Lockout/Tagout eTool
Energy Control Program » Specific Procedures for Energy Control and Control Circuitry Prohibition
Employers must develop, document, and implement energy control procedures to control potentially hazardous energy and render equipment or machinery inoperative whenever employees perform activities covered by the Lockout/Tagout standard. The energy control procedure provides the authorized employee with written instructions specifying how to eliminate the potential for the unexpected activation, or start up of machinery or equipment or the release of stored energy.
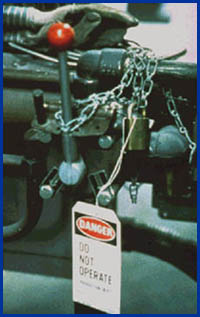
The energy control procedures must outline the scope, purpose, authorization, rules, and techniques that will be used to control hazardous energy, and the means that will be used to enforce compliance.
The energy control procedures must identify the type and magnitude of the hazardous energy and the means and methods that will be used to protect employees during servicing or maintenance operations. The energy control procedure must identify the machine(s) or equipment on which the procedure is to be used. This will ensure that the authorized employee implements the appropriate energy control procedure for the equipment or machine to be serviced or maintained.
Employers are required to address within the energy control procedures the sequential steps necessary to shut down, isolate, block, and secure machines or equipment. Sequential steps for placing, removing, and transferring lockout/tagout devices are also required. If energy control procedures are the same for various pieces of equipment or machines, or if the equipment or machines can be grouped in another logical manner, then a single energy control procedure may be sufficient. An employer may also elect to develop a comprehensive lockout/tagout procedure supplemented by checklists or appendices. However, the energy control procedure must be specific enough and clearly outline the steps to be taken by the authorized employee. There may well be service and /or maintenance operations in a facility which requires their own specific energy control procedure.
Documentation of Procedures
These energy control procedures must be documented. Documentation is necessary in most energy control situations to ensure that authorized employees carefully and specifically follow the steps in the energy control procedure. However, it has been determined that in certain limited situations, documentation of the procedure will not add markedly to the protection otherwise provided by the standard. Section 1910.147(c)(4)(i) explains the eight circumstances under which an employer may be exempted from the requirement for a written energy control procedure.
The documentation exception is intended to apply to situations in which the procedures for deenergization, servicing, and reenergization can be carried out without detailed interactions of energy sources, machines, and employees. When all conditions of the exception are met, the standard does not require the employer to document the energy control procedure unless an accident has occurred involving the unexpected release of hazardous energy. See the Preamble at Federal Register, Vol. 54, No. 169, September 1, 1989, page 36670.
Full Employee Protection
In addition, when an employer uses tagout to control hazardous energy on an energy isolating device that is capable of being locked out, the energy control procedures must provide full employee protection that is equivalent to the level of protection that would be provided through the use of a lockout program.
Full employee protection includes complying with all tagout-related provisions, plus implementing additional safety measures that can provide a level of safety equivalent to that obtained by using a lockout program. Equivalents to reduce the potential for any unexpected or inadvertent energization might include:
- Removing and isolating a circuit element
- Blocking a controlling switch
- Opening an extra disconnecting device
- Removing a valve handle
Procedures for Deenergizing Machines or Equipment
To properly deenergize and eliminate all sources of potential hazardous energy during servicing and maintenance operations and to prevent an employee from omitting an important step in the energy control procedure, the following specific procedural steps must be implemented:
-
Prepare for shutdown. Before an authorized or affected employee turns off a machine or equipment, the authorized employee must have knowledge of the type and magnitude of the energy, the hazards of the energy to be controlled, and the method or means to control the energy.
-
Shut down the machine(s) or equipment. The machine(s) or equipment must be turned off or shut down using normal stopping means, such as using the stop button(s) at the production control center. An orderly shutdown must be conducted to avoid any additional or increased hazards to employees as a result of equipment deenergization. Both authorized and affected employees are permitted to shut down the equipment or machines. However, to ensure that the work will be accomplished safely, only authorized employees are permitted to deenergize and lock or tag out the machines or equipment which are being serviced or maintained. Under the Lockout/Tagout standard, authorized employees who are performing the servicing and/or maintenance, are the only individuals who have been trained to implement the energy isolation procedure and therefore are the only ones permitted to implement it (with the exception of initial preparation for shutdown which allows an affected employee to turn off a machine or equipment, as provided in paragraph (d)(1).
-
Disconnect the energy isolating device(s). All energy isolating devices used to control the energy to the machine or equipment must be physically located and placed in the "off" position to disconnect the machine or equipment from its energy source and deenergize it. Control circuitry does not provide a physical barrier that controls hazardous energy and, therefore, is not an energy isolation device. For example, push buttons, selector switches, and interlocking gates are not energy isolation devices and are not permissible substitutes for energy isolation devices under the standard.
-
Apply the lockout or tagout device(s). Once the equipment or machine's energy isolating device has been disconnected, the lockout or tagout device shall be affixed.
-
Render all stored and/or residual energy safe. Once the lockout or tagout devices have been applied, all potentially hazardous stored or residual energy must be relieved, disconnected, restrained, and rendered safe before the servicing or maintenance can be conducted. If stored energy is present in the machine or equipment after it has been isolated from the energy source(s), the energy must be controlled before servicing and/or maintenance work can be performed. However, if stored energy could reaccumulate while servicing and/or maintenance work is being performed, the employer must continue to verify the isolation of the machine or equipment to assure that it can not reaccumulate and present a hazard to the servicing and/or maintenance employees. The presence of hydraulic or pneumatic systems may necessitate the use of bleed valves to relieve pressure.
-
Verify the isolation and deenergization of the machine or equipment prior to starting work. Employees must verify that machines or equipment have been isolated and deenergized before they begin service or maintenance activities. This step may involve a deliberate attempt to start up the equipment, which should be impossible to activate because of the isolation of the machine or equipment from its energy sources(s). It is an action intended to assure the employee that energy from all power source(s) have been effectively isolated, that residual or stored energy has been blocked, and that injury could not result from inadvertent activation of the operating controls. Verification can also be accomplished using monitoring instruments such as a voltmeter to test electrical circuits to determine that there is no electrical energy available to the machine or equipment. Similar test equipment could be used to check for the presence of other energy types and sources. In order to verify that all potentially hazardous energy has been isolated, the authorized employee may need to use a combination of verification methods. The appropriate combination will depend upon the type of machinery or equipment involved, the complexity of the system, or other factors.
Procedures for Placement, Removal, and Transfer of Lockout/Tagout Devices
The energy control procedures must include specific information concerning the placement, removal, and transfer of the lockout/tagout devices. Employees must be familiar with and able to perform these steps in the appropriate order.
-
Placement of lockout/tagout device(s). The procedure must address whether lockout or tagout devices, or a combination of lockout and tagout devices, will be applied by the authorized employee to the energy isolating device(s) to control hazardous energy. At times, the sequencing and placement of energy isolating and lockout devices can be rather intricate depending upon the complexity of the equipment. For example, an energy control procedure may include affixing a lockout device to an energy isolating device that is capable of being locked out and affixing a tagout device and removing a series of fuses to provide "full employee protection" if the second energy isolating device is capable of being locked out. At a third energy isolating point, a block may be needed to control incoming pressurized energy and the stored pressure may need to be relieved. It is important to ensure that all energy isolation points have been identified, isolated, and the appropriate lockout/tagout device(s) has been applied to provide protection against the potential release of hazardous energy.
- Removal of lockout/tagout device(s). Once the servicing and/or maintenance operations have been completed, specific procedures must be used before the energy isolating devices may be removed and the machine or equipment reenergized. These include:
- Replacement of safeguards, machine or equipment inspection, and removal of all non-essential tools and equipment. This procedure is designed to ensure that employees are not exposed to hazards from normal production if a guard is not replaced, or a tool is left in a location where the startup of the machine would cause the tool to injure the employee or damage the equipment. A visual inspection is acceptable for smaller and less complex machines or equipment. For large, more complex machines or equipment, checklists or other administrative means may be necessary.
- Safe positioning of employees. This procedure is to ensure that employees are not in a location where they are exposed to unexpected energization, start up, or release of hazardous energy when the lock(s) or tag(s) are removed from energy isolating devices. This too can be accomplished by a visual inspection, but for larger, more complex operations, warning devices such as horns, bells or buzzers may be necessary.
- Removal of lockout/tagout device(s). This is to be performed only after the first two steps have been accomplished. Removal of the lockout or tagout device(s) may only be performed by the authorized employee who placed the lock on the energy isolating device, unless the authorized employee who placed the device is unavailable to remove it or in an emergency situation. Under those limited circumstances, the employer may direct the removal of a lockout or tagout device(s), provided that the energy control program incorporates specific procedures and training for that purpose, including:
- — Verifying that the authorized employee is not at the facility.
- — Making all reasonable efforts to contact the employee to inform him/her that his/her device will be removed.
- — Ensuring that the authorized employee knows that the device has been removed prior to resuming work at the facility.
-
Notification of affected employees that servicing and maintenance is completed. The notification procedure is intended to inform the affected employees that the servicing and maintenance operation has been completed and it is now safe to operate the equipment or machine.
-
Transfer of lockout/tagout devices during shift or personnel changes. Many servicing and maintenance operations may extend across one or more workshifts. In such cases it is crucial that energy control procedures and work authorization permits, if used, ensure that all hazardous energy is continuously maintained in a safe, deenergized condition.
Therefore, specific procedures must be used to ensure continuation of lockout or tagout protection for employees during shift or personnel changes. These specific procedures for shift or personnel changes must also address the transfer of lockout/tagout devices between outgoing and incoming employees in order to provide for an orderly transfer of control measures, and to be certain that the machine or equipment is continuously maintained in a safe condition.
One of the most critical elements of ensuring the continuity of protection during shift or personnel changes is providing the incoming employee with an opportunity to verify that the equipment has been deenergized. The incoming employee should not have to depend on the actions of another employee or supervisor, particularly the one who has left the workplace for the day, for assurance that it is safe to work on the machinery or equipment.
OSHA recognizes that the removal and replacement of the lockout/tagout devices for each shift can be involved if a servicing or maintenance operation is complex and entails large numbers of energy isolation devices, large numbers of servicing employees, and multiple shifts. In these situations, an acceptable approach to compliance would be to use a work permit system, with each authorized employee signing on and off the equipment, combined with each authorized employee walking down the equipment to ensure continued deenergization before beginning work.
Specific Procedures for Testing or Positioning of Machines or Equipment
Temporary removal of locks or tags and reenergization of the machinery or equipment is permitted to allow testing or repositioning, provided that specific procedures control the sequence of actions to be taken. The procedures must provide maximum safety coverage for employees when the equipment or machinery must be energized during the course of servicing. Employee exposure to hazards is high during these transition periods. To ensure workplace safety, the following sequence must be followed when testing or repositioning a machine or piece of equipment:
- Clear the machines or equipment of tools and materials.
- Remove employees from the machine or equipment area.
- Remove the lockout or tagout devices as specified.
- Energize and proceed with testing or positioning.
- Deenergize all systems, isolate the machine or equipment from the energy source, and reapply lockout or tagout devices as specified.
OSHA permits the removal of lockout/tagout devices and the reenergization of equipment only during the time necessary for the testing or positioning of the machine, equipment, or component, and only when reenergization is essential to accomplishing the servicing task.