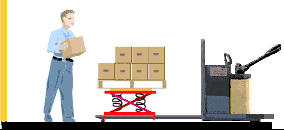
-
>> Ergonomics
Potential Hazard
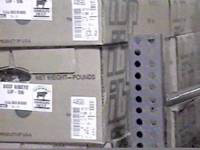
-
Many boxes are excessively heavy, weighing as much as 100 pounds. Manually lifting loads in this weight range places great stress on the employee's muscles. Back injuries such as muscle strain and disc injury can occur when repeatedly lifting heavy objects.
Possible Solutions
-
Improve access to the heaviest items. Employees should be able to access these items without bending at the waist, pulling the elbows away from body while reaching, or twisting. Redesigning storage racks and transport devices can greatly improve the employee's ability to maintain neutral postures.
-
Provide handhold cutouts or handles on all heavy products.
-
Work with suppliers to ensure that container integrity will be adequate so boxes, bags, or buckets will not accidentally break, rip, or pull apart during lifting operations.
-
Fig 2 - Load heavier packages on outside. Load pallets with the lighter product in the center and the heavier product on the outer edges to ensure easier access and lifting of the heavier items.
Potential Hazard
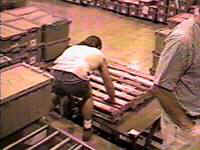
-
Wooden pallets weigh between 40 and 70 pounds and may be lifted several times during a work shift. This repeated lifting can cause stress to the lower back.
-
Splinters from handling the wood are also a hazard to the worker.
Possible Solutions
-
Fig 4 - Plastic pallets weigh 20 to 30 pounds. Use lighter, plastic pallets.
-
Plastic pallets easily nest together to reduce the space of stacking. They also eliminate splinters and uneven surfaces that employees may step on when walking over pallets.
-
Fig 5 - Pallet dispenser reduces handling. Provide a pallet dispenser to reduce pallet handling. This device allows selectors to drive their pallet jack to the dispenser. An empty pallet is then automatically loaded onto the forks without manual lifting.
Potential Hazard
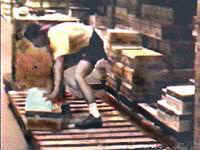
-
Employees repeatedly bend forward at the waist to place the product on the lowest level of the pallets.
-
The heaviest units are placed on the bottom layer for stability. This work process requires employees to lift the heaviest loads using the worst body postures.
Possible Solutions
-
Fig 7 - Use of a forklift raises the height of the load. Raise the height of the bottom level to allow employees to keep the load close to the body, as shown in the figure to the right. This will minimize bending of the torso.
-
Fig 8 - Pallet jack with higher than normal fork elevation. Provide height-adjustable equipment so loads can be maintained at a height that minimizes bending at the waist. This pallet jack raises up to 10 inches, while many others raise 8 inches or less.
-
Fig 9 - Stacked pallets elevate the load. Stack extra empty pallets on the pallet jack to elevate the bottom of the load.
-
Fig 10 - A palletizer on a pallet jack raises the product. View Animation
Place a palletizer on the forks of the pallet jack to keep product at waist height.
-
Educate employees about the hazards of bending while moving heavy loads. Ensure the use of proper lifting techniques.
-
When possible, utilize power equipment rather than manual labor to reduce ergonomic stresses.
Back belts: The effectiveness of back belts in reducing the risk of back injury among healthy workers remains unproven. If workers falsely believe they are protected when wearing belts, they may attempt to lift more than they would without a belt. This poses a risk of injury to the worker (See Back Belts: Do They Prevent Injury? (DHHS) (NIOSH) Publication No. 94-127).
Potential Hazards
-
Over long periods of time the solid rubber wheels of pallet jacks and forklifts can develop flat spots resulting in unstable loads and poor handling. Employees can experience stress to the hands and arms from difficulty in steering and stopping.
-
Worn floors create ruts and bumps.
Possible Solutions
-
Provide periodic maintenance of pallet jacks and fork lifts so they can operate with the minimum amount of hand, arm, and finger force.
-
Provide training to selectors so they recognize the early signs of mechanical breakdown. This will allow them to report problems or difficulties with the machine before the problems lead to injury.
-
Keep floors well maintained, with no ruts or bumps, to reduce the force needed when using manual material-handling equipment and whole body vibration/shock from driven equipment.
For more information, refer to the following:
-
Powered Industrial Trucks (Forklift Trucks). OSHA Safety and Health Topics Page.