The OSHA Strategic Partnership Program (OSPP) provides opportunities for OSHA to partner with employers, workers, professional or trade associations, labor organizations, and other interested stakeholders. OSHA Strategic Partnerships are unique agreements designed to encourage, assist, and recognize partner efforts to eliminate serious hazards and enhance workplace safety and health practices. OSHA Strategic Partnerships establish specific goals, strategies, and performance measures to improve worker safety and health. OSHA Strategic Partnerships focus on improving safety and health in major corporations, government agencies, at large construction projects and private sector industries where OSHA has jurisdiction. Most OSHA Strategic Partnerships are based out of local OSHA Area or Regional Offices.
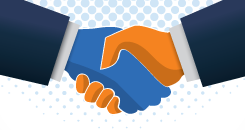