Lead: Secondary Lead Smelter eTool
Smelting » Reverberatory Furnace
Reverberatory furnaces are designed and operated to produce a soft, nearly pure lead product. Reverberatory furnaces emit high levels of lead fume during the following processes:
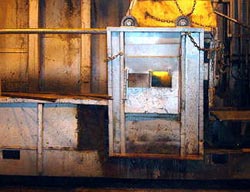
Potential Sources of Exposure
-
Spillage or emissions may occur at feed conveyor transfer and charging points of the reverberatory furnace.
-
Emissions may occur through leaks in refractory material, which allow lead dust and fumes to escape.
-
Lead fume and dust may be emitted from the reverberatory furnace if the furnace is run at positive pressure or if bridging occurs during charging wet materials.
Possible Engineering and Work Practice Controls
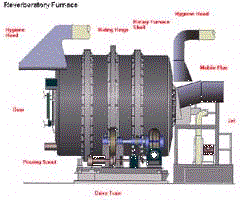
-
Enclose and provide exhaust ventilation for the reverberatory furnace.
- Provide hooding with sufficient exhaust ventilation to capture dust that may be generated by filling or emptying charge material conveyors.
- Maintain positive-pressure, HEPA filtered air system on mobile equipment to ensure effective operation. Check and change air filters regularly as part of an effective scheduled preventative maintenance program.
-
Maintain raw material storage and handling areas under negative pressure to prevent contamination of adjacent furnace areas.
-
Provide process controls to maintain sufficient negative air pressure on the furnace during charging to prevent puffing.
-
Do not overfill conveyors and ram feeders.
-
Vacuum any spills immediately with a HEPA filtered vacuum system. Water should not be used for dust suppression in the smelting area due to the possibility of oxide fires and the mixing of water and molten lead.
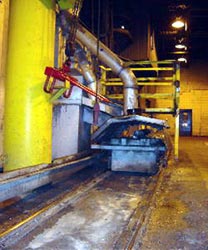
Reverberatory furnace tapping operations involve pouring the molten lead and slag from the furnace into molds or ladles. Some smelters tap metal directly into a holding kettle, which keeps the metal molten for refining. Other smelters cast the furnace metal into blocks and allow the blocks to solidify.
Potential Sources of Exposure
-
Lead fumes may be emitted at the lead or slag tapping plugs during removal of the tapping plug or while lancing the tapping plug.
-
Pouring lead or slag into the tapping launder, mold, ladle or refining kettle may emit fumes.
-
Lead dust may become airborne due to the disturbance of settled dust in the smelting area.
-
Ladles containing slag or molten lead may emit fumes.
-
Spilled slag or molten lead may emit lead fumes.
Possible Engineering and Work Practice Controls

-
Provide local exhaust ventilation at the lead and slag tap, launders, molds, ladles, and refining kettles.
- Allow lead and slag pots to remain under the exhaust hood until crusted to minimize the emission of fume.
- Provide supplied air island at lead and slag tapping stations.
- Provide local exhaust ventilation for staged slag pots if necessary.
-
Reline or repair refractory as necessary to minimize lead fume leakage from furnace.