Ammonia Refrigeration eTool
Storage of Ammonia in Vessels » Operation of Ammonia High Pressure Receiver HPR-1
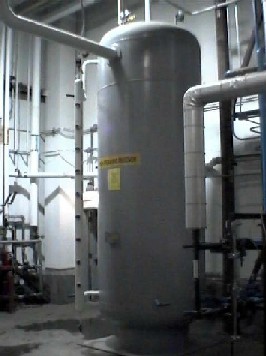
Operation of Ammonia High Pressure Receiver HPR-1
Company Name |
Section Number: TBD |
Page 1 |
---|---|---|
Process Safety Management |
PSM/Standard Operating Procedures/Review/Revision/HPR-1 |
|
Prepared by: |
Revision Date: 0/00 |
|
Revision Approved by: Plant Engineer |
Issue Revision |
Objective: |
This procedure is designed to describe the Technical Operating Specifications (TOS), and to set down the Standard Operating Procedures for the safe operation of Ammonia High Pressure Receiver 1 (HPR-1). |
---|---|
Purpose: |
The purpose of the TOS is to provide a description of the High Pressure Receiver, to define the function of the receiver, its operating conditions and limits, and consequences of deviation from these limits; To describe controls and instrumentation and safety systems, and set operating alignments. The purpose of the Standard Operating Procedure (SOP) is to set down the proper steps for starting, monitoring normal operation, and stopping and restarting the Receiver under normal and emergency conditions. |
Concerns: |
Very Careful attention to valve positions, temperature, and pressure levels is extremely important to the successful completion of these procedures. Deviations from normal operating limits could cause personal injury or death, small to catastrophic release of ammonia or environmental damage, or evacuation of, or injury to, members of the public. We seek to prevent incidents such as:
The company Lockout/Tagout program shall be followed when taking the receiver out of service, while maintaining the receiver, and whil returning it to service. If Line-Breaking is required, all Line-Breaking precautions described in the company Line-Break Policy shall be observed. Additionally, proper PPE shall be immediately available, or worn in response to the threat level posed by the work and circumstances. |
Department: |
Refrigeration |
Operator: |
Qualified Refrigeration Operator(s) |
Equipment: |
Ammonia High Pressure Receiver, HPR-1 outside the south compressor room. Data from U-1-A: Vertical Receiver, Serial Number xxxxx, National Board Number xxxxx, built in 1998, by E.L. Nickell Company. MAWP: 250 psig @ 240°F |
Location: |
|
Related Documents: |
|
Initial Date of Development: |
4/1998 |
Authorized By: |
|
Previous Revision: |
4/1/1998 |
Annual Review By, and Date: |
9/2001 plant engineer, utilities supervisor, two operators, the Process Safety Management (PSM) coordinator, and an outside consultant |
Technical Operating Specifications (TOS)
Function: |
The function of the High Pressure Receiver (HPR-1) is to provide storage for part of the Anhydrous Ammonia liquid inventory needed to supply the plant refrigeration loads, and recirculation receiver loads, as required to maintain efficient operation. |
---|
Description: |
Capacity/ Size |
Safe Operating Limits |
Consequences of Deviation |
Corrective Action |
---|---|---|---|---|
Vertical thermo-siphon Receiver |
7’10.5” x 19’11.75” inside |
250 psig MAWP, max capy 80 percent fill |
Over-pressurization will cause operation of pressure relief valves. Probable risk of ammonia inhalation by nearby Community residents and businesses. |
Shutdown the transfer pumps. Send all the liquid produced to Refrigeration. |
Overfilling will cause refrigerant backup into condensers. |
Shutdown the transfer pumps. Send all the liquid produced to Refrigeration. |
|||
Control failure may result in overfilling |
Shutdown the transfer pumps. Send all the liquid produced to Refrigeration. |
Controls and Instrumentation Safety Systems
DESCRIPTION |
ITEM NUMBER |
FUNCTION |
POSITION AND/OR NORMAL SETPOINT |
---|---|---|---|
High Level float |
Measures level of ammonia liquid in tank, activate warning when reached |
Less than 80 percent fill level; activates alarm light if reached. Light is in the main compressor room |
|
Low level float |
Measures level of ammonia liquid in receiver, activate warning light |
At approximately 10 percent liquid level, activates warning light in the main compressor room. |
|
Dual Pressure Relief Valves on manifold |
Protect against over-pressurization above MAWP of 250 psig |
Top of the receiver, on dual PRV manifold, see P&ID Sheet xx |
Standard Operating Procedure (SOP) Task Flow Diagram
1. Normal start up |
↓ |
2. Normal shutdown |
↓ |
3. Shutdown and isolation for maintenance/repair activity |
↓ |
4. Emergency shutdown and isolation |
↓ |
5. Startup following emergency shutdown and isolation, or shutdown and isolation for maintenance activities |
↓ |
Task |
Step |
Comment |
---|---|---|
1. Normal Start up |
1. |
The receiver is not shut down under normal operations. Restart under normal conditions is never necessary. |
Task |
Step |
Comment |
2. Normal Shut Down |
1. |
The receiver would not be shut down during operation, for any reason. This is essential to the safe operation of the entire system. |
3. Shutdown and Isolation for Maintenance or Repair |
1. See Maintenance Procedures for the float columns, floats, and alarm systems |
Isolation of the receiver itself is not probable. Float columns and alarms can be individually isolated for maintenance and repair. See adjunct SOP |
4. Emergency Shutdown and Isolation |
4.1. Close HPL supply hand valve from condensers: |
Valve number xxxx (hand valve) |
4.2. Close EQ line hand valve |
Valve number xxxx (hand valve) |
|
4.3. Close Purge line hand valve |
Valve number xxxx (hand valve) |
|
4.4. Close HPL return from transfer tanks 1 AND 2 |
Valve number xxxx (hand valve) |
|
4.5. Close liquid injection cooling supply line valve |
Valve number xxxx |
|
4.6. Close liquid feed to plant hand valves |
Valve number xxxx and Valve number xxxx |
|
4.7. Shut down liquid transfer pumps 1 and 2 at TT1 and TT2 in main compressor room |
Transfer Tank 1, Transfer Tank 2, per relevant SOP for both |
|
4.8. Assess situation |
If shutdown is for any period of time, refrigeration operations will shut down as liquid supply runs out. |
|
4.9 Follow instructions of Emergency Response Personnel on scene. |
If this situation involves fire or engulfment, evacuate immediate area of receiver and observe from a safe distance. |
|
If situation involves damage to any part of the refrigeration system, prepare to mitigate and/or contain escaping liquid and vapor, using appropriate PPE, if trained to do so. |
||
5. Startup following emergency shutdown and isolation. |
5.1. Assess situation. Consult with Emergency Response Personnel and Complex Management before initiating start up after emergency and/or release. |
Determine exact extent of any damage, ascertain that electrical power is available; ascertain that compressor room power is available, and that compressor room and ancillary areas are habitable under guidelines for ammonia concentration. |
5.2. Open EQ line hand valve |
Valve number xxxx (hand valve) This equalizes condensers and receiver to same pressure. |
|
5.3. Open purge line hand valve |
Valve number xxxx (hand valve). This will align purger and receive for normal operation. |
|
5.4. Open liquid feed to plant hand valves |
Valve numbers xxxx, and xxxx (hand valves). Visually inspect for ammonia leaks. This will supply the plant loads and recirculators with liquid refrigerant. |
|
5.5. Open the liquid injection supply hand valves |
Valve number xxxx (hand valve). This will permit liquid ammonia flow to cool compressor oil injection. |
|
5.6. Open liquid return from TT 1, and TT 2, hand valves |
Valve number xxxx (hand valve). This will permit transfer of liquid ammonia from the transfer tanks to the receiver. |
|
5.7. Open liquid return hand valve from the condensers |
Valve number xxxx (hand valve). This will permit flow from condensers to receiver. Condensers may now be started and checked for proper operation. |
|
5.8. Turn power on to transfer pumps for TT1, and TT2 |
Refer to SOP for both Transfer Tanks |
|
5.9. Begin normal startup of the ammonia refrigeration system |
Refer to relevant SOP documents for compressors, accumulators, and recirculators. Re-start these prior to proceeding with full system restart. |
Special Cautions and Procedures
Tremendous risk is involved in the complete shutdown and isolation of the High Pressure Receiver unless it is for an extreme emergency involving risk of injur or death to personnel, and/or community residents. Assess the risks and benefits carefully, in consultation with complex management and emergency services personnel. For maintenance, repair or inspection procedures requiring opening of this, or any component of the Ammonia Refrigeration System to the atmosphere, the company line-breaking policy and procedures shall be strictly followed. Among the procedures and steps that are required are:
The area of the line break shall be observed periodically to ensure leakage-free operation, and proper refrigeration function. See also S-xx, Section xx, bid specification for acceptable parts and procedures for repair and replacement of component parts. |