Tri-State Building Services Works With NYDOL For a Safer Workplace
Company: Tri-State Window Cleaning, Inc., dba Tri-State Building Services, LLC
Location: , New York
Employees: 60 - 70
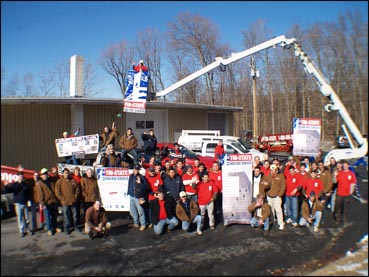
Industry: NAICS - 561720 Janitorial and Cleaning Services
Success Brief:
Tri-State Building Services, LLC (Tri-State) provides full service exterior cleaning and property maintenance programs to residential and commercial industries. Tri-State improved their safety and health management programs through working with the New York State Department of Labor's (NYDOL) On-site Consultation Program. The company received their initial visit from the NYDOL On-site Consultation Program in January 2010.
Dave Grady, Vice President of Tri-State said, "Since the On-site Consultation visit, Tri-State has incurred no lost-time injuries and employee morale has increased." On June 4, 2010, the NYDOL presented Tri-State with a Certificate of Appreciation. NYDOL recognized the site its commitment to promote workplace safety and health by its requesting an On-site Consultation visit.
Company Description:
Tri-State provides exterior building cleaning services (NAICS 561720, Janitorial and Cleaning Services) which include caulking, power washing, painting, window cleaning, and property maintenance programs to low- and high-rise buildings. Tri-State's main office is located in Poughkeepsie, New York. It has several satellite offices throughout the New York and also provides services in Connecticut and Massachusetts.
The Situation:
The owners of Tri-State, bothers Jim Grady, President, and Dave Grady, Vice President, have always made safety a priority due to the nature of the company's industry. Through their need to continue to keep Tri-State employees safe, they decided to seek safety and health assistance from outside experts.
As part of its efforts to increase their understanding of safety and health, Tri-State joined its industry trade association, the Sealant Waterproofing and Restoration (SWR) Institute. At the time it joined the organization, the company's management didn't realize SWR Institute was an OSHA Alliance Program participant. SWR Institute has been an Alliance Program participant since 2003. Through this cooperative program, OSHA and SWR Institute work together to promote safe and secure workplaces in the sealant, waterproofing and restoration industry as well as to enhance worker voice in the workplace. Raising awareness of OSHA's On-site Consultation Program in the industry is one of the goals of the Alliance. OSHA's On-Site Consultation is a federally funded program, which offers free and confidential services to small and medium-sized businesses, and is available to employers in all U.S. states and several territories. For more information see OSHA's Alliance Program.
After joining the SWR Institute's Safety Committee which is actively involved in the implementation of the OSHA and SWR Institute Alliance, Tri-State learned about OSHA's On-site Consultation Program. Members of the SWR Institute Board of Directors who had used the On-site Consultation Program services at their companies recommended Tri-State contact the local On-site Consultation Project for a free safety and health evaluation.
The Solution:
Dave Grady was hesitant initially to seek assistance from the On-site Consultation service. He said, "Inviting OSHA to the workplace was a strange idea at first. However, once we thought it through and gained a better understanding of the program and how it works it seemed like a no-brainer. Why not take advantage of the nation's top authority on safety." In New York State, OSHA's On-site Consultation Program is run by the NYDOL. Tri-State contacted the NYDOL On-site Consultation Program in December 2009.
In January 2010, a consultant from the NYDOL On-site Consultation Program conducted an initial consultation visit of Tri-State's main facility in Poughkeepsie, New York, a satellite office in Albany, New York and one local jobsite. The consultant began the visit with an explanation of the Program's services and informed the employer of its rights and responsibilities. The consultant, along with Tri-State owners and workers, conducted a walkthrough of the establishments and addressed work areas that needed improvement.
In response to the visit, Tri-State corrected identified hazards and instituted several improvements to the company's safety and health management programs. Improvements that Tri-State made include purchasing and installing eye wash stations, properly labeling equipment and chemicals, and enhancing the company's safety manuals. In addition, as a result of the visit, several safety documents also were translated in Spanish to assist Spanish speaking employees with understanding safety and health information.
Dave Grady stated, "Tri-State has taken the position that an educated employee is a safe employee, and the safety and health management contribution involves the participation of management and employees in an internal training program." For example, the company holds weekly tool box talks addressing a wide range of subjects. "Since fall hazards are one of the company's greatest threats," said Dave Grady, "Tri-State addresses fall protection in a separate weekly meeting with staff." Other course work featured in Tri-State's safety program consists of: OSHA 10-hour Outreach Training Program for Construction course, OSHA 30-hour Outreach Training Program for Construction course, Suspended Scaffold, Aerial Lift, International Window Cleaning Association training program, and Aerial Lift Train the Trainer Program for all managers.
The Impact:
After working with the consultant, Tri-State felt it obtained a greater level of awareness and understanding of the significance of an effective safety and health management program. According to Dave Grady, "To maintain a safety and health environment, Tri-State has learned to train, re-train, and reinforce. The company examines their safety and health management program constantly by re-evaluating and modifying their overall existing program, searching for improvement."
Tri-State's has maintained a rate of "0" for both Days Away, Restricted or Transferred (DART) rate and Total Recordable Case (TRC) rate from 2008 through 2010. By comparison, the 2010 national industry average DART and TRC were 2.3 and 3.4 respectively for their industry. Between 2008 and 2010, Tri-State's Experience Modifier Rate decreased by .07, saving the company over $5,000 in workers' compensation premiums.
"I have had numerous employees over the years tell me that we are the safest company that they have ever worked for," stated Mr. Grady. "The On-site Consultation visits have helped the organization to enforce its safety and health expectations by encouraging Tri-State's employees to be safety conscious throughout the entire organization."
Source:
Jim Grady, President, Tri-State Window Cleaning, Inc., dba Tri-State Building Services, LLC
Dave Grady, Vice President, Tri-State Window Cleaning, Inc., dba. Tri-State Building Services, LLC