McElroy Manufacturing, Inc. Oklahoma Family-Owned Pipe Fusion Company – Lean to Safety
Company: McElroy Manufacturing, Inc. – 5305 East Admiral
Location: Tulsa, Oklahoma
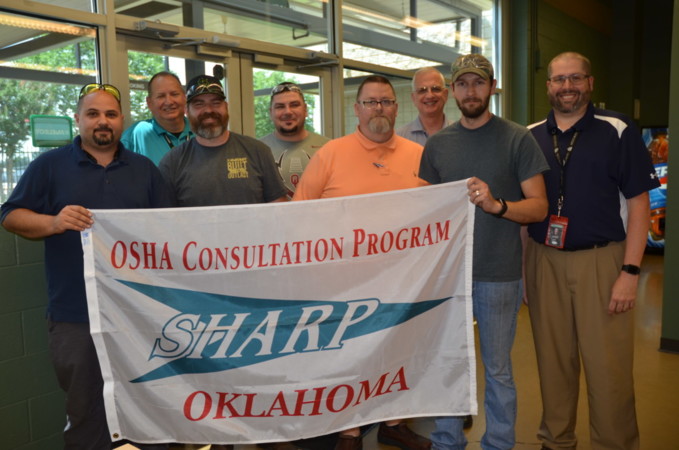
NAICS Code: 332999
McElroy Manufacturing, Inc., located in Tulsa, is a second-generation, Oklahoma family-owned company, founded in 1954 by Art and Panny McElroy and now run by the McElroy family. The McElroy's believe in an honest work ethic. They hold teamwork, innovation, accountability, integrity, mutual trust and respect, and a desire to continuously improve safety and quality above all else. McElroy is entirely dedicated and eagerly expanding their polyethylene pipe fusion machines in new markets across the globe.
The Situation
McElroy employees work in a high-hazard industry. Along with weld, grind, and paint shops, they use over 70 machine tools to manufacture pipe fusion equipment. In assembly and the warehouse, they move machinery on a daily basis. Each employee has a specific task to complete each day, involving building and moving machines or heavy equipment. Employees typically assemble fusion machines, lift large parts, assemble machines, or paint equipment. At McElroy, management has focused on quality operations and safe business practices in a manner that offers protection to every employee.
"Our motto here at McElroy is we are not going to ask employees to do something that will harm them or harm others; we want empowered employees to speak up and take ownership of their work areas," said Tony Little, Health and Safety Manager.
McElroy's commitment to safety goes back over 50 years. At the request of the founder, Art McElroy, the first Oklahoma Department of Labor visit was conducted in 1964, before federal Department of Labor, Occupational Safety and Health Administration (OSHA) was established. 1 In 1999, Mr. McElroy contacted Oklahoma OSHA Consultation Services. This unit of the Oklahoma Department of Labor helps businesses meet the Federal OSHA health and safety regulations.
Today's OSHA On-Site Consultation Program offers voluntary, no cost, and confidential occupational safety and health services to small and medium-sized businesses in all 50 states, the District of Columbia, and several U.S. territories, with priority given to high-hazard worksites. On-Site Consultation services are separate from enforcement and do not result in penalties or citations. Consultants from state agencies, such as the Oklahoma OSHA Consultation Services, or universities work with employers to identify workplace hazards, provide advice for compliance with OSHA standards, and assist in establishing and improving safety and health programs.
Since that first Oklahoma OSHA Consultation Services visit in 1999, McElroy has been working to correct hazards noted during the consultant's walk-around, program review, and employee policy involvement. During one of the initial inspections, over 40 serious hazards were found.
The Solution
The company corrected all of the hazards and continued to work with the Oklahoma consultants to improve its workplace safety processes and polices. With management commitment and more employee involvement, McElroy employees have become more involved in their own workplace safety. People from all levels of the organization contribute to developing a comprehensive safety program that includes employee training, open communication, and individual accountability.
A key part to their success is the accident and near miss reporting mechanisms, job hazard analyses, refresher training, and a company Lean to Safety policy. These efforts contribute to a positive safety culture with employee ownership and involvement. With the most recent addition of the Lean to Safety culture, employees are given time each day to identify things in their work area to improve. Every morning, employees meet to discuss production, safety, and quality issues. Employees make YouTube videos to show how they improved or made a process safer. Employees are also asked what they are grateful for each morning to share with the group. Employee share stories of thankfulness, such as someone helping them get to work because their car broke down, a fellow employee sharing their meal, or an employee who went out of their way to help.
The Impact
McElroy has been dedicated to the safety of their employees from the start. In 2018, with the help of the Oklahoma OSHA Consultation Services, all three of McElroy's Tulsa production facilities were accepted into the OSHA Program (SHARP). This program recognizes small business employers who have used OSHA On-Site Consultation Program services and operate an exemplary safety and health program. Acceptance of a worksite into SHARP from OSHA is an achievement of status that singles the company out among its business peers as a model for worksite safety and health.
McElroy's management has instilled the use of safe work practices with unwavering commitment to ensure employees go home safe each day. Management has worked with the OSHA consultants in reviewing their safety and employee training programs to reinforce their safety commitment to employees. The Management group that focuses on safety includes not only the Health and Safety Managers but also the Vice President of Operations, Manufacturing Engineer Manager, Plants Managers, and Front-Line Supervisors.
Since 1964, workplace safety and health efforts have prevented numerous injuries and saved several thousand dollars. McElroy's workmen's compensation insurance rate is the lowest in Oklahoma; their carrier insures over 500 companies in the state. Over the last several years, the incident rate has remained below the national average. This is a great accomplishment for any business.
Along with strong management commitment and in response to recommendations provided by the OSHA consultants, management formed a stronger bond with and between employees, increased awareness inspections, maintained safety programs, and prevented numerous incidents. "The culture of safety is integrated into everything we do. The biggest impact is our employees feeling like, not only this is a safe place to work, but they don't have to worry about their well-being because we put such an emphasis on it they hold each other accountable," said Barry Calogero, Vice President of Operations. "So if an employee sees something they don't like, they have an obligation and responsibility to say they saw something that didn't seem safe, and they can get it fixed right away instead of saying that it's management's responsibility. They are taking ownership." explained Calogero.
1 The Occupational Safety and Health Administration is an agency of the United States Department of Labor. Congress established the agency under the Occupational Safety and Health Act, which President Richard M. Nixon signed into law on December 29, 1970.
Source: Tony Little, Health and Safety Manager, McElroy Manufacturing, Inc. Barry Calogero, Vice President of Operations, McElroy Manufacturing, Inc.