- Part Number:1910
- Part Number Title:Occupational Safety and Health Standards
- Subpart:1910 Subpart O
- Subpart Title:Machinery and Machine Guarding
- Standard Number:
- Title:Mechanical power presses.
- Appendix:
- GPO Source:
The operating levers on hand-tripped presses having more than one operating station shall be interlocked to prevent the tripping of the press except by the "concurrent" use of all levers.
A means of selecting Off, "Inch," Single Stroke, and Continuous (when the continuous function is furnished) shall be supplied with the clutch/brake control to select type of operation of the press. Fixing of selection shall be by means capable of supervision by the employer.
The "Inch" operating means shall be designed to prevent exposure of the workers hands within the point of operation by:
Pressure vessels. All pressure vessels used in conjunction with power presses shall conform to the American Society of Mechanical Engineers Code for Pressure Vessels, 1968 Edition, which is incorporated by reference as specified in § 1910.6
It shall be the responsibility of the employer to provide and insure the usage of "point of operation guards" or properly applied and adjusted point of operation devices on every operation performed on a mechanical power press. See Table O-10.
Ds = 63 inches/second × Ts
where:
Ds = minimum safety distance (inches); 63 inches/second = hand speed constant;
and
Ts = stopping time of the press measured at approximately 90° position of crankshaft rotation (seconds).
Guards shall be used to protect all areas of entry to the point of operation not protected by the presence sensing device.
Ds = 63 inches/second × Ts;
where:
Ds = minimum safety distance (inches); 63 inches/second = hand speed constant;
and
Ts = stopping time of the press measured at approximately 90° position of crankshaft rotation (seconds).
The safety distance (Dm) between the two hand trip and the point of operation shall be greater than the distance determined by the following formula:
Dm = 63 inches/second × Tm;
where:
Dm = minimum safety distance (inches); 63 inches/second = hand speed constant;
and
Tm = the maximum time the press takes for the die closure after it has been tripped (seconds). For full revolution clutch presses with only one engaging point Tm is equal to the time necessary for one and one-half revolutions of the crankshaft. For full revolution clutch presses with more than one engaging point, Tm shall be calculated as follows:
Tm = [ ½ + (1 ÷ Number of engaging points per revolution)] × time necessary to complete one revolution of the crankshaft (seconds).
Hand feeding tools. Hand feeding tools are intended for placing and removing materials in and from the press. Hand feeding tools are not a point of operation guard or protection device and shall not be used in lieu of the "guards" or devices required in this section.
Scrap handling. The employer shall provide means for handling scrap from roll feed or random length stock operations. Scrap cutters used in conjunction with scrap handling systems shall be safeguarded in accordance with paragraph (c) of this section and with § 1910.219.
Under the general component of the inspection program, the employer shall:
(A) Conduct periodic and regular inspections of each power press to ensure that all of its parts, auxiliary equipment, and safeguards, including the clutch/brake mechanism, antirepeat feature, and single-stroke mechanism, are in a safe operating condition and adjustment;
(B) Perform and complete necessary maintenance or repair, or both, before operating the press; and
(C) Maintain a certification record of each inspection, and each maintenance and repair task performed, under the general component of the inspection program that includes the date of the inspection, maintenance, or repair work, the signature of the person who performed the inspection, maintenance, or repair work, and the serial number, or other identifier, of the power press inspected, maintained, and repaired.
Under the directed component of the inspection program, the employer shall:
(A) Inspect and test each press on a regular basis at least once a week to determine the condition of the clutch/brake mechanism, antirepeat feature, and single-stroke mechanism;
(B) Perform and complete necessary maintenance or repair, or both, on the clutch/brake mechanism, antirepeat feature, and single-stroke mechanism before operating the press; and
(C) Maintain a certification record of each maintenance task performed under the directed component of the inspection program that includes the date of the maintenance task, the signature of the person who performed the maintenance task, and the serial number, or other identifier, of the power press maintained.
Note to paragraph (e)(1)(ii): Inspections of the clutch/brake mechanism, antirepeat feature, and single-stroke mechanism conducted under the directed component of the inspection program are exempt from the requirement to maintain certification records specified by paragraph (e)(1)(i)(C) of this section, but inspections of the clutch/brake mechanism, antirepeat feature, and single-stroke mechanism conducted under the general component of the inspection program are not exempt from this requirement.
Overloading. The employer shall operate his presses within the tonnage and attachment weight ratings specified by the manufacturer.
Explanation of above diagram:
This diagram shows the accepted safe openings between the bottom edge of a guard and feed table at various distances from the danger line (point of operation).
The clearance line marks the distance required to prevent contact between guard and moving parts.
The minimum guarding line is the distance between the infeed side of the guard and the danger line which is one-half inch from the danger line.
The various openings are such that for average size hands an operator's fingers won't reach the point of operation.
After installation of point of operation guards and before a job is released for operation a check should be made to verify that the guard will prevent the operator's hands from reaching the point of operation.
Distance of opening from point of operation hazard | Maximum width of opening |
---|---|
½ to 1½ | ¼ |
1½ to 2½ | ⅜ |
2½ to 3½ | ½ |
3½ to 5½ | ⅝ |
5½ to 6½ | ¾ |
6½ to 7½ | ⅞ |
7½ to 12½ | 1¼ |
12½ to 15½ | 1½ |
15 ½ to 17½ | 1⅞ |
17½ to 31½ | 2⅛ |
This table shows the distances that guards shall be positioned from the danger line in accordance with the required openings.
The employer shall report, within 30 days of the occurrence, all point-of-operation injuries to operators or other employees to either the Director of the Directorate of Standards and Guidance at OSHA, U.S. Department of Labor, Washington, DC 20210 or electronically at http://www.osha.gov/pls/oshaweb/mechanical.html; or to the State Agency administering a plan approved by the Assistant Secretary of Labor for Occupational Safety and Health.
Air valve and air pressure supply/control.
(A) The requirements of paragraphs (b)(7)(xiii), (b)(7)(xiv), (b)(10), (b)(12) and (c)(5)(iii) of this section apply to the pneumatic systems of machines used in the PSDI mode.
(B) The air supply for pneumatic clutch/brake control valves shall incorporate a filter, an air regulator, and, when necessary for proper operation, a lubricator.
(C) The air pressure supply for clutch/brake valves on machines used in the PSDI mode shall be regulated to pressures less than or equal to the air pressure used when making the stop time measurements required by paragraph (h)(2)(ii) of this section.
Air counterbalance systems.
(A) Where presses that have slide counterbalance systems are used in the PSDI mode, the counterbalance system shall also meet the requirements of paragraph (b)(9) of this section.
(B) Counterbalances shall be adjusted in accordance with the press manufacturer's recommendations to assure correct counterbalancing of the slide attachment (upper die) weight for all operations performed on presses used in the PSDI mode. The adjustments shall be made before performing the stopping time measurements required by paragraphs (h)(2)(ii), (h)(5)(iii), and (h)(9)(v) of this section.
The control system shall perform checks for proper operation of all cycle control logic element switches and contacts at least once each cycle. Control elements shall be checked for correct status after power "on" and before the initial PSDI stroke.
The control system shall have provisions for an "inch" operating means meeting the requirements of paragraph (b)(7)(iv) of this section. Die-setting shall not be done in the PSDI mode. Production shall not be done in the "inch" mode.
(A) PSDI shall be implemented only by use of light curtain (photo-electric) presence sensing devices which meet the requirements of paragraph (c)(3)(iii)(c) of this section unless the requirements of the following paragraph have been met.
(B) Alternatives to photo-electric light curtains may be used for PSDI when the employer can demonstrate, through tests and analysis by the employer or the manufacturer, that the alternative is as safe as the photo-electric light curtain, that the alternative meets the conditions of this section, has the same long term reliability as light curtains and can be integrated into the entire safety system as provided for in this section. Prior to use, both the employer and manufacturer must certify that these requirements and all the other applicable requirements of this section are met and these certifications must be validated by an OSHA-recognized third-party validation organization to meet these additional requirements and all the other applicable requirements of paragraphs (a) through (h) and appendix A of this section. Three months prior to the operation of any alternative system, the employer must notify the OSHA Directorate of Safety Standards Programs of the name of the system to be installed, the manufacturer and the OSHA-recognized third-party validation organization immediately. Upon request, the employer must make available to that office all tests and analyses for OSHA review.
The safety distance (Ds) from the sensing field of the presence sensing device to the point of operation shall be greater than or equal to the distance determined by the formula:
Ds = Hs × (Ts + Tp + Tr + 2Tm) + Dp
Where:
Ds = Minimum safety distance.
Hs = Hand speed constant of 63 inches per second (1.6 m/s).
Ts = Longest press stopping time, in seconds, computed by taking averages of multiple measurements at each of three positions (45 degrees, 60 degrees, and 90 degrees) of crankshaft angular position; the longest of the three averages is the stopping time to use. (Ts is defined as the sum of the kinetic energy dissipation time plus the pneumatic/magnetic/hydraulic reaction time of the clutch/brake operating mechanism(s).)
Tp = Longest presence sensing device response time, in seconds.
Tr = Longest response time, in seconds, of all interposing control elements between the presence sensing device and the clutch/brake operating mechanism(s).
Tm = Increase in the press stopping time at the top of the stroke, in seconds, allowed by the brake monitor for brake wear. The time increase allowed shall be limited to no more than 10 percent of the longest press stopping time measured at the top of the stroke, or 10 milliseconds, whichever is longer.
Dp = Penetration depth factor, required to provide for possible penetration through the presence sensing field by fingers or hand before detection occurs. The penetration depth factor shall be determined from Graph h-1 using the minimum object sensitivity size.
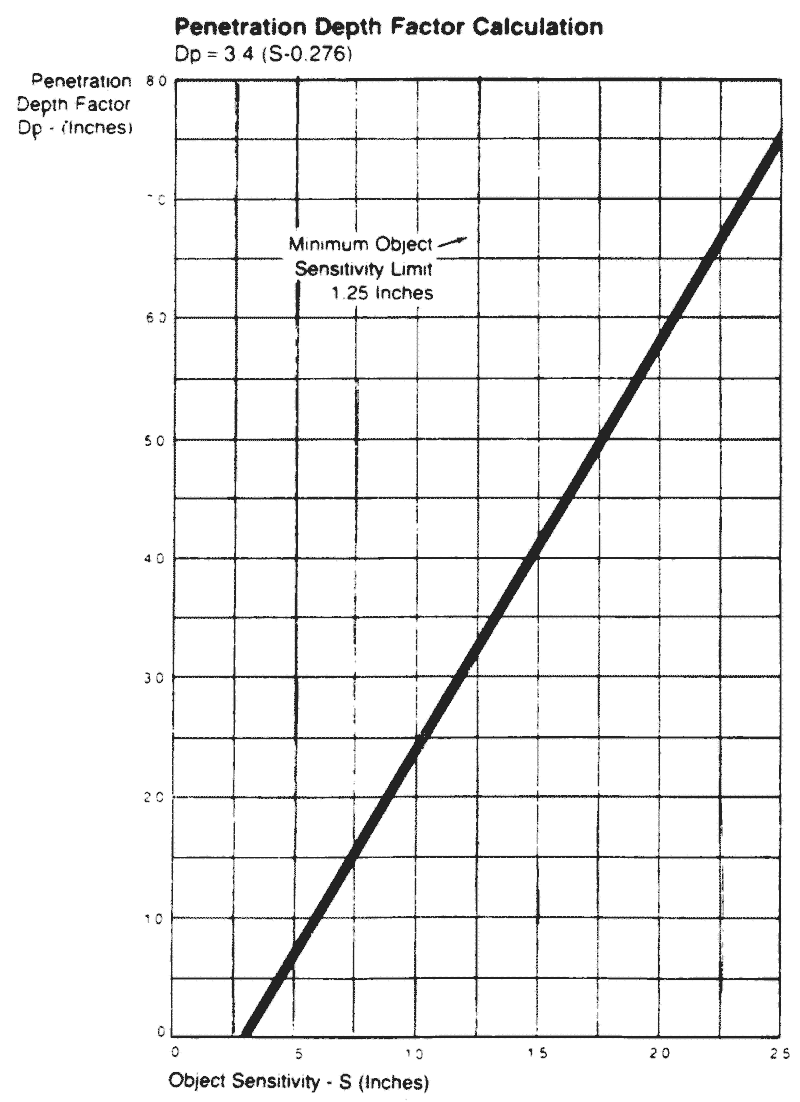
Supplemental safeguarding shall be used to protect all areas of access to the point of operation which are unprotected by the PSDI presence sensing device. Such supplemental safeguarding shall consist of either additional light curtain (photo-electric) presence sensing devices or other types of guards which meet the requirements of paragraphs (c) and (h) of this section.
(A) Presence sensing devices used as supplemental safeguarding shall not initiate a press stroke, and shall conform to the requirements of paragraph (c)(3)(iii) and other applicable provisions of this section, except that the safety distance shall comply with paragraph (h)(9)(v) of this section.
(B) Guards used as supplemental safeguarding shall conform to the design, construction and application requirements of paragraph (c)(2) of this section, and shall be interlocked with the press control to prevent press PSDI operation if the guard fails, is removed, or is out of position.
Hand tools. Where tools are used for feeding, removal of scrap, lubrication of parts, or removal of parts that stick on the die in PSDI operations:
(A) The minimum diameter of the tool handle extension shall be greater than the minimum object sensitivity of the presence sensing device(s) used to initiate press strokes; or
(B) The length of the hand tool shall be such as to ensure that the operator's hand will be detected for any safety distance required by the press set-ups.
The following checks shall be made at the beginning of each shift and whenever a die change is made.
(A) A check shall be performed using the test rod according to the presence sensing device manufacturer's instructions to determine that the presence sensing device used for PSDI is operational.
(B) The safety distance shall be checked for compliance with (h)(9)(v) of this section.
(C) A check shall be made to determine that all supplemental safeguarding is in place. Where presence sensing devices are used for supplemental safeguarding, a check for proper operation shall be performed using the test rod according to the presence sensing device manufacturer's instructions.
(D) A check shall be made to assure that the barriers and/or supplemental presence sensing devices required by paragraph (h)(9)(ix) of this section are operating properly.
(E) A system or visual check shall be made to verify correct counterbalance adjustment for die weight according to the press manufacturer's instructions, when a press is equipped with a slide counterbalance system.
Prior to the initial use of any mechanical press in the PSDI mode, two sets of certification and validation are required:
(A) The design of the safety system required for the use of a press in the PSDI mode shall be certified and validated prior to installation. The manufacturer's certification shall be validated by an OSHA-recognized third-party validation organization to meet all applicable requirements of paragraphs (a) through (h) and appendix A of this section.
(B) After a press has been equipped with a safety system whose design has been certified and validated in accordance with paragraph (h)(11)(i) of this section, the safety system installation shall be certified by the employer, and then shall be validated by an OSHA-recognized third-party validation organization to meet all applicable requirements of paragraphs (a) through (h) and appendix A of this section.
The operator training required by paragraph (f)(2) of this section shall be provided to the employee before the employee initially operates the press and as needed to maintain competence, but not less than annually thereafter. It shall include instruction relative to the following items for presses used in the PSDI mode.
(A) The manufacturer's recommended test procedures for checking operation of the presence sensing device. This shall include the use of the test rod required by paragraph (h)(10)(i) of this section.
(B) The safety distance required.
(C) The operation, function and performance of the PSDI mode.
(D) The requirements for hand tools that may be used in the PSDI mode.
(E) The severe consequences that can result if he or she attempts to circumvent or by-pass any of the safeguard or operating functions of the PSDI system.
[39 FR 23502, June 27, 1974, as amended at 39 FR 41846, Dec. 3, 1974; 40 FR 3982, Jan. 27, 1975; 43 FR 49750, Oct. 24, 1978; 45 FR 8594, Feb. 8, 1980; 49 FR 18295, Apr. 30, 1984; 51 FR 34561, Sept. 29, 1986; 53 FR 8353, 8358 Mar. 14, 1988; 54 FR 24333, June 7, 1989; 61 FR 9240, Mar. 7, 1996; 69 FR 31882, June 8, 2004; 76 FR 80739, Dec. 27, 2011; 77 FR 46949, Aug. 7, 2012; 78 FR 69550, Nov. 20, 2013]