Respiratory Protection eTool
Respiratory Protection » Respirator Change Schedules
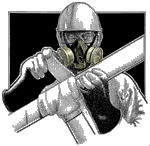
Did you know that employers are required to provide a respirator cartridge change schedule? See the requirements for change schedules.
Respirator cartridges don't last forever!
A change schedule is the part of the written respirator program which says how often cartridges should be replaced and what information was relied upon to make this judgment. A cartridge's useful service life is how long it provides adequate protection from harmful chemicals in the air. The service life of a cartridge depends upon many factors, including environmental conditions, breathing rate, cartridge filtering capacity, and the amount of contaminants in the air. It is suggested that employers apply a safety factor to the service life estimate to assure that the change schedule is a conservative estimate.
If you know what the chemical is and how much of it you are exposed to, then you are ready to estimate out how long your respirator cartridges will work and apply the safety factor.
Three valid ways for you to estimate a cartridge's service life
1. Conduct Experimental Tests
- Can save money by providing a more accurate service life value instead of relying on conservative assumptions made by other methods.
- Most reliable method, especially for multiple contaminants.
- Can be used to validate an existing change schedule.
- Will likely take time and money to perform the tests.
2. Use the Manufacturer's Recommendation
- Can result in a more accurate estimate for your particular brand of respirator.
- Relies on the manufacturer's broad knowledge and expertise.
- May not be possible if the manufacturer is unable to provide a recommendation.
- May not account for all workplace and user factors adequately.
3. Use a Math Model
- Inexpensive and takes little time.
- Requires no math calculations if you use NIOSH's MultiVapor™ Version 2.2.3 Application.
- Not as accurate as experimental testing. May result in a service life estimate that is shorter than it needs to be due to conservative assumptions.
- Generally limited to single contaminant situations.
Keep In Mind
- You may not rely on odor thresholds and other warning properties as the primary basis for determining the service life of gas and vapor cartridges and canisters.
- You should account for environmental and user factors and use a conservative approach when evaluating service life testing data.
- You should apply a safety factor to any estimate to account for uncertainty.
- Mixtures, intermittent use and concentrations, storage practices and other variables may require the use of an administrative time limit, e.g. one day, even though the estimated life would be longer.
- An example of a decision logic tree which could be used when evaluating a workplace for use of air purifying respirators is presented in these pages.
- There is a published "Rule of Thumb" that may provide a rough estimation of cartridge service life. However, you should NOT use this as the sole method of determining service life.
OSHA Requirements for Change Schedules
The following is a synopsis of some of the requirements of the standard.
- Employers develop cartridge/canister change schedules based on available data or information. Such information includes the exposure assessment and information based on breakthrough test data, mathematically based estimates, and/or reliable use recommendations from the employer's respirator and/or chemical suppliers.
- Reliance on odor thresholds and other warning properties will not be permitted as the primary basis for determining the service life of gas and vapor cartridges and canisters.
- OSHA emphasizes that a conservative approach is recommended when evaluating service life testing data. Temperature, humidity, air flow through the filter, the work rate, and the presence of other potential interfering chemicals in the workplace all can have a serious effect on the service life of an air-purifying cartridge or canister.
The standard requirements for change schedules are found in 29 CFR 1910.134(d)(3)(iii)(B)(2).
For enforcement policy and guidance, see the OSHA Directive for Inspection procedures for the Respiratory Protection Standard.
For additional background material, see the OSHA Preamble to Final Rules for Respiratory Protection.
OSHA Requirements for Change Schedules
The following is a synopsis of some of the requirements of the standard.
- Employers develop cartridge/canister change schedules based on available data or information. Such information includes the exposure assessment and information based on breakthrough test data, mathematically based estimates, and/or reliable use recommendations from the employer's respirator and/or chemical suppliers.
- Reliance on odor thresholds and other warning properties will not be permitted as the primary basis for determining the service life of gas and vapor cartridges and canisters.
- OSHA emphasizes that a conservative approach is recommended when evaluating service life testing data. Temperature, humidity, air flow through the filter, the work rate, and the presence of other potential interfering chemicals in the workplace all can have a serious effect on the service life of an air-purifying cartridge or canister.
The standard requirements for change schedules are found in 29 CFR 1910.134(d)(3)(iii)(B)(2).
For enforcement policy and guidance, see the OSHA Directive for Inspection procedures for the Respiratory Protection Standard.
For additional background material, see the OSHA Preamble to Final Rules for Respiratory Protection.
Factors That Can Reduce Cartridge Service Life
Worker Exertion Level: a worker breathing twice as fast as another will draw twice the amount of contaminant through the respirator cartridge
The service life of a cartridge or canister respirator depends upon the total amount of contaminant captured by the absorbent. The total amount of captured contaminant is directly related to the work rate or breathing rate; i.e., a worker breathing twice as fast as another will draw twice the amount of contaminant through the respirator cartridge. Most cartridge studies have used a breathing rate, 50-60 liters per minute, that approximates a high end of moderate work rate. For work rates that exceed this level (e.g., heavy shoveling, running) you may need to apply or take into account a correction factor when determining a service life.
Respirator Cartridge Variability: some cartridges contain more activated charcoal than others
The service life of a respirator cartridge is directly related to the amount of active material in the cartridge. For instance, most dual cartridge organic vapor respirators contain between 35-50 grams of activated charcoal in each cartridge. If the specific cartridge being evaluated can be reproducibly determined to have a certain amount of active material, then modifications to the service life may be justified. You can obtain information on cartridge specifications from manufacturers.
Temperature: the hotter it is, the shorter the service life
High temperatures can adversely affect the adsorptive capacity of respirator cartridges and canisters. The high temperature may act by thermally loosening the attractive forces that make adsorption happen or may act in concert with humidity by increasing the moisture carrying capacity of air. This latter mechanism may represent the greatest likely effect on service lives of cartridges. Temperature effects alone have been reported to reduce the service life 1-10% for every 10 degrees Celsius rise depending on the specific solvent (Nelson, et. al., 1976). Corrections to cartridge estimated service life for this effect alone are probably not necessary under normal working temperatures.
Relative Humidity: water vapor will compete with the organic vapors for active sites on the adsorbent
Relative Humidity is a measure of the amount of water vapor the air will hold at a specified temperature and is expressed in percentage values. Since warmer air will hold more water than colder air, the same relative humidity at a higher temperature represents a significantly greater amount of moisture. High relative humidity is a significant negative factor in the capacity of organic vapor cartridges since the large quantity of water vapor will compete with the organic vapors for active sites on the adsorbent. Most of the laboratory work determining adsorbent capacity has been performed at a low relative humidity of 50% at approximately 70 degrees F.
If the actual use of the organic vapor respirators will take place in a significantly more humid environment, then you may need to apply or take into account a safety factor when determining a service life. The exact magnitude of the humidity effect is complex, dependent in part upon chemical characteristics and concentrations of both the contaminant and the water vapor. Based upon relatively few studies, a reduction by a factor of 2 in the cartridge service life originally estimated based upon 50 % relative humidity, may be made when the relative humidity reaches 65% (Nelson, et. al., 1976; Werner, 1985). If the relative humidity exceeds 85%, you should consider experimental testing or another method to more specifically determine the service life. Mathematical modeling may be an appropriate, albeit complex, approach to predict the effect of humidity at various chemical concentrations (Wood, 1987; Underhill, 1987).
Multiple Contaminants: predictions should be derived from the least well adsorbed compound
Multiple contaminants introduce a great deal of variability into the prediction of service life for respirator cartridges. Much of the laboratory testing and the mathematical models have utilized a single contaminant to determine service lives. Only a limited number of multiple contaminant situations have been studied and reported in the literature (e.g. Yoon, 1996; Jonas et. al., 1986). Cartridge service life for mixtures of compounds with significantly different chemical characteristics is probably best determined by experimental methods. Predictions based upon models without experimental data should probably be very conservative and ascribe the service life derived from the least well adsorbed compound to the total mixture concentration in terms of parts per million. The displacement of a less well adsorbed compound by a more highly adsorbed one may alter the actual service life from the estimated one in some cases.
Factors That Can Reduce Cartridge Service Life
Worker Exertion Level: a worker breathing twice as fast as another will draw twice the amount of contaminant through the respirator cartridge
The service life of a cartridge or canister respirator depends upon the total amount of contaminant captured by the absorbent. The total amount of captured contaminant is directly related to the work rate or breathing rate; i.e., a worker breathing twice as fast as another will draw twice the amount of contaminant through the respirator cartridge. Most cartridge studies have used a breathing rate, 50-60 liters per minute, that approximates a high end of moderate work rate. For work rates that exceed this level (e.g., heavy shoveling, running) you may need to apply or take into account a correction factor when determining a service life.
Respirator Cartridge Variability: some cartridges contain more activated charcoal than others
The service life of a respirator cartridge is directly related to the amount of active material in the cartridge. For instance, most dual cartridge organic vapor respirators contain between 35-50 grams of activated charcoal in each cartridge. If the specific cartridge being evaluated can be reproducibly determined to have a certain amount of active material, then modifications to the service life may be justified. You can obtain information on cartridge specifications from manufacturers.
Temperature: the hotter it is, the shorter the service life
High temperatures can adversely affect the adsorptive capacity of respirator cartridges and canisters. The high temperature may act by thermally loosening the attractive forces that make adsorption happen or may act in concert with humidity by increasing the moisture carrying capacity of air. This latter mechanism may represent the greatest likely effect on service lives of cartridges. Temperature effects alone have been reported to reduce the service life 1-10% for every 10 degrees Celsius rise depending on the specific solvent (Nelson, et. al., 1976). Corrections to cartridge estimated service life for this effect alone are probably not necessary under normal working temperatures.
Relative Humidity: water vapor will compete with the organic vapors for active sites on the adsorbent
Relative Humidity is a measure of the amount of water vapor the air will hold at a specified temperature and is expressed in percentage values. Since warmer air will hold more water than colder air, the same relative humidity at a higher temperature represents a significantly greater amount of moisture. High relative humidity is a significant negative factor in the capacity of organic vapor cartridges since the large quantity of water vapor will compete with the organic vapors for active sites on the adsorbent. Most of the laboratory work determining adsorbent capacity has been performed at a low relative humidity of 50% at approximately 70 degrees F.
If the actual use of the organic vapor respirators will take place in a significantly more humid environment, then you may need to apply or take into account a safety factor when determining a service life. The exact magnitude of the humidity effect is complex, dependent in part upon chemical characteristics and concentrations of both the contaminant and the water vapor. Based upon relatively few studies, a reduction by a factor of 2 in the cartridge service life originally estimated based upon 50 % relative humidity, may be made when the relative humidity reaches 65% (Nelson, et. al., 1976; Werner, 1985). If the relative humidity exceeds 85%, you should consider experimental testing or another method to more specifically determine the service life. Mathematical modeling may be an appropriate, albeit complex, approach to predict the effect of humidity at various chemical concentrations (Wood, 1987; Underhill, 1987).
Multiple Contaminants: predictions should be derived from the least well adsorbed compound
Multiple contaminants introduce a great deal of variability into the prediction of service life for respirator cartridges. Much of the laboratory testing and the mathematical models have utilized a single contaminant to determine service lives. Only a limited number of multiple contaminant situations have been studied and reported in the literature (e.g. Yoon, 1996; Jonas et. al., 1986). Cartridge service life for mixtures of compounds with significantly different chemical characteristics is probably best determined by experimental methods. Predictions based upon models without experimental data should probably be very conservative and ascribe the service life derived from the least well adsorbed compound to the total mixture concentration in terms of parts per million. The displacement of a less well adsorbed compound by a more highly adsorbed one may alter the actual service life from the estimated one in some cases.
Exposure Assessment
When? What? How Much?
Employers must characterize the nature and magnitude of employee exposures to respiratory hazards before selecting respiratory protection equipment. Paragraph 29 CFR 1910.134(d)(1)(iii) requires the employer to identify and evaluate the respiratory hazard(s) in the workplace. Employers must make a "reasonable estimate" of the employee exposures anticipated to occur as a result of those hazards, including those likely to be encountered in reasonably foreseeable emergency situations, and must also identify the physical state and chemical form of such contaminant(s). The final rule does not specify how the employer is to make reasonable estimates of employee exposures for the purposes of selecting respirators.
When must an employer conduct an exposure assessment?
When you expose your employees to a respiratory hazard and/or require them to wear respirators. Examples of when you should consider assessments may include but are not limited to:
- When OSHA has a substance specific standard (e.g., lead, methylene chloride).
- When employees notice symptoms (e.g., irritation, odor) or complain of respiratory health effects.
- When the workplace contains visible emissions (e.g., fumes, dust, aerosols).
What is the identity and nature of the airborne contaminant?
Specific characteristics of the airborne hazard must be established in order to select an appropriate respirator.
- Is the airborne contaminant a particulate (dust, fumes, mist, aerosol) or a gas/vapor?
- Is the airborne contaminant a chemical and are material safety data sheets available?
- Is the airborne contaminant a biological (bacteria, mold, spores, fungi, virus)?
- Are there any mandatory or recommended occupational exposure levels for the contaminant?
How much employee exposure is there in the workplace?
The final rule permits employers to use many approaches for estimating worker exposures to respiratory hazards.
- Sampling - Personal exposure monitoring is the "gold standard" for determining employee exposures because it is the most reliable approach for assessing how much and what type of respiratory protection is required in a given circumstance.
- Sampling should utilize methods appropriate for contaminants(s).
- Sampling should present the worst case exposures; or
- Sampling should represent enough shifts and operations to determine the range of exposure.
- Objective Information - You may rely on information and data that indicate that use or handling of a product or material cannot, under worst-case conditions, release concentrations of a respiratory hazard above a level that would trigger the need for respirator use or require use of a more protective respirator.
- You can use data on the physical and chemical properties of air contaminants, combined with information on room dimensions, air exchange rates, contaminant release rates, and other pertinent data, including exposure patterns and work practices, to estimate the maximum exposure that could be anticipated in the workplace.
- Data from industry-wide surveys by trade associations for use by their members, as well as from stewardship programs operated by manufacturers for their customers, are often useful in assisting employers, particularly small-business owners, to obtain information on employee exposures in their workplaces.
-
Variation - You should account for potential variation in exposure by using exposure data collected with a strategy that recognizes exposure variability, or by using worst-case assumptions and estimation techniques to evaluate the highest foreseeable employee exposure levels. The use of safety factors may be necessary to account for uneven dispersion of the contaminant in the air and the proximity of the worker to the emission source.
Exposure Assessment
When? What? How Much?
Employers must characterize the nature and magnitude of employee exposures to respiratory hazards before selecting respiratory protection equipment. Paragraph 29 CFR 1910.134(d)(1)(iii) requires the employer to identify and evaluate the respiratory hazard(s) in the workplace. Employers must make a "reasonable estimate" of the employee exposures anticipated to occur as a result of those hazards, including those likely to be encountered in reasonably foreseeable emergency situations, and must also identify the physical state and chemical form of such contaminant(s). The final rule does not specify how the employer is to make reasonable estimates of employee exposures for the purposes of selecting respirators.
When must an employer conduct an exposure assessment?
When you expose your employees to a respiratory hazard and/or require them to wear respirators. Examples of when you should consider assessments may include but are not limited to:
- When OSHA has a substance specific standard (e.g., lead, methylene chloride).
- When employees notice symptoms (e.g., irritation, odor) or complain of respiratory health effects.
- When the workplace contains visible emissions (e.g., fumes, dust, aerosols).
What is the identity and nature of the airborne contaminant?
Specific characteristics of the airborne hazard must be established in order to select an appropriate respirator.
- Is the airborne contaminant a particulate (dust, fumes, mist, aerosol) or a gas/vapor?
- Is the airborne contaminant a chemical and are material safety data sheets available?
- Is the airborne contaminant a biological (bacteria, mold, spores, fungi, virus)?
- Are there any mandatory or recommended occupational exposure levels for the contaminant?
How much employee exposure is there in the workplace?
The final rule permits employers to use many approaches for estimating worker exposures to respiratory hazards.
- Sampling - Personal exposure monitoring is the "gold standard" for determining employee exposures because it is the most reliable approach for assessing how much and what type of respiratory protection is required in a given circumstance.
- Sampling should utilize methods appropriate for contaminants(s).
- Sampling should present the worst case exposures; or
- Sampling should represent enough shifts and operations to determine the range of exposure.
- Objective Information - You may rely on information and data that indicate that use or handling of a product or material cannot, under worst-case conditions, release concentrations of a respiratory hazard above a level that would trigger the need for respirator use or require use of a more protective respirator.
- You can use data on the physical and chemical properties of air contaminants, combined with information on room dimensions, air exchange rates, contaminant release rates, and other pertinent data, including exposure patterns and work practices, to estimate the maximum exposure that could be anticipated in the workplace.
- Data from industry-wide surveys by trade associations for use by their members, as well as from stewardship programs operated by manufacturers for their customers, are often useful in assisting employers, particularly small-business owners, to obtain information on employee exposures in their workplaces.
-
Variation - You should account for potential variation in exposure by using exposure data collected with a strategy that recognizes exposure variability, or by using worst-case assumptions and estimation techniques to evaluate the highest foreseeable employee exposure levels. The use of safety factors may be necessary to account for uneven dispersion of the contaminant in the air and the proximity of the worker to the emission source.
Safety Factors for Cartridge Service Life
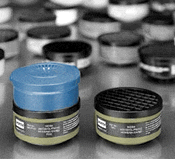
Safety factors are reductions to an estimated service life to ensure that the actual service life will not be exceeded. They are generally applied to the estimate for non-correctable conditions such as presence of unknown contaminants, variations in work rate, or emergency situations. Thus the change schedule will end before the cartridge service life expires. The safety factor reduction depends in part upon the accuracy of estimation methods and in part upon workplace variables.
Safety Factors for Cartridge Service Life
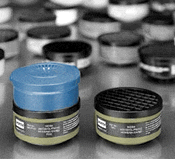
Safety factors are reductions to an estimated service life to ensure that the actual service life will not be exceeded. They are generally applied to the estimate for non-correctable conditions such as presence of unknown contaminants, variations in work rate, or emergency situations. Thus the change schedule will end before the cartridge service life expires. The safety factor reduction depends in part upon the accuracy of estimation methods and in part upon workplace variables.
Rule of Thumb
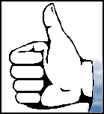
Experimental work can allow for a generalization or "rule of thumb" that broadly defines the service life of cartridges exposed to chemicals. One such Rule of Thumb for estimating organic vapor cartridge service life is found in chapter 36 of the American Industrial Hygiene Association (AIHA) publication "The Occupational Environment - Its Evaluation and Control."
It suggests that:
→ If the chemical's boiling point is > 70 °C and the concentration is less than 200 ppm you can expect a service life of 8 hours at a normal work rate.
→ Service life is inversely proportional to work rate.
→ Reducing concentration by a factor of 10 will increase service life by a factor of 5.
→ Humidity above 85% will reduce service life by 50%.
These generalizations should only be used in concert with one of the other methods of predicting service life for specific contaminants.
Rule of Thumb
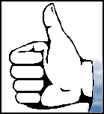
Experimental work can allow for a generalization or "rule of thumb" that broadly defines the service life of cartridges exposed to chemicals. One such Rule of Thumb for estimating organic vapor cartridge service life is found in chapter 36 of the American Industrial Hygiene Association (AIHA) publication "The Occupational Environment - Its Evaluation and Control."
It suggests that:
- If the chemical's boiling point is > 70 °C and the concentration is less than 200 ppm you can expect a service life of 8 hours at a normal work rate.
- Service life is inversely proportional to work rate.
- Reducing concentration by a factor of 10 will increase service life by a factor of 5.
- Humidity above 85% will reduce service life by 50%.
These generalizations should only be used in concert with one of the other methods of predicting service life for specific contaminants.