Combustible Dust Expert Forum
Washington, D.C.
May 13, 2011
Meeting Summary Report
Prepared for:
U.S. Department of Labor
Occupational Safety and Health
Administration
Directorate of Standards and Guidance
Prepared by:
Eastern Research Group, Inc.
Lexington, MA 02421
July 20, 2011
Table of Contents
1 Introduction
2 Opening Remarks
3 Administration of the Meeting
4 Topics for Group Discussion
4.1 Scope
4.2 Focus on Preventing Secondary Explosions
4.3 Existing Facilities
4.4 Multiple Layers of Protection
5 Concluding Remarks
Appendix A. Biographies of Invited Experts
Appendix B. Information Provided by OSHA to Invited Experts
Appendix C. Handouts from Dr. Ali Rangwala
Acronyms and Abbreviations
AHJ | Authority Having Jurisdiction |
---|---|
ANPR | advanced notice of proposed rulemaking |
ASTM | American Society for Testing and Materials |
CSB | U.S. Chemical Safety and Hazard Investigation Board |
DOL | Department of Labor |
ERG | Eastern Research Group, Inc. |
Kst | deflagration index |
MIE | minimum ignition energy |
MOC | management of change |
NEP | National Emphasis Program |
NFPA | National Fire Protection Association |
OSHA | Occupational Safety and Health Administration |
PPE | personal protective equipment |
PSM | process safety management |
SBREFA | Small Business Regulatory Enforcement Fairness Act |
1 Introduction
This report summarizes the discussion during an expert forum convened by the Occupational Safety and Health Administration (OSHA) pertaining to its rulemaking on combustible dust. The one-day meeting was held on May 13, 2011, at the U.S. Department of Labor in Washington, D.C. The purpose of the meeting was to obtain expert input on protective and cost-effective regulatory options for a combustible dust standard.
The expert forum is the latest in a series of OSHA activities on its combustible dust rulemaking. On October 21, 2009, OSHA issued an advanced notice of proposed rulemaking (ANPR) for a combustible dust standard. Since issuing the ANPR, OSHA has held six stakeholder meetings on combustible dust. OSHA invited 14 experts to participate in the latest forum. Appendix A lists the experts' names and affiliations and includes brief biographies of their relevant experience.
The experts included individuals from industry, academia, government, insurance underwriters, and unions and those involved with standards development. Expert participants were provided with background information and discussion questions prior to the meeting (see Appendix B). All experts were given the opportunity to provide verbal comments at the meeting; no written comments were requested. OSHA publicly announced the meeting in a press release issued on April 28, 2011. The press release explained that limited space would be available for interested members of the public to observe (but not participate in) the meeting and asked interested parties to register. Approximately 60 nonparticipating observers attended the meeting.
Eastern Research Group, Inc. (ERG) provided logistical support for the forum, and a technical writer from ERG attended the meeting and prepared this summary report. This report captures the main discussion points that experts raised during the meeting, but it is not a verbatim transcript of the meetings. The content throughout this report reflects the remarks made by the experts at the meeting and should not be viewed as the opinion of ERG or OSHA.
2 Opening Remarks
The expert forum began with brief opening remarks offered by the following OSHA officials:
David Michaels, Assistance Secretary of Labor for Occupational Safety and Health, welcomed the experts, observers, and OSHA attendees. Dr. Michaels remarked that the purpose of the meeting was to help OSHA determine the best way to write the combustible dust standard. He also described the next steps of the rulemaking process, including the need to convene a panel per the Small Business Regulatory Enforcement Fairness Act (SBREFA).Dr. Michaels also described the next steps of the rulemaking process, including the need to convene a panel per the Small Business Regulatory Enforcement Fairness Act (SBREFA).
Jordan Barab, Deputy Assistant Secretary of Labor for Occupational Safety and Health, recalled his experience working on combustible dust investigations with the U.S. Chemical Safety and Hazard Investigation Board (CSB). He noted that OSHA's first priority is to protect workers, which sometimes involves issuing standards. Mr. Barab also emphasized that OSHA is committed to ensuring that standards make sense in the workplace. He mentioned that although this forum is one of many opportunities for public input, the discussion will serve to inform the direction of the standard.
Dorothy Dougherty, Director, Directorate of Standards and Guidance, thanked the experts for their time and encouraged them to share their opinions to help OSHA move forward with a combustible dust standard. Ms. Dougherty also welcomed the observers and thanked them for attending. She noted that observers and the public will have opportunities outside of the forum to comment on the rulemaking. Ms. Dougherty indicated that developing a combustible dust standard poses many unique challenges because of the diversity of dusts, facilities, and processes involved. Although the series of stakeholder meetings already provided OSHA with many viewpoints and opinions, the agency decided to convene the expert forum to seek expert opinion on several specific topics critical to the rulemaking process. Ms. Dougherty added that the scheduled discussion topics are only a subset of the technical issues that OSHA is considering in the rulemaking process, and she noted that OSHA is not seeking consensus among the invited experts on any issue.
Department of Labor (DOL) personnel on the panel were: Amanda Edens, Deputy Director, Directorate of Standards and Guidance; Mat Chibbaro, Fire Protection Engineer, Office of Safety Systems; Bob Burt, Director, Office of Regulatory Analysis; and Edmund Baird, Attorney, Office of the Solicitor.
3 Administration of the Meeting
The meeting was facilitated by Barbara Upston from Management Consulting Associates. Ms. Upston provided the experts with an overview of the meeting agenda and format. She emphasized that OSHA is not seeking consensus on the discussion topics, but is rather seeking the individual opinion of each of the invited experts. Ms. Upston reiterated that the observers are not participants in the meeting and should refrain from making comments or holding side conversations. She asked the experts to introduce themselves and briefly describe their experiences with combustible dust (see Appendix A for expert participant biographies). Ms. Upston also reviewed the specific questions that OSHA requested the experts to address (see Appendix B).
4 Topics for Group Discussion
The discussion topics at the expert forum were organized into four sessions: the scope of the combustible dust standard, prevention of secondary explosions, existing facilities, and multiple layers of protection. For each session, a DOL official introduced the general topic after which the experts provided comments. The following sections summarize the introductions made by DOL officials and the comments made by the experts for each session. Comments are grouped together by topic, without reference to the identity of the commenter, and do not necessarily appear in the order in which the discussion occurred.
4.1 Scope
Mr. Burt (OSHA) introduced the first discussion topic: the scope of the combustible dust standard. First, he compared the grain handling facilities standard (29 CFR 1910.272) - an earlier standard that addressed many industry-specific safety issues, including combustible dust - to a general combustible dust standard. He noted that the grain handling facilities standard was developed for a limited number of well-defined facilities having well-understood hazards in a few discrete processes. In contrast, a general combustible dust standard would cover all types of facilities with combustible dust hazards, spanning a wide variety of processes and dust types. The broad scope has caused OSHA to contemplate different rulemaking approaches, such as a performance-based approach versus a specification approach that mandates use of certain engineering and administrative controls.
Mr. Burt also discussed the effectiveness of the grain handling facilities standard. OSHA estimated at the time that the standard costs grain handling facilities over $100 million in 2010 dollars per year. However, retrospective studies have shown that the standard also had substantial benefits (e.g., reduced accidents and fatalities). Mr. Burt pointed out that a general combustible dust standard is quite different because it will cover tens of thousands of businesses (including many small businesses) across many industries with a wide range of processes and dust types. Mr. Burt concluded that the challenge OSHA faces when developing the combustible dust standard is writing an effective rule that covers a wide variety of processes, but at a reasonable cost.
Mr. Burt noted that the scope of the standard - defined in the first sentence of the rule - essentially tells employers whether the standard applies to their facilities. The scope can be broad (e.g., any worker with occupational exposure to certain chemicals) or narrow (as in the grain handling facilities standard). OSHA recognizes that including all facilities with any amount of combustible dust on site, regardless of the magnitude of the actual hazard, is inappropriate. However, the balance OSHA has to achieve with respect to scope is to avoid costs for employers with facilities where the hazard is minimal while assuring that facilities with serious combustible dust hazards are brought into the scope of the standard.
4.1.1 Would it be appropriate to exclude certain materials based on their explosibility? Should the exclusion go beyond noncombustible dusts to some minimally combustible dusts as well? If so, what criteria would appropriate? There are dusts in the low Kst range that have produced fatal incidents - including, most strikingly, sugar dust.
Several experts stated that the standard should not attempt to exclude materials based on a measure of explosibility. One expert noted that combustible dust is any dust that can support flame propagation, and the American Society for Testing and Materials (ASTM) has already developed a testing methodology (ASTM E-1226) that can be used to determine if a dust meets that criterion. This expert felt that any dust that supports flame propagation per the ASTM method should be considered combustible by OSHA's standard.
Another expert stated that defining a threshold based on explosibility (e.g., excluding dusts with a deflagration index, or Kst value, less than 50 bar-meters/second) has inherent limitations and should not be attempted. One expert observed that in the data provided by OSHA (see Appendix B), dusts with a hazard class of ST1 - the least explosive class of dusts - caused the most incidents and the most injuries by gross numbers compared to dusts with hazard classes of ST2 and ST3. Additionally, a recent incident at a steel manufacturing facility in Tennessee that caused one fatality and one injury was reportedly caused by a dust with an explosion severity of only 0.007. Thus, this expert felt that explosion severity and Kst should not be used to limit the scope of the standard because even minimally combustible dusts have been shown to cause injuries and fatalities. Another expert noted that an incident at a textile mill in Massachusetts that caused half a billion dollars of property damage and severely burned 14 workers was due to a misperception that the dust was not hazardous because it had a "low"; Kst around 50 and a minimum ignition energy (MIE) between 300 and 400 millijoules.
Other experts suggested measures of explosibility that they felt could be used to limit the scope of the standard. However, multiple experts generally suggested that no single parameter could be used as a hard line to exclude materials from the standard. The following paragraphs summarize the range of opinions expressed on this topic.
One expert supported using the equations for explosion severity and ignition sensitivity - as defined in National Fire Protection Association (NFPA) 499, Recommended Practice for the Classification of Combustible Dusts and of Hazardous (Classified) Locations for Electrical Installations in Chemical Process Areas - to help define what types of controls different materials require. The expert recognized that materials with low ignition sensitivity (i.e., hard to ignite) and low explosion severity (i.e., producing little pressure once ignited) might still present a hazard but felt that such materials could be safely controlled with preventative measures rather than extensive engineering controls. This expert also said that equations in NFPA 654 used to calculate maximum allowable dust accumulation thickness might not capture all possible dust hazards (e.g., dust with a high MIE might also be thermally unstable), but he still supported use of these equations as a means of distinguishing between different degrees of combustible dust hazards. However, one expert strongly disagreed with the use of the NFPA 654 equations, because incidents have occurred at facilities where employers interpreted the results to mean that there was no significant hazard (e.g., the textile mill in Massachusetts mentioned previously). The equations are particularly inapplicable to instances of piloted ignition (i.e., instances where a spark or small flame initiates a larger event). The previous expert responded that the incident at the textile mill was a flash fire rather than a deflagration, and effective housekeeping would have prevented the incident without the need for sophisticated and costly engineering controls.
Another expert supported an approach of excluding nonexplosible materials based on their chemistry, such as sodium bicarbonate, rock dusts, and wholly oxidized materials. For materials of marginal combustibility, this expert preferred to use MIE rather than Kst to assess explosion risk. However, the expert also noted that even hard-to-ignite materials can be hazardous (e.g., if ignited by a primary explosion). The expert later clarified his comment, stating that he was not proposing MIE as the sole parameter to define the scope of the standard but wanted to shift the focus away from Kst. He said no single parameter is sufficient to define a hazard and that a risk evaluation may be warranted to assess the full range of material properties that contribute to explosibility. A problem that facilities, and OSHA, will face is obtaining adequate data. Another expert echoed the comment that MIE is an important parameter for evaluating risk. When assessing a hazard, the expert considers: 1) whether the process is putting energy into the material and 2) whether the increase in temperature could cause ignition.
One expert noted that there will never be consensus on the best measure of explosibility or ignitability. Rather, OSHA must utilize what is known now to pass a regulation and start protecting workers immediately, while still recognizing the need for continuing research on combustible dust. The agency should incorporate enough flexibility into the rule to accommodate changing technology and knowledge. For example, explosibility is currently used as an indicator for flash fire hazard, but a new measure of flash fire hazard might eventually be developed.
Similarly, another expert commented that as many as 45 different parameters can be used to characterize flammability. These parameters are quantified by numerous different test methods, and the methods are frequently revised. As a result, this expert felt that it is very difficult to quantify the hazard with only one test method, or even a few test methods in combination. He also noted that the grain handling facilities standard used housekeeping and training (i.e., education) to mitigate the hazard without requiring any measurements to characterize dust hazard potential. This expert eventually suggested undertaking a significant research effort to study dust flammability to defend which parameters provide the best metric of hazard; he also encouraged OSHA to develop an educational module on housekeeping. The expert provided two handouts at the forum: one describing material flammability and the other depicting the dynamics of a dust flame (see Appendix C).1
The experts also discussed how facilities might be expected to acquire testing data necessary to determine if a new combustible dust standard applies to them. One expert felt that the standard should not require extensive testing for employers who already know and recognize that they have a hazard. Rather, explosibility testing is an issue for facilities that handle marginally explosive dusts. This expert remarked that explosibility tests conducted using the standard 20-liter test apparatus have given "false positives"; for some nonexplosible materials (i.e., a nonexplosible material was found to have a low Kst value). A proposed revision to NFPA 654, Standard for the Prevention of Fire and Dust Explosions from the Manufacturing, Processing, and Handling of Combustible Particulate Solids, suggests testing the dust in a larger apparatus in cases where testing with the 20-liter test apparatus results in a low Kst value.
Several experts noted that publishing some type of database or tables of explosibility data (e.g., material, particle size, Kst) would assist employers - particularly small businesses - by reducing the need for testing. Such a database would be restricted to well-behaved and well-defined materials, however, and not every material has well-established properties. Additionally, the fact that explosibility varies greatly with dust particle size makes compiling such a database more challenging. One expert warned that much of the available test data predates the standardized ASTM test methodology, which would raise questions about data comparability.
Finally, one expert added that OSHA should distinguish between prevention and protection in its consideration of explosibility. Ignition sensitivity is useful for determining what preventive measures might be required (e.g., monitoring bearing temperature in a hammer mill). In contrast, Kst is an engineering parameter that is used to design protective measures. This expert cautioned against having a single "defining"; parameter for applicability purposes.
4.1.2 Would it be appropriate to exclude industries that have a history of fewer incidents? Fewer incidents with injuries? Fewer incidents with fatalities? Where should the cutoff be?
One expert noted that the insurance industry uses their own loss experience to focus on hazardous industries. For example, according to one of the experts, Factory Mutual has published information2 indicating that the woodworking and food industries are some of the most hazardous sectors, whereas other industries (e.g., textile and printing industries) have had only one small incident each over the last 20 years. This expert supported using industry history as a guide, although he recognized that defining any limits would be very difficult.
Other experts rejected the notion of excluding industries based on incident history. These experts believed that the available data is an unreliable measure of potential hazard. One expert felt that the nature of dust explosions and the vulnerability of a facility are inherently random, and that available incident data is inadequate to provide the statistical confidence needed to exclude industries. Two more experts added that industries should not be excluded based on performance history; a good track record does not imply that there is zero hazard, nor is it an indicator of future performance. These experts emphasized that current data is insufficient to justify such exclusions.
Another expert gave reasons why incident data might not be sufficient for applicability purposes, based on experiences the expert gained from surveying employees in various sectors of the food manufacturing industry. The expert stated that employees are generally aware of incidents occurring but may not always report them, particularly for near misses or incidents that can be quickly addressed. These smaller incidents are often not recognized as precursors to larger incidents. This expert remarked that basing the scope of the standard on incident history is going to miss conditions, which might lead to bigger incidents due to underreporting. Additionally, relying on the incident data provided to the experts (see Appendix B) will exclude incidents resulting in property damage, but not worker injuries or fatalities. The expert noted that fires and explosions resulting in property damage are just as important to consider, because in many cases, these incidents would have seriously injured or killed employees, had they been in the immediate vicinity at the time the incident occurred. Another expert supported the notion that incident history should not be used as a basis of exclusion for various reasons, such as a lack of information on small incidents. This expert noted that incidents often go unreported because combustible dust is not a well-recognized hazard.
4.1.3 Would it be appropriate to exclude smaller entities? If so, should this be based on facility size, number of employees, or some other threshold? If not, would a different level of controls be appropriate?
One expert felt that being able to exclude the "mom and pop"; small businesses is valuable, but that defining any sort of size limitation will be very difficult. Another expert noted that NFPA 664, Standard for the Prevention of Fires and Explosions in Wood Processing and Woodworking Facilities, does attempt to limit its scope, with the intent of excluding small furniture manufacturers and cabinet makers. The standard uses facility square footage and minimum required dust collection flow rates as proxies for facility size. Facilities not meeting either threshold are excluded from this standard and from NFPA 654, although the facilities are still encouraged to apply some of the standard's recommendations.
One expert noted that a facility using smaller quantities of material will have a more localized hazard; however, workers at these smaller facilities are also often in closer proximity to the hazard. The expert suggested focusing on administrative controls in smaller facilities because engineering controls can be difficult and costly to apply to manual operations.
Another expert cautioned against letting facility size factor into the scope of the combustible dust standard. The expert cited an example of a recent incident involving three fatalities that occurred at a small (15 to 20 employees) chemical manufacturing facility in West Virginia. This expert argued that such incidents illustrate why facility size should not be used to limit the scope of the combustible dust standard.
4.1.4 Are there any other scope-limiting approaches that would be appropriate?
One expert proposed a conceptual approach to limiting scope by excluding facilities where it would be inherently impossible for a substantial dust cloud to form (e.g., kitchen operations). He noted that this would be similar to a scope-limiting approach in NFPA 484, Standard for Combustible Metals, which lists threshold quantities of materials (e.g., 5 pounds) above which the standard applies. The expert later clarified that he does not necessarily support the NFPA thresholds verbatim, and that he is suggesting a combination of two criteria - the ability to form a suspended dust cloud and the threshold mass of dust material - to limit scope.
Another expert remarked that establishing threshold quantities is not a novel concept, as it has already been employed in the process safety management (PSM) standard (§ 1910.119). Additionally, two experts noted that while NFPA 654 has not been able to endorse a facility threshold size because of the breadth of covered facilities, the standard does limit the scope for certain requirements within the standard. For example, certain engineering control requirements in NFPA 654 apply only when an explosion hazard exists - a distinction that is based, for example, on the volume of an air-material separator or the mass of dust present. The mass of dust dictates the amount of energy to be released and thus, the potential for injuries. NFPA 654 recognizes that certain engineering controls are not practical to implement when dusts are used in limited quantities, whereas other controls are applicable to all facilities because they control the amount of dust present.
One expert noted that OSHA should not use particle mass median diameter to limit scope. This expert remarked that some standards use mass median diameter as a threshold, presumably because the presence of large particles can prevent deflagrations by sucking up heat and acting as quenching nuclei. This expert disagreed with that approach because small particles will almost always separate from the large particles during certain processes (e.g., in a cyclone). This expert supported a standard that regulates all combustible particulate solids regardless of size, because fine particles capable of supporting deflagration have the potential to form from larger particles through attrition and handling.
Another expert argued against scope-limiting criteria due to the human cost of injuries and fatalities. This expert felt that the standard must cover all facilities with a flash fire or explosion hazard in order to protect all workers that might be at risk. Noting that some facilities are still uneducated about combustible dust hazards, he encouraged OSHA to include even small facilities in the standard such that they are required to perform hazard assessments for their combustible dusts.
Other topics raised during the discussion of scope included the following:
- Several experts discussed the role of risk in defining the scope of the standard, because the standard's applicability criteria can be viewed as an acceptable degree of risk. Some experts expressed that no facility or activity would ever be 100 percent risk free, which necessitates approaching the standard from a risk-based standpoint. One expert clarified the difference between hazard and risk: a hazard is something that yields unacceptable consequences, but risk describes the likelihood that a hazard will occur.
- One expert used a past incident to illustrate difficulties OSHA might face in developing a combustible dust standard. In this incident, a facility was pneumatically conveying combustible dust through nonconductive piping, which caused an electrostatic discharge that triggered an explosion. The expert indicated that "the only way"; OSHA could prevent such an incident is through a general educational bulletin informing employers that they should never pneumatically convey combustible dust in nonconductive piping.
- One expert noted that the incident list provided by OSHA might include some materials that are thermal decomposition hazards (e.g., benzoyl peroxide) rather than combustible dust hazards. He encouraged OSHA's standard and analysis of previous incidents to focus on combustible dust hazards.
4.2 Focus on Preventing Secondary Explosions
Mr. Chibbaro (OSHA) introduced the second discussion topic - a combustible dust standard that focuses on preventing secondary events. The rationale behind this approach is to prevent the most catastrophic events, which tend to be secondary explosions. Two ways to accomplish this in a combustible dust standard are to 1) omit all requirements that only prevent primary explosions (e.g., ignition controls) or 2) omit requirements that only mitigate the effect of explosions after they are initiated (e.g., explosion venting). He asked the experts to consider the impact of the proposed approaches on employee safety and on cost. He also requested data on the extent to which injuries and fatalities are caused by primary versus secondary explosions and sought input on thresholds for accumulations of dust that trigger housekeeping requirements.
4.2.1 Would focusing on secondary explosions prevent most multi-fatality events? How could OSHA estimate the number of incidents or fatalities prevented by such an approach? Is data available that indicate whether fatalities were due to primary vs. secondary events?
4.2.2 What would be the impact of omitting provisions that only address primary explosions? An example would be ignition-source controls within processing or dust-collection equipment.
4.2.3 What would be the impact of omitting provisions that minimize the effects of an incident, were one to occur? Examples include explosion vents and explosion-suppression systems.
These questions presented very similar issues and the experts did not distinguish which they were addressing, so they are grouped together:
Three experts provided their impressions of the relative proportions of injuries and fatalities caused by primary versus secondary explosions. One expert noted that he investigated more than 300 casualties caused by dust deflagrations, with approximately one-third being fatalities. Out of these incidents only two individuals were victims of primary explosions. One incident involved an exploding drier, and the other a natural gas explosion. Another expert had a different experience with casualties: he said he has evaluated many incidents where the primary event was responsible for both "horrific burn injuries"; and fatalities, but he did not quantify the relative proportion of fatalities caused by primary versus secondary explosions. A third expert noted that primary events have killed four or five people this year already.
Another expert noted that the grain handling facilities standard, which relies heavily on housekeeping, has been very effective; there has been only one major explosion at a grain handling facility since the standard was passed, and that reportedly occurred because the facility was not complying with the standard. That expert said that eliminating dust accumulations should be a top priority because certain engineering controls (e.g., explosion suppression) are not always reliable. The expert suggested focusing the standard on housekeeping, at least initially, and possibly phasing in additional requirements, such as engineering controls, in future years after facilities have implemented the required housekeeping measures. He encouraged OSHA to help facilities implement the most cost-effective measure.
One expert commented that OSHA is better equipped to enforce prevention of secondary explosions rather than primary explosions. It is much easier, he clarified, for inspectors to look for fugitive dust than to evaluate the effectiveness of primary explosion controls - an assessment that requires engineering skills and a thorough understanding of process equipment. Nonetheless, the expert still did not advocate for a standard that omits provisions preventing primary explosions due to their potential hazards. For example, he said unprotected primary explosions in pressurized vessels can cause substantial damage to facility structures and generate shock waves and flying projectiles that can have very serious consequences. Eventually, this expert noted that requiring facilities to conduct hazard assessments might be preferred to a standard that focuses on preventing primary or secondary explosions. Though he acknowledged that hazard assessments are more costly given the education and training required, the expert added that both NFPA and European combustible dust standards have required hazard assessments and compliance options.
Another expert emphasized the importance of understanding combustible dust hazards, which will vary with facility-specific conditions (e.g., types of production equipment, types of dusts, types of building envelopes). This expert felt that OSHA's standard must not focus on one type of control to the exclusion of others and therefore, should not exclude controls that prevent primary explosions or mitigate the effects of an incident. The expert noted, however, that the standard should emphasize regulations that can be enforced.
Another expert supported these points, noting that omitting provisions that either address primary explosions or mitigate the effects of an explosion is a risky approach. Employers are likely, he explained, to implement the standard's minimum requirements and assume that by following those provisions their facilities are protected, when that might not be the case.
Some experts provided further context on why housekeeping is a crucial tool for mitigating secondary explosions. One expert estimated that 95 to 99 percent of injuries and fatalities could be prevented by proper housekeeping. This expert said that effective housekeeping is more important than installing controls on unprotected dust collectors or silos, although he later clarified that the standard should also require protective measures on certain classes of process equipment (e.g., conveyors, dust collectors, bins) that would result in the greatest safety benefits and protection of facility assets.
Several experts recommended that any new housekeeping requirements explicitly address the need for removing hidden, non-obvious dusts. One expert noted that visible accumulations of combustible dusts can be avoided relatively easily using straightforward housekeeping measures. The challenge, rather, is coping with "invisible"; dust, such as that found in enclosed conveyors or above suspended ceilings. Another expert added that requirements for removing hidden dust (e.g., in ductwork, on elevated surfaces, behind sheathing) are more important than debating a specific dust accumulation threshold for "visible"; dust. Another expert supported this concept, noting that facilities' written housekeeping programs typically target dusts that routinely accumulate on working surfaces, without addressing accumulations on overhead surfaces (e.g., rafters) and other difficult-to-access locations. Finally, an expert described a novel approach that companies had successfully implemented to prevent dusts from accumulating on overhead surfaces: installing oscillating fans over hard-to-reach areas. This expert also noted that the Fire Protection Research Foundation is conducting ongoing research on factors that cause combustible dusts to become entrained in air, which eventually can lead to dust accumulations.
In response to an inquiry from Mr. Chibbaro (OSHA), one expert said he was unaware of any correlation between the cost of installing protective features and the degree of protectiveness provided, most likely due to the randomness of certain dust-related incidents. He added that any relationship between cost and protectiveness is likely a complex non-linear relationship. Another expert recommended that OSHA look at actual facility-specific investments in implementing engineering controls. He specifically encouraged OSHA to gather information on costs associated with protecting grain elevators located in Prince Rupert, British Columbia, as the investments at this highly strategic location might provide insights to the upper bounds of costs for implementing engineering controls. In a different context, one expert stated that, in general, ninety percent of the costs are spent eliminating the last ten percent of the risk.
Experts also raised several concerns about relying too heavily on housekeeping. One expert noted that many facilities already lack sufficient personnel for housekeeping and that employers usually balk at adding labor strictly for housekeeping duties. Additionally, because employers value production over housekeeping, workers are often not given enough time for housekeeping. Another expert raised the issue that many facilities contract out their housekeeping services, and that the contractors might not be aware of the hidden places where dust accumulates. He indicated that hiring full-time, in-house cleaning staff for specific equipment can reduce fires and contribute to a safer workplace. Another expert noted that several fairly significant explosions have been attributed to improper housekeeping procedures. Employers should take care to implement housekeeping in a cautious fashion and reduce their reliance on compressed air for cleaning hard-to-reach places. A third expert described the hierarchy of housekeeping methods documented in several NFPA standards and proposed revisions to those standards: 1) vacuuming (with correctly classified equipment), 2) sweeping and water wash-down, and 3) using compressed air blow downs.
One expert noted that reducing dust accumulations is only one way of preventing secondary explosions. Depending on a facility's specific situation, establishing a dust-free environment might not always be feasible. In such cases, other ways of reducing risk - such as minimizing the possibility of the primary event, controlling ignition sources, or isolating the process - might be an effective means for reducing risks of injuries or fatalities, even if dust accumulations remain. To illustrate his point, the expert noted that requiring a facility to have an entire housekeeping crew remove accumulated dusts from facility locations that are effectively isolated and otherwise unoccupied might not be an effective risk-reduction measure. Focusing strictly on housekeeping strategy will not serve such facilities well. Another expert noted that, in addition to housekeeping, knowing the flammability of the material is important, because a primary explosion provides sufficient energy to trigger any secondary explosion. In the case of secondary explosions Kst is a good gauge. In addition, some dusts are so explosive that even a very thin layer can be hazardous, necessitating controls other than housekeeping.
Mr. Burt (OSHA) asked the experts how the standard can ensure that housekeeping takes place. He cited two specific concerns about housekeeping programs: 1) during an economic downturn, it is not uncommon for facilities to cut back on housekeeping and 2) following increases in production rates, some facilities fail to increase housekeeping efforts commensurately. One expert responded by noting that significant increases and decreases in business do correlate with combustible dust events. He said OSHA should require recordkeeping of housekeeping to ensure that housekeeping activities occur as planned. Using this approach, OSHA inspectors can review records to assess how frequently the facility has been removing dust, rather than relying only on the physical presence of dust, which is an imperfect indicator because facilities might conduct extensive housekeeping in advance of announced inspections. Another expert expressed support for this idea.
The experts offered various other observations when discussing housekeeping requirements. For instance, one expert encouraged OSHA to proceed with promulgating a combustible dust standard because threat of enforcement is an effective incentive for facilities to implement controls. This expert also recommended that the standard provide incentives and rewards for finding hidden dust so that employees do not view housekeeping as a menial task. Another expert felt strongly that top levels of management must have a firm commitment to effective housekeeping and an understanding that good housekeeping supports their business interests (and should not be viewed as ancillary to production). The expert acknowledged that OSHA cannot regulate this type of commitment, but noted that lower insurance premiums might be a different incentive for good housekeeping. Another topic raised by an expert was the need for employers to view housekeeping as a hazard mitigation strategy, and to not confuse this with janitorial practices, grounds maintenance, and other aesthetic measures. Finally, another expert noted that employers appear to respond to OSHA's compliance assistance and informational materials, and thus recommended a four-part strategy consisting of: 1) an educational component; 2) language in the standard requiring that contractors be educated and held accountable; 3) enforcement through OSHA inspections; and 4) employee involvement, including a means for workers to voice concerns when their time is diverted from housekeeping to production. This expert also stressed mandating employee involvement in regular inspections, because workers know when something has gone wrong and often have already implemented (potentially hazardous) makeshift procedures or maintenance activities as corrective action.
4.2.4 Is there a simple way to define quantities of dust that are necessary to trigger cleaning action to prevent secondary explosions? Specifically, what method could be implemented by small entities without calculations or outside expertise?
One expert remarked that the need for housekeeping should be dictated by the rate at which dust is generated. Two other experts noted that certain NFPA standards (e.g., 654, 664) have established maximum allowable dust accumulation thicknesses. One of the experts said he could not identify a single dust-related incident with injury or loss of life at facilities that had met NFPA's applicable dust accumulation criteria. One expert suggested that many facilities could use the simple criteria that if you could see your footprints, there is too much dust. One expert indicated that OSHA's standard can include acceptable levels of dust accumulation, provided that the standard also gives employers compliance options when those criteria cannot be met.
4.2.5 How much dust accumulation on horizontal surfaces results from failure to install or maintain dust-collection systems as recommended in the NFPA standards? For example, if NFPA-recommended dust-collection equipment was to be omitted from a packaging operation, the fugitive dusts emitted, but not captured, would eventually accumulate on surfaces.
Some experts encouraged OSHA to require facilities to control dust releases at their sources, rather than focus strictly on housekeeping. One expert referenced Section 3 of FM Global data sheet 7-76 as support for the importance of controlling fugitive dust. This expert felt that OSHA's standard must have some requirement for basic preventative controls, such as keeping the dust contained (as in a dust collector) and isolating potentially hazardous equipment. These steps will help prevent or minimize the consequences of initiating events and ensure these events do not result in secondary explosions.
One expert considered housekeeping to be a "band-aid"; for correcting deficiencies in existing equipment, because he viewed housekeeping as cleaning up dust that should not have escaped process equipment in the first place. Consistent with this remark, some experts recommended that facilities follow general approaches outlined in NFPA standards: 1) equipment should be designed to contain dust and maintained in good condition, and 2) facilities should implement ignition source controls. Housekeeping (and other controls that mitigate the consequences of an explosion) should only be used as the final measure of defense and as part of a larger systematic risk-reduction approach. One expert added that having enough workers to perform housekeeping is typically not an issue if prevention methodologies are used to limit the escape of fugitive dust. He further noted that the costs of maintaining process equipment and dust controls in good condition is usually less than equipment repair and other costs that facilities incur following explosions or major fires. Another expert made a comparison with safety standards for processing flammable liquids. Those standards are written to ensure that liquids are confined within process equipment, thus reducing the likelihood that clouds of flammable vapors will form. The expert suggested an analogous approach for combustible dust: ensuring first that dust remains inside process equipment to avoid hazards associated with dust clouds and accumulated settled dust. One expert suggested drawing on the experience of the petroleum and chemical industry regarding containment of process chemicals.
Another expert emphasized the importance of maintenance in preventing the escape of fugitive dust. This expert noted that a major explosion at a sugar mill reportedly occurred one week after inspections of the ducting, airflow, and dust collections system revealed incorrectly installed piping, piping plugged with sugar, and fans operating below the required velocities. Noting that effective maintenance could have helped prevent, or minimize the consequences of, the incident, the expert emphasized that equipment maintenance is an important element of combustible dust control programs.
The experts also discussed the relative cost of containing dust at the source (e.g., through engineering controls) versus removing settled dust via housekeeping programs. One expert described a client with 30 facilities that are being upgraded in the wake of OSHA's combustible dust National Emphasis Program (NEP). The expert estimated that every dollar spent on containment, capture, and control of combustible dust saves 10 dollars on upgrading the electrical classification and 100 dollars on housekeeping over a 10-year time period. In short, this expert said that investing resources on engineering controls was found to save money on housekeeping. Some other experts commented on the relative emphasis that should be placed on controlling dust at the source (including housekeeping) versus installing engineering controls (e.g., protective features on dust collectors, silos, and other equipment). One expert said the costs associated with installing certain engineering controls are much less expensive than relying primarily on housekeeping for dust control (which can involve purchasing specialized vacuums and other classified equipment) and upgrading electrical classifications. In short, these experts suggested that the cost of mitigating primary deflagration hazards can be relatively small compared to the cost of managing fugitive dust.
4.3 Existing Facilities
Mr. Burt (OSHA) introduced the third discussion topic: how a new combustible dust standard should apply to existing facilities. Mr. Burt noted that some requirements of the grain handling facilities standard did not apply to existing facilities. Accordingly, he asked the experts: Should the combustible dust standard adopt a "grandfathering approach,"; or are some engineering controls important enough to warrant installing at existing facilities? As one example, OSHA must consider whether existing facilities should be required to retrofit their dust collection systems to be consistent with current consensus standards that were not available at the time the original facilities were constructed. Mr. Chibbaro (OSHA) added that a typical hierarchy of safety controls places engineering controls above administrative controls. However, in an explosion scenario, the hierarchy is modified so that controls that prevent an incident from occurring (engineering or administrative) are ranked above those that mitigate the consequences of an incident.
4.3.1 OSHA is concerned about the burden on employers if existing facilities must retroactively comply with the standard, especially the higher-cost engineering controls. Are there situations where engineering controls are not essential for existing facilities and, if so, how could they be defined in a standard?
To open this discussion, the experts first distinguished between two types of engineering controls. The first type includes preventive measures, such as avoidance and control of ignition sources, mechanical integrity, and bonding and grounding. Some experts said these engineering controls are generally well-understood, accepted with little resistance, and less costly to implement and maintain. The second type includes explosion protection measures (e.g., explosion isolation), and employers are often less convinced by the arguments for installing this second class of controls. For example, NFPA 484 requires all dust collectors to be located outdoors, but companies are reluctant to comply when they feel that their material has a low Kst or is only being collected in small quantities. Experts noted that the degree to which facilities implement engineering controls usually depends on the material and type of control.
When responding to this question, the experts had different opinions on whether OSHA should include a retroactivity clause in its combustible dust standard. A summary of the comments follows, starting with potential approaches that some experts recommended for grandfathering certain facilities and ending with reasons why several experts felt that OSHA's combustible dust standard should not exempt any facilities due to their age.
Several experts commented on a possible retroactivity clause for the combustible dust standard. One suggested that the standard take an "effectiveness approach"; to retrofitting, similar to the insurance industry. Insurers typically approach old properties by comparing the cost to correct a problem (e.g., installing a dust collector) with the cost of potential damage; and a typical guideline applied is that every dollar spent on improvements should protect against 10 dollars in damages. The expert felt that the combustible dust standard should grandfather certain situations because OSHA cannot expect facilities to spend 30 percent of their property value on upgrades and retrofits. Instead, existing properties should focus on administrative controls, and installation of new engineering controls should only be required during process upgrades. The expert admitted that defining an "effectiveness factor"; is more difficult for OSHA because it would require valuation of a human life, but he nonetheless encouraged OSHA to employ a cost-benefit approach when deciding whether a grandfathering clause is warranted.
Another expert cautioned that combustible dust hazards can be found at both new and old facilities. Thus, the expert recommended that any grandfathering provisions included in the combustible standard be accompanied by language informing owners of grandfathered facilities of potential hazards and options for voluntarily complying with requirements for existing facilities. This expert also recommended that any retroactivity clause not include facilities manufacturing products different from those made by the original occupants of the facility. For example, an employer that manufactures plastics at a facility that was originally constructed to manufacture metals should not qualify for the grandfathering exemption. Another expert supported this caveat and noted that management of change (MOC) provisions would be applicable, as in the PSM standard. This expert added that various elements of the PSM standard can be applied to a combustible dust standard, although he did not support incorporating combustible dusts into the PSM standard.
One expert noted that the retroactivity clause in NFPA 654 could serve as a model, whereby facilities are only required to meet requirements that were in place at the time of construction. The clause is primarily focused on engineering controls, which might prove technologically infeasible or financially prohibitive for facility retrofits. The standard has a caveat, however, that the authority having jurisdiction (AHJ) retains the right to require certain controls in spite of the retroactivity clause if significant risk exists. This expert further noted that OSHA did not account for the retroactivity clause when citing facilities under the NEP - a practice that the expert did not support. Another expert added that the current edition of NFPA 654 does require certain more easily implemented controls (e.g., ignition controls, bonding and grounding, housekeeping) to be applied retroactively, even at facilities that fall under the grandfather clause for engineering controls. Similarly, another expert noted that most administrative controls are usually applied retroactively (e.g., housekeeping, training, MOC, inspection and maintenance, incident investigation) because these administrative controls help sustain existing engineering controls and prevent them from deteriorating. Finally, another expert cautioned OSHA against assuming that all facilities were actually designed to comply with standards in place at the time; and one expert noted that eligibility for grandfathering could be based on an assessment of a facility's loss history and citation history.
One expert questioned why controlling ignition sources and fuel sources (e.g., dust accumulations) is viewed as inadequate protection and why employers might be compelled to implement additional explosion protection measures. The expert noted contradictions to this effect within the NFPA standards, whereby avoidance of ignition sources is recognized as sufficient for some processes, such as bag dumping, but inadequate for others. Another expert explained important differences between dust accumulations (which can take days or weeks to accumulate) and ignition sources (which can appear instantaneously). He identified many tricky and unexpected ignition sources, such as lightning, pyrophoric coals, or even a pigeon carrying a lit cigarette.
Some experts recommended that OSHA not include a global grandfathering clause in its combustible dust standard. One expert felt that a global grandfather clause implies that workers in old facilities are not valued as much as workers in new facilities. In addition, such a clause provides no incentive for facilities with outdated controls to upgrade to newer technologies. Another expert indicated that regulation must not provide a disincentive to install such upgrades. He said existing facilities should not receive a "blank check"; to continue operating as is, especially if most multi-fatality incidents occur at old facilities. Instead, some experts suggested alternative ways to ease the financial impacts of retrofitting requirements.
For example, one expert suggested phased applicability for retrofitting requirements based on the number of people exposed to combustible dust hazards. OSHA can require that a certain fraction of higher priority processes be retrofit over a short timeframe (e.g., two years), while other lower priority processes can have longer timeframes for compliance (e.g., 10 years). Such an approach would be useful at facilities that face significant capital investments for the required improvements. Alternatively, the expert suggested phasing in the standard based on facility size (with larger facilities regulated first), similar to how the Americans with Disabilities Act was implemented. Another expert suggested setting one effective date for retrofitting not too far in the future, but then having OSHA set internal priorities for enforcement based on risk. This expert believed that regardless of the approach that OSHA takes, the standard must mandate some type of engineering controls for existing facilities.
Another expert recommended that facilities conduct risk evaluations so that they address high priority hazards first. However, he also noted several challenges with a risk evaluation approach. First, risk evaluations are not easy for small entities because of a lack of trained staff. Second, most facilities do not have the full range of testing data needed to conduct a meaningful, quantitative risk evaluation. Without having the information needed to conduct thorough risk evaluations, many employers are aiming for subjective risk-reduction goals, such as "acceptable to the AHJ,"; which are difficult to comply with.
Anort ther expeadded that NFPA 654 and 664 currently include aspects of risk evaluation and that revisions in process for NFPA 61, 484, and 655 are adding risk evaluation components. The challenge that the NFPA committees are facing is determining the degree of risk evaluation to require, as not all facilities need the same level of detail in their risk assessments. This expert noted that risk assessment is valuable for showing facilities both where they do and do not have hazards. Another expert commented that AHJs often have no training or expertise with combustible dust risk-reduction measures. If the standard delegates any authority to AHJs, OSHA must ensure that these individuals have an adequate level of training to assess facilities' risk evaluations. This expert suggested a simple, stepwise approach to hazard assessment, similar to what facilities currently follow for permit-required confined space entry.
Another expert feared that employers without extensive knowledge of combustible dusts will have difficulty complying with risk assessment requirements because of the resources needed to complete them (e.g., hiring an engineer). As an alternate approach, the expert suggested that OSHA's combustible dust standard include prescriptive requirements that apply to all facilities and then follow with other risk-based recommendations. The standard should be written so that employers with limited experience with combustible dust will still be able to implement prescriptive components.
Another expert suggested that OSHA's standard include a list of equipment known to cause dust explosions (e.g., mechanical impact mills, spray driers) and require hazard assessment for those specific pieces of equipment. Another expert listed options for how to implement this prioritization: OSHA could mandate the equipment prioritization in the combustible dust standard; OSHA could focus on priority equipment during enforcement; or employers could be required or encouraged to conduct their own prioritization. Another option presented was for OSHA to establish industry partnerships and coordinate with trade associations to develop industry-specific templates for prioritization, similar to the industry-specific risk assessments included in the EPA Risk Management Plan regulation. One expert added that employees and their representatives should also be represented in such partnerships. Another expert remarked that OSHA could focus inspections based on its own knowledge of incident history.
Before concluding discussions on retroactivity, Mr. Burt (OSHA) asked the experts to give more specific examples of situations that definitely require engineering controls, regardless of the facility age. One expert voiced concern about facilities using a single dust collection system to control dusts from "high risk"; operations (e.g., hammer mills) as well as "low risk"; operations (e.g., fugitive dust from a hand-dumping area); the expert characterized this type of dust control as "totally unacceptable."; Another expert noted that in multi-plant facilities, combustible dust problems at one facility should trigger inspections at the other plants. One expert remarked that OSHA should prioritize hazards based on the number of people at risk. For example, an unprotected dust collector in a parking lot behind the building is a lot less risky than having it in the middle of a plant. Another expert added that assessing the proximity of the working staff to hazardous equipment (e.g., bucket elevator, hammer mill) is an important consideration when addressing combustible dust hazards. One expert endorsed a performance-based approach, noting that several NFPA standards outline objectives for life safety protection, mission continuity, and structural integrity. Risk assessment should consider the proximity of workers to the hazard, impediments to egress, and how likely workers are to escape. Another expert added that the NFPA standards have requirements for peer review, which helps ensure that risk assessments are done well. One expert noted that a facility with both gas and dust explosion hazards is more problematic than a dust hazard alone, and that external factors (e.g., vulnerability to earthquakes) should also be taken into consideration.
4.3.2 Data available to OSHA indicates widespread non-compliance with engineering control provisions of NFPA standards. Has compliance improved in the last few years as a result of increased hazard awareness and government enforcement efforts? If engineering controls were not mandated, how likely are they to be installed voluntarily, and in what situations?
One expert noted that most facilities do not follow the NFPA standards at all or do so to a minimal extent. As an example, he noted that many small facilities were designed by a mechanic who might have limited or no awareness of NFPA standards or combustible dust hazards. This situation is exacerbated by weak enforcement at the state and local level; many AHJs are also unfamiliar with applicable consensus standards and codes and are therefore unable to recognize hazards.
One expert remarked, based on experiences at his company, that compliance has apparently improved with increased awareness of combustible dust hazards, but that awareness and support must extend from operators to management. This expert was skeptical that facilities would install engineering controls voluntarily, except after explosions occur.
Another expert commented that the OSHA combustible dust NEP triggered enormous interest in bringing facilities into compliance with current NFPA standards. Most of his clients would not have done so had it not been for concern for inspections and enforcement. Another expert described an employer who added a job for routine housekeeping, verification of bonding and grounding, and evaluation of other dust control measures as a result of the NEP.
4.4 Multiple Layers of Protection
Mr. Baird (Office of the Solicitor) introduced the fourth topic of discussion: the use of multiple layers of protection to address combustible dust hazards. Mr. Baird first used the analogy of multiple safety measures included in vehicle design to protect occupants in cars: drivers are tested before they are allowed on the road, but because accidents still occur, cars are equipped with seat belts, airbags, antilock brakes, and other features to mitigate the effects of certain, known hazards. Mr. Baird asked the experts to consider the extent to which multiple layers of protection might be necessary in OSHA's combustible dust standard, keeping in mind the concerns of small business, cost effectiveness, and employee protection.
4.4.1 Would it be appropriate for OSHA to require a single layer of protection against dust explosions – for example, housekeeping without ignition controls or explosion mitigation features?
All experts who addressed the topic stated that a single layer of protection is inadequate to protect against dust explosions. Several experts articulated different reasons why multiple layers of protection are important.
One expert noted that a number of elements must come together to create an explosion hazard: oxygen, fuel, confinement, dispersion, and ignition. Thus, the question is how effectively a facility can eliminate at least one of the five elements. For instance, removing ignition sources is one layer of protection. This should significantly decrease the frequency of events, but is unlikely to be completely effective due to the random nature of some ignition sources. In addition, this type of protection will not reduce the consequences of an event should one occur. Thus, rather than focusing on one type of control, this expert recommended implementing a combination of controls. Facilities should keep adding layers of protection, he said, until they reach an acceptable level of risk and an acceptable level of consequences. He supported a combustible dust standard that would start by making sure employers and workers understand combustible dust hazards, then require certain administrative controls, and finally move on to engineering controls, starting with those that are inexpensive to implement and continuing with increasingly costly controls. Each facility should layer these controls until they reach an acceptable level of risk. This expert concluded by saying OSHA's standard need not require multiple layers of protection; rather, it should focus on having facilities meet the objectives of the standard (e.g., achieving an acceptable level of risk, preventing an explosion that kills a predetermined number of people).
Another expert had a different perspective on why multiple layers of protection should be required. This expert noted that all protection features or strategies have a finite reliability. For example, a housekeeping worker might fail to remove dust accumulations on a given day, or a deflagration suppression system could develop an unnoticed leak and lose effectiveness. Because of potential failures in individual protective measures, multiple protective systems are necessitated. The NFPA standards also operate on this premise. Another expert commented further, suggesting that OSHA refer to the chemical and petroleum industries' "layer of protection analysis,"; which is a technique for evaluating the reliability of the layers and determining the number of layers required to lower risk to tolerable levels. This type of analysis reinforces the finite probability of failure of each layer of protection and the importance of ensuring that the weaknesses of each layer do not align to form a path to disaster. This participant felt that although one layer of protection should be an effort to eliminate ignition sources, it should not be the only layer. The NFPA standards, he noted, typically do not accept the presumed absence of ignition sources as the sole layer of protection. Eliminating every possible ignition source in advance is nearly impossible, as evidenced by the difficulty that inspectors face in identifying ignition sources during incident investigations.
Another expert used Swiss cheese as an analogy for the failure model: each layer of cheese has holes in it, some big and some small, but when all of the slices line up none of the holes should extend all the way through. The expert noted that there is no single protective measure that will prevent combustible dust incidents at all facilities. Instead, facilities need to use a combination of protective layers that provide an acceptable level of risk. This expert reiterated that while control of ignition sources should be an element of every model and is an easy way to reduce the overall risk of an event, it does not reduce the hazard (i.e., consequences).
Two other experts provided additional comments. First, one expert noted that employees face many competing pressures, particularly production versus safety, and that given this situation, housekeeping alone is an inadequate level of protection. Second, an expert distinguished between prevention and protection. He noted that prevention includes safety controls like temperature monitoring and grounding and bonding, whereas protection covers venting, suppressing, total containment, and inerting. This expert suggested that having only protective systems in the absence of preventive measures would be acceptable because workers would still be safe in the event of an explosion, but the expert did not recommend that approach.
Mr. Baird (Office of the Solicitor) followed up by asking the experts how employers will know when they have reached an "acceptable level of risk."; One expert responded by indicating that this has been an issue with NFPA 654; that consensus standard requires employers to conduct process hazard analyses but does not explicitly define acceptable levels of risk. Another expert noted that process safety information and material-specific properties (e.g., explosibility, ignitability) should be used during hazard assessment and might help employers determine how many layers of protection are needed. For example, certain types of grounding might not be necessary for dusts of high MIE, whereas other dusts would warrant the use of such controls. Another expert remarked that having an independent second opinion evaluate the hazard assessment can increase confidence that a process has been made "safe enough."; The expert noted that facilities should never rely on one person's opinion, especially not if that person is responsible for production.
Mr. Burt (OSHA) followed with two more questions. First, do the experts know what percentage of fatalities is prevented by each type of control? Second, what are the failure rates for each type of control? The experts responded with a discussion of human reliability and the reliability of engineering controls.
Some experts felt that humans are less reliable than engineering controls. One expert noted that very often an employee is the single layer of protection between safe operation and catastrophe, and he suggested that any controls relying entirely on human responses will eventually fail. Thus, if OSHA's standard focuses only on housekeeping, then incidents will continue to occur. The standard, he argued, should instead require multiple controls including, at its core, basic process control systems and equipment design. Another expert was less pessimistic about the probability of human failure and noted that there are ways of estimating the likelihood of human error considering the worker's training, the stress level of the situation, and other factors. This expert felt that under most normal circumstances, a properly trained and motivated employee should be successful at implementing most administrative controls. Another expert added that sometimes incidents occur when the errors of multiple individuals combine, so higher order probabilities might be involved. For example, an explosion involving plastic dusts at a facility in Kentucky was caused when one individual opened the door of a malfunctioning oven to help regulate the temperature while other workers were performing a dust blow-down; this combination of practices initiated the event. This expert generally felt that human-controlled processes are more likely to break down. One expert commented on human reliability by noting that investigations that stop at the level of the employee have not gone deep enough; investigations should instead determine the system-level failures responsible for the employee error (e.g., were training programs inadequate?).
In terms of the reliability of engineering controls, several experts noted that manufacturers of certain systems (e.g., explosion suppression, relief venting) have published probabilities of failure. One expert noted that the fire alarm industry has quantified reliability data for many products. However, this expert noted that incident investigations usually show that failures result from lack of maintenance or inappropriate design rather than equipment failure. In other words, many incidents could have been prevented by effective inspection and maintenance programs and are not due to inherently unreliable engineering controls. Thus, this expert felt that management must commit to running a safe workplace and lowering risk to the lowest achievable level, rather than relying entirely on technology to reduce incidents. Another expert questioned the relevance of quantifying failure rates, seeing that many small businesses potentially subject to OSHA's standard are likely not going to do so. The expert noted that quantifying failure rates is a sophisticated analysis that even larger chemical companies struggle with. Another expert remarked that an underlying problem of calculating reliability is that, even if it is possible to narrow down the probability of failure of a given layer, the calculations still require an assumption on the probability of the ignition event, and that probability is typically difficult to quantify.
Other experts commented on other layers of protection that the standard might require:
- One expert remarked that work practice controls are another, often less expensive type of control. For example, a facility can switch from bag dumping of powder material to a safer mode of transferring material.
- Another expert commented that personal protective equipment (PPE) is another layer of protection that OSHA should consider in the standard. The type of protective clothing required for employees handling combustible dust is ultimately determined by the hazards of the job duties. However, another expert added that use of PPE should not be the primary means by which employees are protected from combustible dust hazards. Further, if PPE is incorporated into OSHA's standard, the expert said it must be provided at no cost to employees. One expert noted that NFPA 2113, Standard on Selection, Care, Use, and Maintenance of Flame-Resistant Garments for Protection of Industrial Personnel against Flash Fire, includes information on 1) testing and certification of garments and 2) determining when and where protective clothing should be used. This standard is now being referenced by NFPA's combustible dust standards.
- One expert emphasized the need for training and education to ensure that all controls work effectively. He described a situation where workers transferring dry powdered chemicals to "super-sacks"; were instructed to attach a clip onto the bag's bonding wire to eliminate the electrostatic hazard. In one case the worker attached the clip around the rubber insulation of the wire instead of to the copper itself, thus preventing the electrostatic control from functioning. This might not have occurred if the worker had a better understanding of how the bonding wires worked.
- Two experts commented on management of change (MOC). One expert remarked that one of his clients had little success implementing MOC, in part because the purchasing department would alter engineers' requests (e.g., to an after-market part) in order to save money. This expert felt that enforcing MOC would be difficult for OSHA but that it is an important administrative control. Another expert described how he encourages facilities to implement MOC programs; wherever this expert installs an explosion protection or suppression system, he adds labels indicating that the process equipment has an explosion hazard and that MOC must be applied.
- One expert recommended that OSHA's standard mandate employee involvement in all aspects of combustible dust safety, including program planning, hazard identification and inspection, MOC, monitoring and enforcement, abatement activities, training and re-training (after a problem is identified), incident investigation, and emergency response. He and another expert said OSHA's standard should include an "anti-retaliation clause"; to protect employees who report hazards, injuries, and illnesses.
Ms. Edens (OSHA) asked the experts for recommendations on how best to get management commitment to combustible dust safety programs. One expert commented that he initially tries to educate his clients on the hazards and help them understand how it affects their employees and their business. If employers understand the hazards, then they typically do not need to be convinced to provide the layers of protection. Otherwise, the threat of fines, regulatory enforcement, and increased insurance premiums might also coax employers. Another expert added that part of the problem is a lack of proper understanding of the hazards and that training will help. A third expert emphasized the importance of management commitment to safety, noting that this attitude will "trickle down"; to different tiers of employees. Similarly, a lack of commitment to safety from management will set a poor example for employees.
4.4.2 OSHA's current standards include controls for certain ignition sources, including electrical equipment, powered industrial trucks, and welding. Would it be necessary for employee protection to require controls, in addition to housekeeping, for ignition sources such as static electricity, friction, sparks, hot surfaces, open flames, or smoking?
The experts commented on ignition controls in the context of providing multiple layers of protection (see Section 4.4.1 above).
4.4.3 If engineering controls were not mandated, what layers of protection would be appropriate?
One expert rephrased this question as: "In an existing facility, can you get an acceptable level of risk with administrative controls alone?"; This expert noted that it is a critical question because retrofitting existing facilities with required engineering controls can be difficult and costly. This expert felt that risk assessment plays a key role in answering this question.
Another expert noted that many existing facilities simply cannot be retrofitted to comply with prescriptive engineering requirements in the current NFPA standards. For example, a silo might not be structurally strong enough to have deflagration vents installed. However, the expert remarked that taking a performance-based alternative design approach can come close to achieving the same level of safety. Such an approach, taken intentionally by an informed professional, can help existing facilities achieve the maximum level of safety, given the limitations of facilities' current configuration and construction. This expert felt that OSHA's standard must include a performance-based approach if the standard is to be applied retroactively to existing facilities. NFPA 654 can serve as a roadmap for engineering considerations and related requirements, such as peer review, documentation, and analytical methods.
4.4.4 In your expert opinion, what should be the hierarchy for protection for combustible dust hazards (dust control, ignition control, explosion mitigation)?
One expert commented that the NFPA standards approach the hierarchy of controls in generally the same order as listed by OSHA. Controlling the fuel source first and then ignition sources is very cost-effective and limits damage should an event occur.
Another expert remarked that the hierarchy of controls differs for primary and secondary explosions. In the case of primary explosions, dust control is not appropriate because often the purpose of the process vessel is to contain a dust cloud (e.g., dust collector, hammer mill). Rather, explosion protection systems (e.g., venting) are warranted. In the case of open vessels, PPE might be appropriate for nearby operators, as well as ignition source control to reduce explosion risk. For secondary dust explosions, dust control should be the first priority, followed by ignition control, and lastly, explosion and flash fire mitigation.
5 Concluding Remarks
Ms. Edens (OSHA) concluded the forum by thanking the experts for their time and participation. She noted that the meeting had been very informative for all involved. Ms. Edens remarked that the next step in the rulemaking process is the upcoming SBREFA panel, although the date for that has not been set. In the meantime, OSHA will review the input provided by the experts and post a summary report for the export forum on the agency's website (www.osha.gov) and notify participants by email when that occurs. Lastly, Ms. Edens remarked that because OSHA's combustible dust standard is still in the early stages of development, all stakeholders will have more opportunities to provide input in the future.
1 Following the meeting, the expert provided OSHA with an additional document clarifying the handout on the dynamics of a dust flame. This additional document is also included in Appendix C, although it was not distributed at the forum.
2 Refer to Factory Mutual's Global Data Sheet 7-76: Prevention and Mitigation of Combustible Dust Explosion and Fire. March, 2009.
Appendix A. Biographies of Invited Experts
Note: The biographies in this appendix were provided by the invited experts. They are included here without revision.
John M. Cholin, P.E., FSFPE, M.E.E.
Mr. John M. Cholin, PE, is President of J.M.Cholin Consultants, Inc. (JMCC), a fire protection consulting and engineering firm specializing in industrial fire protection strategies. Mr. Cholin is a Licensed Professional Engineer in the discipline of Fire Protection Engineering.
Over the past 20 years his consulting practice has become dominated by combustible dust explosion hazards and the management of them. JMCC serves clients in the combustible metals, forest products, paper, food products, pharmaceutical, fossil fuel and chemical industries.
He is a member of:
- NFPA
- Fellow of the SFPE
- NSPE
- Technical Committee on Initiating Devices for the National Fire Alarm Code (NFPA 72),
- Technical Committee on the Fundamentals of Dust Explosion Prevention and Control (NFPA 650, 654, 655) and
- Technical Committee on Wood, Paper and Cellulosic Dusts (NFPA 664).
He has authored four chapters for the 18th, 19th, and 20th Editions of the NFPA Fire Protection Handbook. He has authored commentary for the each of the National Fire Alarm Code Handbooks, from 1993 through 2010 editions. He also serves as a seminar instructor for both NFPA and SFPE.
Guy Colonna
Guy Colonna is the Division Manager, managing the Industrial and Chemical Engineering department for the National Fire Protection Association. He has been with NFPA for 25 years and holds engineering degrees from the US Coast Guard Academy and Stanford University. He is also a registered professional engineer in chemical engineering in Massachusetts.
His responsibilities at NFPA include management of the Marine Chemist Training and Certification Program and NFPA activities dealing with marine fire protection. He also serves as Staff Liaison to committees dealing with safeguards at dust hazard process locations, explosives, industrial fire brigades, explosion protection systems including venting of deflagrations, and pyrotechnics and special effects.
He developed and instructs NFPA's confined space safety training courses offered to both the maritime and general industry and combustible dust and explosion protection seminars. He has previously served as the Executive Secretary to the Industrial Fire Protection Section of the NFPA. He has served on Department of Transportation and Department of Labor-OSHA advisory committees representing NFPA.
Before starting work with NFPA, Guy served as an officer in the US Coast Guard. His assignments include service aboard ship, in research and development and in the Coast Guard's Eighth District (Gulf Coast). He developed a service-wide confined space safety program and an occupational safety and health program for Coast Guard marine safety personnel in the Eighth District.
He is the author of technical papers and presentations on confined space safe practices, hot work safe practices, chemical hazard identification and classification, combustible dusts fire and explosion hazard protection, and pyrotechnics and special effects.
He is a member of the American Institute of Chemical Engineers, American Chemical Society, Society of Fire Protection Engineers, and American Society of Safety Engineers.
Dr. Vahid Ebadat Ph.D., M.Inst.P, MIEE, C.Eng., C.Phys
Dr. Vahid Ebadat Ph.D., M.Inst.P, MIEE, C.Eng., C.Phys. is the CEO of Chilworth North America. He has worked extensively as a process and operational hazards consultant for the chemical, pharmaceutical and food industries. Dr. Ebadat is a regular speaker at training courses on gas and vapor flammability, dust explosions, and controlling electrostatic hazards. He is a member of NFPA 77 Technical Committee on Static Electricity, NFPA 654 Standard for the Prevention of Fire and Dust Explosions from the Manufacturing, Processing, and Handling of Combustible Particular Solids and ASTM E27 Committee on Hazard Potential of Chemicals. Dr. Ebadat's research has culminated in the publication of numerous technical articles and papers.
Henry L. Febo, Jr., PE
Henry L. Febo, Jr., PE is Assistant Vice President and Senior Engineering Technical Specialist in the Engineering Standards Division at FM Global. He has worked in the Division for the past 20 years where he has been responsible for developing numerous loss prevention engineering standards that are used by the field engineering staff at FMGlobal. His areas of expertise include the hazards of flammable liquids and gases, combustible dusts and reactive chemicals, safety-instrumented systems, venting of reactive systems, chemical plant protection and Process Safety Management. His duties also include visits to insured clients to provide loss prevention advice on specific problems, responding to questions from the field engineering staff, training of field staff and customers.
Prior to joining to Engineering Standards Division, he was in the field engineering organization at FM Global for 19 years. He has supervised other loss prevention engineers and provided loss prevention engineering advice to insured clients of all types with emphasis on chemical and other high hazard potential processes and occupancies.
Mr. Febo has degrees in Chemical Engineering from Drexel University (BS) and New York University (ME) and is a registered Professional Engineer.
Mr. Febo is a member of the NFPA Hazardous Chemicals Committee; Committee on Handling and Conveying of Dusts, Vapors, and Gases and the Explosion Protection Committee, each for about 15 years. He has been a member of the AIChE Safety and Health Division as well as the AIChE DIERS Users Group for almost 30 years. He has presented papers at the Safety and Health Division's annual Loss Prevention Symposium as well as for other technical organizations and has been published in several technical publications and is a chapter author of the NFPA Fire Protection Handbook.
Walter L. Frank, PE
Walter L. Frank, PE, President, Frank Risk Solutions, Inc.
Mr. Frank has more than 38 years of experience in the chemical process industries, with the last 24 years as a risk, reliability, and safety consultant. He spent 24 years with DuPont where he held assignments in the areas of plant technical support, manufacturing supervision, research and development, design, project start-up, and process safety consulting. His last ten years with DuPont were in the Process Safety and Fire Protection group in the DuPont Engineering Services Division, specializing in explosion hazards evaluation and control. After DuPont, he was a process safety consultant with ABS Consulting for ten years, leaving to form Frank Risk Solutions in 2007.
In addition to his work in explosion hazards evaluation and control, Mr. Frank provides support to industry in the areas of process safety management system application and enhancement, auditing, regulatory compliance, and safety culture evaluation and growth. Mr. Frank has co-authored four books on process safety topics for the American Institute of Chemical Engineers (AIChE), Center for Chemical Process Safety (CCPS), and was a contributing author for the process safety section of the new edition of Perry's Chemical Engineer's Handbook.
Mr. Frank received a B.S. degree in Chemical Engineering from Rose-Hulman Institute of Technology in 1973. He is a registered Professional Engineer in the state of Delaware and is both an AIChE Fellow and a CCPS Fellow. He is an NFPA member and chairs the Technical Committee on Handling and Conveying of Dusts, Vapors, and Gases.
Recent relevant work experience includes dust explosion hazard evaluations for the wood products, semiconductor silicon, paper products, defense, and recycling industries. He is currently chairing a significant revision of NFPA 654, Standard for the Prevention of Fire and Dust Explosions from the Manufacturing, Processing, and Handling of Combustible Particulate Solids.
C. W. Kauffman
C. W. Kauffman is a Professor of Aerospace Engineering at the University of Michigan where he specializes in gas dynamics and propulsion. Since junior high school when he discovered that he could propel cone top beer cans containing several stones of carbide and several drops of water over his house roof he has been interested in explosions. The research of his undergraduate advisor which employed shock tubes was of great interest leading to an early industry position where the task was to determine the cause of malfunctions during ICBM test flights.
His PhD research at Michigan, funded by NASA, concerned combustion instabilities or two phase detonations which were occurring in the Rocketdyne F-1 engine to be employed on the Saturn V rocket. These results were applied to develop fuel air explosives, FAE, for military purposes. This was, however, related very closely to the heterogenous dust explosions which occurred in coal mines and grain elevators where a rigorous program of investigations and legislation basically eliminated this industrial hazard. As the Soviets were well known for their explosion expertise contacts were initiated nearly forty years ago leading to numerous technical interactions, visits, and even residence in the Russian Federation where the technical opportunities grew to include the various aspects of flight and flight vehicles. This combination of explosions and aviation resulted in his being the first runner up for the 1984 vacancy on the National Transportation Safety Board, a frequent press source for aviation disasters, and being selected for Federal Aviation Administration work to prevent fuel vapor explosions aboard aircraft.
In the 2004-2005 academic year he reinstituted a two semester course concerning explosions, explosives, propellants, and pyrotechnics at the request of the students resulting from the beginning of the Iraq war. Most recently he has been engaged in a national effort in order to prevent foreign students and scholars from looting American industrial and military information which is then used by their home countries to threaten America's security.
Arthur (Art) Mattos
Arthur (Art) Mattos - VP – Global Asset Protection Services, LLC
Principal Consultant - Matthews, NC, USA
Education: BS, Mechanical Engineering, University of Rhode Island - 1980
Experience: 29 years of loss prevention experience
Designations: CFPS (Certified fire Protection Specialist)
Professional Memberships: NFPA (National Fire Protection Association), SFPE (Society of Fire Protection Engineers)
Art graduated from the University of Rhode Island in December, 1980, with a BS in Mechanical Engineering and Applied Mechanics, and began his career with Industrial Risk Insurers (IRI) in January, 1981 as a located Field Engineer in Hickory, NC. Since then, he has served in numerous roles within IRI and Global Asset Protection Services (GAPS), including Supervisor - District Loss Prevention, Loss Prevention Account Consultant, Senior Loss Prevention Account Consultant, and VP - Principal Consultant. As VP - Principal Consultant, Art manages the loss prevention servicing activity and provides risk management solutions to a diversified group of GAPS Clients, including chemical, food processing, healthcare, hospitality, metalworking, packaging, plastics, printing, pulp & paper,retail, textiles, warehousing, and woodworking.
Art is a Member of the National Fire Protection Association (NFPA), the Society of Fire Protection Engineers (SFPE), and is a Certified Fire Protection Specialist (CFPS). He serves as Chair of the NFPA Technical Committee for Wood and Cellulosic Materials Processing (NFPA 664). He is also active in the Carolinas and Greater Atlanta Chapters of SFPE, and has served in several leadership positions, including Carolinas Chapter President, Co-Editor of "The Spark"; newsletter, and Chair of the Carolinas Chapter's Technical Seminar Committee.
George Petino Jr., MME, P.E.
George Petino, Jr., MME, P.E.
President, Hazards Recognition Corp.
Dust Explosion Consultant
Active in engineering research for more than forty-nine years, Mr. Petino has been an engineer at Hazards Research Corporation since 1971. He is principal consultant in dust explosion hazards risk evaluation, dust explosion incident investigation, educational seminars, characterization of electrostatic phenomena and design of explosion venting and grounding systems. He holds a BSME from Fairleigh Dickinson University and an MME from Stevens Institute of Technology. He is a Licensed Professional Engineer in New Jersey and Nevada.
Shortly after joining Hazards Research Corporation in 1971, Mr. Petino performed a hazards analysis of equipment and procedures for continuous manufacture of Composition B from TNT and RDX for Holsten Defense Corporation. He subsequently performed an extensive series of programs for the Department of Defense related to Detonability of explosives processing mixtures and safety of metering and handling equipment for sensitive explosives.
Since 1978, Mr. Petino has concentrated his activities in the area of dust explosion hazards evaluation, performing major studies on utility plants, refuse-derived fuel and sludge-drying facilities, in addition to extensive work in conventional commercial process plants in the food, chemical, pharmaceutical and plastic industries. Beginning in 1981, he has provided on-site services throughout the United States, Canada, Mexico, South America, Europe and Australia for one of the largest chocolate manufacturers in the world. For the last thirty-one years, this client has retained him as their expert responsible for all dust explosion risk evaluations in North and South America. During this time period, he developed their dust explosion hazards asset conservation standards before comparable standards such as ATEX and NFPA were published. In Europe, the passage of ATEX did not cause any expenditure of capital in order for this corporation's plants to be in compliance. Mr. Petino is currently responsible for the mitigation of dust explosions risks in fifty-six confectionery, rice and petfood factories.
Mr. Petino has been retained by OSHA to investigate dust explosion incidents. A paper co-authored by Mr. Petino has been selected by the Office of Science and Technology Assessment (OSTA) to be used as a guideline for the safe handling or processing of biosolids-derived fuel. Presently, there are no OSHA regulations addressing this hazard.
Ali S. Rangwala
Ali S. Rangwala is an assistant professor at the department of fire protection engineering at Worcester Polytechnic Institute (WPI) (2006 – present). He has a BS in Electrical Engineering, from the Government College of Engineering, Pune, India (2000), an MS in Fire Protection Engineering from the University of Maryland, College Park (2002), and a PhD in Mechanical and Aerospace Engineering from the University of California, San Diego (2006).
Professor Rangwala's current research interests include, deflagration of combustible dust clouds, ignition behavior of combustible dust layers, in-situ burning of oil on broken ice, velocity measuring techniques in fire induced flows, and flame propagation and burning rate behavior of condensed fuel surfaces. He has his own research laboratory (1500 square feet) at WPI, and is currently advising 4 funded graduate students. In the last few years, he has published over 10 journal articles and has presented in over 20 conferences. He has papers in journals such as Journal of Hazardous Materials, Combustion and Flame, Combustion Theory and Modeling, Fire Safety Journal and Fire Technology. He teaches three graduate courses: Explosion Protection, Industrial Fire Protection, and Combustion at Worcester Polytechnic Institute, Department of Fire Protection Engineering.
Robyn Robbins, B.A., C.I.H.
Robyn Robbins, B.A., C.I.H.
Assistant Director, Occupational Safety and Health Office, UFCW International Union. She has been with the UFCW since 1996.
EDUCATION/TRAINING
Johns Hopkins Univ., Baltimore MD 1972-76 B.A. Natural Sciences
Univ. of Illinois, School of Public Health, Chicago 1978-81 Industrial Hygiene (M.S. Program)
Past Positions and Employment
1981 – 1986 Food and Allied Service Trades Dept., AFL-CIO, Washington D.C. Safety and Health Specialist
1986 – 1991 Maryland Occupational Safety and Health Agency, Baltimore, MD, Industrial Hygienist/Compliance Officer
1991-1996 George Meany Center for Labor Studies, National Labor College, Silver Spring MD, Industrial Hygienist, Labor Educator, NIEHS Railroad Workers Hazardous Materials Training Program
Professional Affiliations
Member, American Industrial Hygiene Association
Member, American Board of Industrial Hygiene
Member, American Public Health Association
Certification
Certified in the comprehensive practice of industrial hygiene, American Board of Industrial Hygiene, 1992. Recertified 1998, 2004, 2009
Member: American National Standards Institute, Z10, Accredited Standards Committee, Safety and Health Management Systems Standard, 2001-2003, 2005 to current. Revision of standard.
Steve Sallman
Steve Sallman is a Technician of the United Steelworkers - Health, Safety & Environment Department at the International Headquarters in Pittsburgh, Pennsylvania.
Steve's employment history includes spending four years at the Iowa Division of Labor – OSHA, in the Consultation & Education Bureau as a Safety & Health Consultant. Prior to this, he worked at the Firestone Tire & Rubber Plant for 13 years where he served Local Union #310 as a full-time Health, Safety & Environment representative for 8 years.
Some of Steve's current duties include, providing assistance to the membership of the USW by conducting workplace health, safety & environment (HSE) audits and investigations at USW represented facilities. He leads HSE negotiations with various employers, works with government representatives and other organizations and finally, coordinates HSE conferences for the members of the union.
Tom Scherpa
Tom Scherpa is a Consulting Engineer with the DuPont Engineering Technology (DuET) Process Safety and Fire Protection Group. He has 9 years of experience in the DuET PSFP group, with a focus on dust explosion hazards. Prior to joining DuPont, Tom worked as a laboratory technician in the dust explosion testing lab at FM Global. He has a B.S. degree in chemical engineering and a master's degree in fire protection engineering, both from Worcester Polytechnic Institute (WPI). The subject of his master's thesis was dust entrainment by a blast wave, which can contribute to secondary dust explosions. He has been a member of the NFPA Technical Committee on Handling and Conveying of Dusts, Vapors, and Gases (HAP-AAA) since 2006.
Jeffrey Wanko, P.E., C.S.P.
Jeffrey Wanko, P.E., C.S.P. – Investigator, US Chemical Safety Board. Mr. Wanko received a Bachelor's Degree in Chemical Engineering from Syracuse University in 1989 and a Master's of Environmental Engineering from the Illinois Institute of Technology in 1999. He served 2 years as a Peace Corps volunteer in the African Nation of Lesotho as a high school teacher and water engineer.
Mr. Wanko has been an environmental, health, and safety professional for 18 years specializing in process safety for the pharmaceutical, specialty chemical, and food sectors. He serves on NFPA technical committees for combustible dusts and flammable liquids.
Mr. Wanko is a Professional Engineer licensed in the States of Illinois and New Jersey. In addition, he is a Certified Safety Professional.
He led the team for Chemical Safety Board's investigation into the fatal propane explosion in Ghent, West Virginia in which 4 were killed and 5 seriously injured. In 2008, he led the investigation team on the Indspec incident in Petrolia, Pennsylvania that involved a large release of oleum and subsequent evacuation of three communities. He is currently the lead investigator for the incident in Bayamon, Puerto Rico, in which an explosion occurred following overfill of a 5,000,000-gallon gasoline storage tank and the AL Solutions incident in New Cumberland, West Virginia in which three were killed in a titanium and zirconium metal dust flash fire.
Bob Zalosh
Bob Zalosh is a Worcester Polytechnic Institute (WPI) Professor Emeritus and runs a consulting organization entitled Firexplo. Bob was a WPI Professor of Fire Protection Engineering from 1990 to 2006. Prior to that, Bob held various positions conducting and managing fire and explosion research at Factory Mutual Research Corporation (one of the predecessors of FM Global) over a 15 year period, culminating as Assistant Vice President and Manager of the Applied Research Department.
Bob's consulting activities have included conducting combustible dust hazard and risk assessments for a variety of industrial facilities. He has conducted numerous dust fire and explosion incident investigations, and has advised OSHA and private clients on the development and review of settlement agreements resulting from citations issued after Combustible Dust National Emphasis Program inspections.
Bob is the author of a textbook entitled Industrial Fire Protection Engineering and co-authored the Center for Chemical Process Safety's Guidelines for Safe Handling of Powders and Bulk Solids. He also is the author of the chapter on Explosions in the NFPA Handbook (19th and 20th Editions) and the chapter on Explosion Protection in The SFPE Handbook on Fire Protection Engineering (all editions). He is a member of the NFPA Explosion Protection and Combustible Metals Committees and several advisory panels dealing with fire and explosion hazards.
Appendix B. Information Provided by OSHA to Invited Experts
Background
The information available to the Agency indicates that an average of 7 fatalities and 35 injuries per year resulted from combustible dust incidents (fires and explosions) between 1999 and 2010. The number of fatalities and injuries vary widely from year to year, and OSHA believes these data may substantially undercount injuries, because incidents with only one or two injuries are much less likely to be reported widely or investigated by OSHA or CSB than those involving fatalities.1 Fatalities may also be undercounted because we have no way of being sure that we have found data on every incident, and have discovered fatality incidents not in our original data base.
Analysis of the results of the National Emphasis Plan and interviews with Compliance Officers across the country make it clear that controls to address the hazard of combustible dust are significantly lacking. Widespread non-compliance with OSHA and NFPA standards exists. This parallels the findings of the Chemical Safety Board (CSB) in its 25-year combustible dust study, which indicated widespread noncompliance with the NFPA standards that are mandated by most State and local building and fire codes.
Following the NFPA approach, most facilities will need to test the dust they generate and perform risk assessments of their combustible dust hazards. Many facilities will need to make additional investments in combustible dust control technologies. They will also need to develop a combustible dust program that will incur expenses to develop and use appropriate housekeeping procedures and ignition control measures, and other program elements.
NFPA standards are partially performance-based, in which a hazard analysis drives the controls used to abate the hazard. They also contain an option to comply with the entire standard on a performance basis. A performance-oriented, hazard analysis-driven standard gives employers great flexibility in abating hazards. This is helpful for a comprehensive standard that covers such a wide array of facilities, processes, and materials.
By contrast, OSHA's grain handling facilities standard covers a portion of a single industry with a relatively similar, and limited, range of dust types. In promulgating such a narrowly-focused rule, the Agency was able to use a more specification-based approach. Included are specific requirements for dust collectors, grain dryers, and inside bucket elevators, and specific housekeeping requirements for areas near inside bucket elevators, grinders, and grain dryers. OSHA conducted a review of the Grain Handling Facilities standard in 2003, concluding that it should continue without major change because fatalities had decreased significantly without negative economic impact.
Given the wide breadth of potential dusts and processes that might be covered by an OSHA standard and the potential impact on small facilities, OSHA believes that it will be especially helpful in preparing to convene a Small Business Regulatory Enforcement Fairness Act (SBREFA) panel to examine in depth all possible approaches the Agency can take to formulate a comprehensive combustible standard. In general, it can be specification-oriented or performance-oriented. It can address all industries in a general manner, or could be industry-specific and detailed, in which case the Agency would need to gather detailed data on every specific industry. All industries could be included, or those with a relatively low risk could be exempted if a suitable risk metric could be established. Similarly, certain low-explosive materials could be exempted if an appropriate threshold could be established. Finally, OSHA could focus on preventing the most catastrophic events that nearly always involve secondary explosions.
The forum will convene experts in the field to gather information on protective and cost-effective regulatory options. The experts include representatives of a broad spectrum of industries, academia, research, underwriters, government, and employee representatives. The attached list of participants will be expanded to approximately 15 experts.
Discussion Issues
OSHA is convening this meeting to bring together experts in the field of combustible dust to discuss approaches that would both protect employees and be cost-effective for employers. OSHA does not seek consensus but rather a frank discussion of the panel members' individual expert opinions.
Please do not assume that the issues listed below would be the only components of a prospective standard; rather, these are the specific issues for which OSHA has invited experts to provide input. Other components of a prospective standard that the Agency is considering, but for which OSHA does not need input at this time, include employee participation, inspection, testing, maintenance, repair, management of change, investigation, emergency planning, and training.
No written comments or prepared remarks are needed from the panel members. The forum will be informal. To capture the general thoughts, the session will be recorded for the sole purpose of preparing a summary report. This report will list the participants, but will not attribute remarks to any specific person.
Participants should be prepared to address the following four issues.
1. Scope
OSHA could take a broad inclusive approach or could limit the scope in one or more ways. Please refer to the spreadsheet attached when considering the following questions.
Would it be appropriate to exclude certain materials based on their explosibility? Should the exclusion go beyond non-combustible dusts to some minimally combustible dusts as well? If so, what criteria would appropriate? There are dusts in the low Kst range that have produced fatal incidents – including, most strikingly, sugar dust.
Would it be appropriate to exclude industries that have a history of fewer incidents? Fewer incidents with injuries? Fewer incidents with fatalities? Where should the cutoff be?
Would it be appropriate to exclude smaller entities? If so, should this be based on facility size, number of employees, or some other threshold? If not, would a different level of controls be appropriate?
Are there any other scope-limiting approaches that would be appropriate?
If possible, provide verifiable data to support your individual expert opinion, and indicate its source.
2. Focus on Preventing Secondary Explosions
Would focusing on secondary explosions prevent most multi-fatality events? How could OSHA estimate the number of incidents or fatalities prevented by such an approach? Is data available that indicates whether fatalities were due to primary vs. secondary events?
What would be the impact of omitting provisions that only address primary explosions? An example would be ignition-source controls within processing or dust-collection equipment.
What would be the impact of omitting provisions that minimize the effects of an incident, were one to occur? Examples include explosion vents and explosion-suppression systems.
Is there a simple way to define quantities of dust that are necessary to trigger cleaning action to prevent secondary explosions? Specifically, what method could be implemented by small entities without calculations or outside expertise?
How much dust accumulation on horizontal surfaces results from failure to install or maintain dust-collection systems as recommended in the NFPA Standards? For example, if NFPA-recommended dust-collection equipment was to be omitted from a packaging operation, the fugitive dusts emitted, but not captured, would eventually accumulate on surfaces.
3. Existing Facilities
OSHA is concerned about the burden on employers if existing facilities must retroactively comply with the standard, especially the higher-cost engineering controls. Are there situations where engineering controls are not essential for existing facilities and, if so, how could they be defined in a standard?
Data available to OSHA indicates widespread non-compliance with engineering control provisions of NFPA standards. Has compliance improved in the last few years as a result of increased hazard awareness and government enforcement efforts? If engineering controls were not mandated, how likely are they to be installed voluntarily, and in what situations?
4. Multiple Layers of Protection
Many fire- and explosion-control scenarios involve a number of layers of protection. For example, a typical modern office building would have a fire alarm system to alert occupants, a sprinkler system to control a fire, barriers to limit fire spread, and multiple exits to allow occupants to egress.
Would it be appropriate for OSHA to require a single layer of protection against dust explosions – for example, housekeeping without ignition controls or explosion mitigation features?
OSHA's current standards include controls for certain ignition sources, including electrical equipment, powered industrial trucks, and welding. Would it be necessary for employee protection to require controls, in addition to housekeeping, for ignition sources such as static electricity, friction, sparks, hot surfaces, open flames, or smoking?
If engineering controls were not mandated, what layers of protection would be appropriate?
In your expert opinion, what should be the hierarchy for protection for combustible dust hazards (dust control, ignition control, explosion mitigation)?
Dust Incidents Table
Dust Type1 | Kst2,3 | Number of Incidents4 | Number of Injuries | Number of Fatalities | |||||||
---|---|---|---|---|---|---|---|---|---|---|---|
Total | Where Injuries and Fatalities Are Known |
Avg. | Min. | Max. | Total | Avg. | Min. | Max. | Total | ||
Tobacco | 12 | 1 | 1 | 1.0 | 1 | 1 | 1 | 0.0 | 0 | 0 | 0 |
Cotton | 24 | 8 | 7 | 0.1 | 0 | 1 | 1 | 0.1 | 0 | 1 | 1 |
Iron | 50 | 1 | 1 | 0.0 | 0 | 0 | 0 | 1.0 | 1 | 1 | 1 |
Coffee dust | 55 | 1 | 0 | -- | -- | -- | -- | -- | -- | -- | -- |
Sugar, beet | 59 | 2 | 1 | 15.0 | 15 | 15 | 15 | 1.0 | 1 | 1 | 1 |
Steel | 61 | 4 | 4 | 0.8 | 0 | 1 | 3 | 0.0 | 0 | 0 | 0 |
Corn | 75 | 1 | 1 | 0.0 | 0 | 0 | 0 | 0.0 | 0 | 0 | 0 |
Tantalum | 90 | 1 | 1 | 0.0 | 0 | 0 | 0 | 0.0 | 0 | 0 | 0 |
Alfalfa | 94 | 1 | 1 | 2.0 | 2 | 2 | 2 | 0.0 | 0 | 0 | 0 |
Sewage sludge | 96 | 2 | 2 | 0.5 | 0 | 1 | 1 | 0.0 | 0 | 0 | 0 |
Corn (maize) gluten | 110 | 1 | 1 | 3.0 | 3 | 3 | 3 | 1.0 | 1 | 1 | 1 |
Starch, wheat | 115 | 2 | 2 | 0.0 | 0 | 0 | 0 | 0.0 | 0 | 0 | 0 |
Phenolic resin | 129 | 3 | 3 | 16.0 | 1 | 38 | 48 | 3.3 | 0 | 7 | 10 |
Wheat starch | 132 | 1 | 1 | 0.0 | 0 | 0 | 0 | 0.0 | 0 | 0 | 0 |
Polyethylene | 134 | 1 | 1 | 38.0 | 38 | 38 | 38 | 6.0 | 6 | 6 | 6 |
Whey | 140 | 1 | 1 | 8.0 | 8 | 8 | 8 | 1.0 | 1 | 1 | 1 |
Polyurethane foam | 145 | 4 | 3 | 0.0 | 0 | 0 | 0 | 0.0 | 0 | 0 | 0 |
Rubber, synthetic | 145 | 1 | 1 | 0.0 | 0 | 0 | 0 | 0.0 | 0 | 0 | 0 |
Sulfur | 151 | 3 | 2 | 0.5 | 0 | 1 | 1 | 0.0 | 0 | 0 | 0 |
Cocoa bean dust | 152 | 1 | 1 | 1.0 | 1 | 1 | 1 | 1.0 | 1 | 1 | 1 |
Sugar (10x) | 154 | 1 | 1 | 1.0 | 1 | 1 | 1 | 0.0 | 0 | 0 | 0 |
Polyurethane | 156 | 1 | 1 | 16.0 | 16 | 16 | 16 | 0.0 | 0 | 0 | 0 |
Bone meal | (0-200) | 2 | 1 | 0.0 | 0 | 0 | 0 | 0.0 | 0 | 0 | 0 |
Nylon fiber | (0-200) | 2 | 2 | 20.0 | 3 | 37 | 40 | 0.0 | 0 | 0 | 0 |
Sewage sludge, dehumidified, from paper-manufacturing-plant | (0-200) | 1 | 1 | 2.0 | 2 | 2 | 2 | 0.0 | 0 | 0 | 0 |
Titanium | (0-200) | 1 | 0 | -- | -- | -- | -- | -- | -- | -- | -- |
Walnut shells | (0-200) | 1 | 1 | 6.0 | 6 | 6 | 6 | 0.0 | 0 | 0 | 0 |
Cork | 202 | 1 | 1 | 1.0 | 1 | 1 | 1 | 0.0 | 0 | 0 | 0 |
Starch, corn | 202 | 2 | 2 | 0.0 | 0 | 0 | 0 | 1.0 | 1 | 1 | 2 |
Cellulose | 229 | 2 | 2 | 1.0 | 1 | 1 | 2 | 0.0 | 0 | 0 | 0 |
Barley | 240 | 1 | 1 | 4.0 | 4 | 4 | 4 | 0.0 | 0 | 0 | 0 |
Fumaric acid | (201-300) | 1 | 1 | 9.0 | 9 | 9 | 9 | 0.0 | 0 | 0 | 0 |
Ibuprofen | (201-300) | 1 | 1 | 2.0 | 2 | 2 | 2 | 0.0 | 0 | 0 | 0 |
Vitamin granulate | (201-300) | 3 | 3 | 1.3 | 0 | 2 | 4 | 0.0 | 0 | 0 | 0 |
Magnesium | 508 | 10 | 9 | 0.8 | 0 | 2 | 7 | 0.7 | 0 | 2 | 6 |
Charcoal (general) | 10-117 | 3 | 3 | 2.7 | 1 | 4 | 8 | 0.7 | 0 | 1 | 2 |
Oat (general) | 14-81 | 2 | 2 | 0.0 | 0 | 0 | 0 | 0.0 | 0 | 0 | 0 |
Potato (general) | 20-89 | 1 | 1 | 0.0 | 0 | 0 | 0 | 0.0 | 0 | 0 | 0 |
Paper (general) | 21-138 | 14 | 12 | 1.1 | 0 | 9 | 13 | 0.0 | 0 | 0 | 0 |
Milk (general) | 28-125 | 1 | 1 | 2.0 | 2 | 2 | 2 | 0.0 | 0 | 0 | 0 |
Dog food (general) | 41-55 | 1 | 1 | 3.0 | 3 | 3 | 3 | 0.0 | 0 | 0 | 0 |
Corn (general) | 47-163 | 14 | 14 | 1.4 | 0 | 10 | 20 | 0.0 | 0 | 0 | 0 |
Coke (general) | 47-75 | 3 | 1 | 3.0 | 3 | 3 | 3 | 0.0 | 0 | 0 | 0 |
Flour (general) | 57-112 | 4 | 4 | 1.0 | 0 | 3 | 4 | 0.0 | 0 | 0 | 0 |
Sugar (general) | 59-154 | 7 | 7 | 5.7 | 0 | 33 | 40 | 2.0 | 0 | 14 | 14 |
Starch (general) | 89-202 | 4 | 4 | 0.0 | 0 | 0 | 0 | 0.0 | 0 | 0 | 0 |
Rubber (general) | 90-162 | 10 | 10 | 2.4 | 0 | 13 | 24 | 0.6 | 0 | 5 | 6 |
Toner (general) | 95-196 | 1 | 1 | 0.0 | 0 | 0 | 0 | 1.0 | 1 | 1 | 1 |
Maltodextrin (general) | 96-128 | 1 | 1 | 3.0 | 3 | 3 | 3 | 1.0 | 1 | 1 | 1 |
Aluminum (general) | 100-415 | 29 | 26 | 2.5 | 0 | 25 | 64 | 0.5 | 0 | 2 | 14 |
Wood (general) | 102-205 | 79 | 76 | 1.6 | 0 | 15 | 124 | 0.3 | 0 | 3 | 20 |
Soy (general) | 110-125 | 2 | 2 | 0.5 | 0 | 1 | 1 | 0.0 | 0 | 0 | 0 |
Malt (general) | 122-170 | 1 | 1 | 2.0 | 2 | 2 | 2 | 0.0 | 0 | 0 | 0 |
Coal (general) | 123-129 | 29 | 28 | 3.6 | 0 | 30 | 100 | 0.6 | 0 | 6 | 15 |
ABS (general) | 142-209 | 1 | 1 | 0.0 | 0 | 0 | 0 | 0.0 | 0 | 0 | 0 |
Chemical | G | 4 | 4 | 0.5 | 0 | 1 | 2 | 0.0 | 0 | 0 | 0 |
Feed | G | 6 | 5 | 1.4 | 0 | 3 | 7 | 0.2 | 0 | 1 | 1 |
Grain | G | 25 | 25 | 1.2 | 0 | 9 | 30 | 0.3 | 0 | 3 | 7 |
Metal | G | 9 | 9 | 0.4 | 0 | 2 | 4 | 0.1 | 0 | 1 | 1 |
Plastic | G | 12 | 10 | 1.6 | 0 | 7 | 16 | 0.0 | 0 | 0 | 0 |
Mixture | M | 23 | 22 | 2.4 | 0 | 13 | 52 | 0.7 | 0 | 4 | 15 |
Ammonium perchlorate | U | 1 | 1 | 4.0 | 4 | 4 | 4 | 1.0 | 1 | 1 | 1 |
Benzoyl peroxide | U | 1 | 1 | 1.0 | 1 | 1 | 1 | 0.0 | 0 | 0 | 0 |
Carbon black | U | 2 | 2 | 0.5 | 0 | 1 | 1 | 0.0 | 0 | 0 | 0 |
Coal tar pitch | U | 1 | 1 | 0.0 | 0 | 0 | 0 | 2.0 | 2 | 2 | 2 |
Coatings, powder | U | 5 | 5 | 2.0 | 0 | 5 | 10 | 0.0 | 0 | 0 | 0 |
Coatings, rubber | U | 1 | 1 | 7.0 | 7 | 7 | 7 | 0.0 | 0 | 0 | 0 |
Fly ash | U | 1 | 1 | 0.0 | 0 | 0 | 0 | 1.0 | 1 | 1 | 1 |
Grapefruit powder | U | 1 | 1 | 1.0 | 1 | 1 | 1 | 0.0 | 0 | 0 | 0 |
Lacquer | U | 1 | 1 | 3.0 | 3 | 3 | 3 | 0.0 | 0 | 0 | 0 |
Phosphorus pentasulfide | U | 1 | 1 | 1.0 | 1 | 1 | 1 | 0.0 | 0 | 0 | 0 |
Polyalphamethyl styrene | U | 1 | 1 | 1.0 | 1 | 1 | 1 | 0.0 | 0 | 0 | 0 |
Poultry litter | U | 1 | 1 | 0.0 | 0 | 0 | 0 | 0.0 | 0 | 0 | 0 |
Sodium azide | U | 1 | 1 | 6.0 | 6 | 6 | 6 | 1.0 | 1 | 1 | 1 |
Terephthalic acid | U | 1 | 1 | 2.0 | 2 | 2 | 2 | 2.0 | 2 | 2 | 2 |
Tofu residue | U | 1 | 1 | 16.0 | 16 | 16 | 16 | 1.0 | 1 | 1 | 1 |
Unknown | U | 89 | 71 | 1.0 | 0 | 11 | 68 | 0.1 | 0 | 2 | 10 |
Vinsol resin | U | 1 | 1 | 2.0 | 2 | 2 | 2 | 1.0 | 1 | 1 | 1 |
Pyrotechnics/explosives | EXCLUDE | 4 | 4 | 0.8 | 0 | 1 | 3 | 0.5 | 0 | 2 | 2 |
Grand Total (Excluding pyrotechnics/ explosives) |
-- | 466 | 424 | 2.0 | 0 | 38 | 861 | 0.3 | 0 | 14 | 146 |
1 Dust type was assigned to each incident based on the best available information, including FATCAT and U.S. Chemical Safety Board (CSB) incident reports, press releases, and general information about the facility. For cases where only limited information was available, dust type is either identified at a generic level or not identified at all.
2 Kst values were identified using three resources: NFPA standards (in particular, NFPA 68, Table F.1(a)-(e); NFPA 61, Table A.6.2.1; and NFPA 484, Table A.1.1.3), the website www.airpurificationinc.com/resources/2010/10/is-my-dust-combustible/, and the GESTIS-DUST-EX database maintained by Institut für Arbeitsschutz der Deutschen Gesetzlichen Unfallversicherung (IFA, Institute for Occupational Safety and Health of the German Social Accident Insurance). Kst values from the GESTIS-DUST-EX database were used only when values were not available from the first two resources.
3 Kst values were identified as precisely as possible; however, not all materials could be assigned a specific value:
- A range indicates that sources yielded multiple Kst values for the same material, or, that the Kst values for multiple related materials were used as a proxy for a general material (e.g., the range for starch [general] is based on the Kst values for corn starch, potato starch, rice starch, and wheat starch).
- A "G"; indicates that the dust type is too generic to be able to assign a meaningful range of Kst values.
- An "M"; indicates that the dust is a mixture and thus could not be assigned a Kst value.
- A "U"; indicates that the Kst is unknown, either because the dust type is unknown or because a Kst could not be located for a known dust type.
- In a few cases, the dust explosion class could be located but not the exact Kst value. In these instances, the Kst range for the dust explosion class is placed in parentheses in the Kst column (e.g., 0-200 for a class 1 dust).
- Even where a precise value is given, users should recognize that Kst values still vary by particle size distribution. Therefore, the Kst data in this chart should be viewed only as a generic indicator of the dust's explosibility.
4 Explosible dust incidents span from January 24, 1980 to December 31, 2010 and were compiled from: a CSB database, a blog website (dustexplosions.blogspot.com), press releases, and the OSHA FATCAT database.
1 The ratio of injuries to fatalities in the incident data base is less than six to one, while the ratio of injuries to fatalities in fires and explosions in general, as reported by BLS, is over fifteen to one.
Appendix C. Handouts from Dr. Ali Rangwala
Handout 1
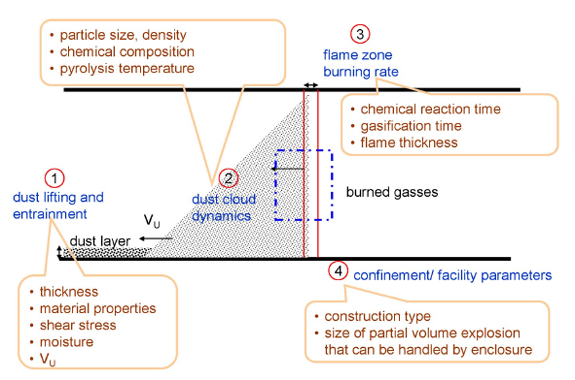
Handout 2
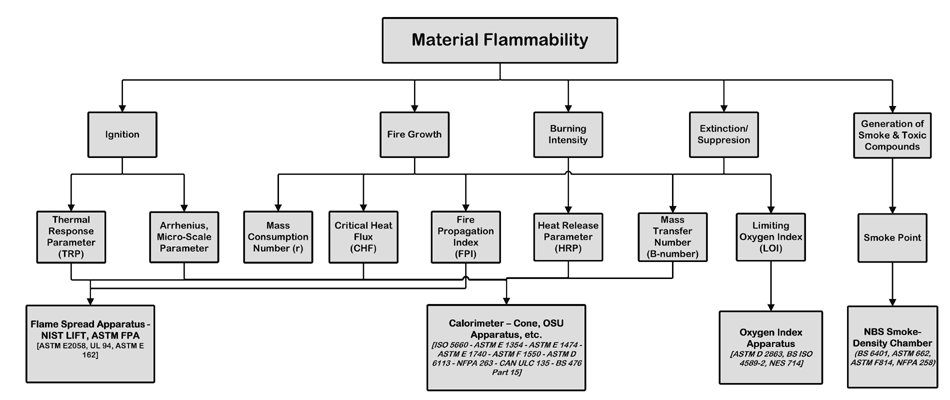
Figure 3: Material flammability flow chart. Tier two from the top describes five different aspects that describes a material's flammability. Tier three shows some of the many parameters that have been used or suggested to describe material flammability. Tier four shows four of the most common small-scale flammability test apparatus.
Supplement to Handout 1 (provided after the meeting)
Handout 1: Exploring Test Methodologies used to Assess Dust Deflagrations
Problem Description
Dust deflagrations are complex phenomena that include several physical processes such as:
- Gasification characteristics of the dust particles
- Ignition
- Burning/propagation rates (i.e. combustion thermo-chemistry)
- Fluid mechanics, heat transfer and interaction between particles and the flow
- Dust lifting and entrainment
- Dust cloud dispersion
Figure 1a shows a sketch of a dust deflagration with the fundamental phenomena controlling the movement of the flame through an unburned mixture of dust and oxidizer. The reaction zone produces high temperature and rapid expansion of gasses that can cause development of high pressure. Figure 1b shows two mechanisms that control the propagation of the reaction zone, where the flame can propagate as a sequential ignition of diffusion flames or as a premixed flame purely in the gas phase. Both the mathematical theory and the parameters controlling these two modes of propagation are completely different! This adds a further level of complexity to the study of dust deflagrations. Due to these complications, a comprehensive mathematical theory to predict deflagration mechanisms of dust clouds is at present beyond reach. Correspondingly, an engineering solution to the problem is also absent.
With this in mind, the best approach in identifying the hazard associated with a fugitive dust is to have a better understanding of the parameters involved in the problem. More specifically the parameters need to be a simple rule of thumb so that plant operators and inspectors can easily implement them. Parameters such as heat of combustion, minimum ignition energy, minimum explosible concentration etc: have been used repeatedly in various literature sources to classify various kinds of dust. However, a comprehensive list of all the parameters involved and their inter-relationship with respect to each other is lacking.
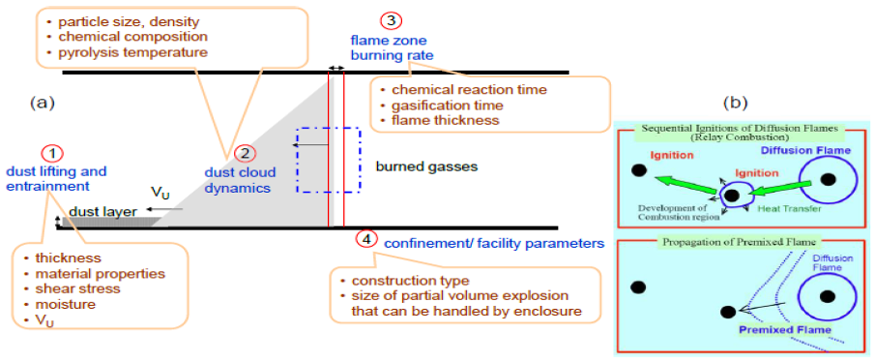
Figure 1: (a) A schematic of a dust flame showing areas that need to be identified and studied. Figure 1b shows two extreme cases of flame propagation mechanisms possible (zone 3). The dust-oxidizer flame can move via sequential ignitions or as a premixed flame. (Figure 1b adapted from Lin et al.)
Currently NFPA 654 (Standard for Prevention of Fire and Dust Explosion from the Manufacturing, Processing and handling of Combustible Solid Particles) and 664 (Standard for the Prevention of Fires and Explosions in Wood Processing and Woodworking Facilities) list the following parameters that are used to identify a dust explosion hazard (a description of each parameter is further elaborated in Appendix A):
- Minimum explosion concentration, MEC (3.3.16, NFPA 654 and A.3.3.9.2, NFPA 664)
- Minimum ignition energy (MIE) (A.3.3.9.2, NFPA 664)
- Particle size distribution (A.3.3.9.2, NFPA 664)
- Moisture content (A.3.3.9.2, NFPA 664)
- Maximum explosion pressure at optimum concentration (A.3.3.9.2, NFPA 664)
- Maximum rate of pressure rise at optimum concentration (A.3.3.9.2, NFPA 664)
- Deflagration index or Kst (A.3.3.9.2, NFPA 664)
- Depth of dust accumulation (Table A.6.6.2, NFPA 654)
- Layer ignition temperature (A.3.3.9.2, NFPA 664)
- Dust cloud ignition temperature (A.3.3.9.2, NFPA 654)
- Limiting oxidant concentration to prevent ignition (A.3.3.9.2, NFPA 654)
- Electrical resistivity (A.3.3.9.2, NFPA 654)
- Charge relaxation time (A.3.3.9.2, NFPA 654)
- Chargeability (A.3.3.9.2, NFPA 654)
- Minimum dust accumulation area (A.6.4.2.2 (2), NFPA 654)
- Lowest temperature at which pyrolysis has been reported (5.2.4.1, NFPA 654)
- Minimum dust accumulation thickness(0.8 mm -6.2.3.1, NFPA 654 and 3.2 mm - 6.4.2.2, NFPA 664)
As a first step, it is important to identify parameters out of this list of 17 that are most important and relevant to the problem at hand. It should be noted that the minimum dust layer thickness which is the main basis for identifying a dust hazard in NFPA 654, characterizes the quantity of fugitive dust that can reasonably be suspended by a single credible upset1 vs. the room volume it can be suspended in. This quantity however does not characterize the properties of dust and also suffers from identifying a minimum threshold. The threshold in this approach would be the quantity where the over-pressure resulting from the explosion does not result in damage beyond the initiating area. Thus additional parameters such as size of a partial volume explosion that can be handled by the construction need to be included. Such additional parameters are included in Appendix A where a first attempt at documenting all the parameters involved in the problem (48 parameters total) are listed. Overall, the parameters in Appendix A are grouped into thermodynamic, thermokinetic, physical, chemical, and electrical properties of the dust. In addition, facility related parameters such as type of construction, confinement level, operating temperature, humidity in air etc: are also accounted. Thermodynamic properties are heat of combustion, adiabatic flame temperature, specific heat, thermal conductivity, and latent heat of vaporization. Thermokinetic properties are based on both the thermodynamic and chemical kinetic effects. For example, the laminar burning velocity2 depends on both thermodynamic (heat of combustion) as well as chemical kinetic (rate of gas phase reaction) processes. Physical properties include mass of particles, particle size, ease of suspension etc. Chemical properties include parameters used to quantify chemical composition of the dust. Dust deflagrations are also sensitive to electrical properties of the dust which determine the ease of charge dissipation and charge storage to analyze static electric ignition. Facility related parameters include construction type, confinement levels etc.
It could be argued that all 48 parameters listed in Appendix A are important and need to be known to quantify a hazard associated with a dust. However, a more rational engineering approach would be to make an optimal choice of these parameters based on:
- How important is the effect of these parameters on the explosion outcome
- How variable are these parameters among most common materials susceptible to dust explosions
- How much resolution is really needed for adequate design in practice
Some of the parameters listed in Appendix A can thus drop out and a list of main controlling factors of a dust hazard can be obtained. A series of methodologies to assess the resulting parameters can be then analyzed proposing an optimal set of tests that will lead to the quantification of these parameters. The parameters could then be incorporated into a dust hazard analysis guideline to establish impact, but impact assessment needs to be related to existing impact assessment methodologies. So this approach has to follow with:
- How adequate are the testing methodologies in isolating and quantifying these parameters, propose viable improvements
- How good are the impact testing methodologies currently used when assessing the outcome
- Can the testing methodologies be improved based on the recent advances in measurement techniques and diagnostic tools
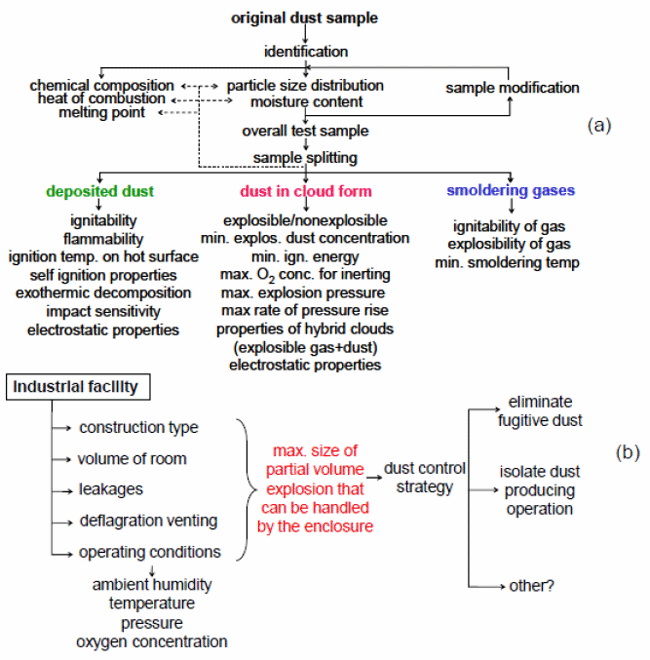
Figure 2: (a) Flowchart of possible tests for assessing the ignitability and explosibility of dusts and (b) parameters associated with the facility
NFPA 664 (A.6.4.2.2) provides a section on guidelines for amount of dust that is "tolerable" in an industrial facility. This has to be developed as part of a more formal analysis and tested using an experimental program. For example, the experimental phase could involve a series of partial volume explosions - to find out if there is a safe quantity of dust for partial volume explosions in ordinary industrial construction.
1 Upsets are, for example, a compressed air line lets loose and the turbulence forms a cloud of fugitive dust that had accumulated on equipment tops and bar joists.
2 Laminar burning velocity also called flame velocity, normal combustion velocity, or laminar flame speed is defined as the velocity of at which the unburned gases move through the combustion wave in the direction normal to the wave surface
References
- Park, H., A.S. Rangwala, and N.A. Dembsey, J. Hazardous Materials, 2008. (accepted for pub).
- Balasuria, S. and A.S. Rangwala, "Analysis of Flame Propagation in a Premixed Flammable Dust-Oxidizer Mixture. Comb. Theory and Modeling,"; 2009. (under review).
- Rangwala, A.S. Park, H., N.A, Dembsey, E. J. Granite, "Using Thermal and Kinetic Parameters to Model Coal Dust Ignition,"; in Mary K O' Connor Process Safety Conference. 2008. Texas A&M. (also accepted for a special edition of Journal of Loss Prevention.)
- Rangwala, A.S., T.J. Myers, and A.F. Ibarreta, "Measurement of the Non-Dimensional Frank-Kamenetskii Number Using a Standard Dust Layer Ignition Testing Apparatus,"; in Fire and Explosion Hazards. 2007. Edinburgh, UK.
- Joshi, K.A., V. Raghavan, and A.S. Rangwala, "Spontaneous Ignition of Moist Coal,"; in 6th Joint Meeting of Combustion Institute. 2009. Ann Arbor, Michigan.
- Joshi, K.A., A.S. Rangwala, and V. Raghavan, "Spontaneous Ignition of Coal Dust Layers";, in Proc. Asia Pacific Combustion Conference. 2009. Taipei, Taiwan, May 24-27.
- Park, H., Joshi K. A., Rangwal A. S., E.J. Granite, "Estimation of Thermal and Kinetic Parameters to Model Coal Dust Ignition"; in Pittsburgh Coal Conference. 2008. Pittsburgh, PA.
- Granite, E.J. and A.S. Rangwala, "Overview of Underground Coal Fires,"; International Pittsburgh Coal Conference, Sep, 2009. 26.
- Black, K. and A. Schwalbenberg, "Analysis of Cornstarch-Air Premixed Flames,"; in Major Qualifying Project, A. Rangwala, (advisor). 2009, Worcester Polytechnic Institute: Worcester.
- Alexander, A. and J. Desrosier, "Ignition of Dust in a Corner,"; in Major Qualifying Project, A. Rangwala, (advisor) 2009, Worcester Polytechnic Institute.
- Eckhoff, R. K., Dust Explosions in the Process Industries. 3 ed. 2003, Boston: Gulf Professional Publishing/ Elsevier.
- Joshi K.A.and Levendis. Y., Co-combustion of coal and bagasse - evolution of emissions, evidence of synergism and speciation of PAH emissions. Fuel , 2009. (under review).
- Bragato M., Joshi K.et al, Emissions generated during the co-combustion of coal and bagasse fuel blends. Thirty Second Internation Symposium on Combustion. 2008. Montreal, Canada.
- Jian-Lin, C., R. Dobashi, and T. Hirano, "Mechanisms of flame propagation through combustible particle clouds,"; Journal of Loss Prevention in the Process Industries, 1996. 9(3): p. 225-229.
Appendix A
Parameters Involved
Name of Parameter (symbol, units) |
Description | Established Test Methods or Apparatus* |
|
---|---|---|---|
Thermodynamic Parameters | |||
1 | Heat of combustion (J/g) | Amount of energy released per unit mass undergoing a combustion reaction | Bomb calorimeter |
2 | Combustion efficiency | Fraction of energy that is utilized in pressure build up | Law of Conservation of Energy |
3 | Radiant heat fraction | Fraction of total heat released that is transferred via radiation mode | Radiant flux measurements |
4 | Latent heat of vaporization (J/g) | Amount of heat required to vaporize a unit mass of fuel | Differential Scanning Calorimeter |
5 | Adiabatic flame temperature (°C) | Maximum possible temperature achieved by the combustion reaction in a constant pressure process | Theoretical Calculations |
6 | Specific heat of dust (J/g- K) | Amount of energy required per unit mass of dust to increase the temperature of the dust by one unit | Differential Scanning Calorimeter |
Thermo-kinetic Parameters | |||
7 | Laminar burning velocity (m/s) | Velocity at which unburned gases move through a combustion front in the direction normal to the front surface | None |
8 | Propagation speed of smoldering reaction front (m/s) | Rate at which a exothermic oxidation reaction front moves in the direction of non-reactive zone of a dust layer | |
9 | Rate of reaction in the gas phase (g/s) | Rate at which the reactant gas concentration depletes | |
10 | Rate of reaction in the solid phase (surface chemical reaction rate) (g/s) | Identifies the smoldering combustion of a dust layer. Smoldering layers can release combustible vapors such as CO, CH4, which can lead to a gas deflagration | |
11 | Maximum closed volume deflagration pressure (bar) | Maximum pressure reached during a dust deflagration for the optimum concentration of the dust cloud | ASTM E1226 |
12 | Maximum closed volume rate of pressure rise (bar/s) | Rate of pressure rise at maximum pressure reached during a dust deflagration for the optimum concentration of the dust cloud | ASTM E1226 |
13 | Deflagration index, (KSt) (bar-m/s) | Rate of pressure rise at maximum pressure during a dust deflagration normalized to unit volume | ASTM E1226 |
14 | Minimum explosion concentration (MEC) (g/m3) | Minimum concentration of a combustible dust cloud sufficient to increase the pressure by 1 atmosphere (14.7 psi or 1 .01bar) due to deflagration. Dust assumed to be well dispersed in air. | ASTM E 1515 |
15 | Minimum ignition energy (MIE) (mJ) | Minimum energy sufficient to ignite most easily ignitable concentration of fuel in air | ASTM E 2019 |
16 | Autoignition temperature of layer (°C) | Lowest set temperature of the surface at which dust layer on it will ignite spontaneously | ASTM E 2021 |
17 | Autoignition temperature of cloud (°C) | Minimum temperature at which a dust cloud will self ignite | ASTM E 1491 06 (Godbert Greenwald Furnace Test) |
18 | Limiting oxygen concentration (LOC) | Minimum oxygen concentration at the limit of flammability for the worst case (most flammable) fuel concentration |
ASTM E 2079 |
Physical Parameters | |||
19 | Thermal conductivity of dust (W/m°C) | Amount of heat transmitted through a unit thickness in a direction normal to a surface of unit area caused due to a unit temperature gradient | |
20 | Mass of combustible particulate solid (g) | Typically a fugitive dust layer can contain inerts which are not combustible. This property accounts for this variable | |
21 | Particle shape | Quantitatively, shape factors and coefficients are used as parameters in equations governed by particle shape | Pattern recognition techniques |
22 | Particle size (m) | Characteristic dimension of irregularly shaped particle representing the diameter of equivalent sphere | Image Analysis with Microscope |
23 | Particle size distribution | Statistical term that quantifies fluctuations in size and shape of particles of given dust sample | ASTM B761 - 06 |
24 | Bulk density (g/cm3) | Weight of dust per unit volume | |
25 | Porosity | Measure of difference in densities of dust bulk and dust particle because of void spaces between particles in the bulk | |
26 | Degree of compaction of powder | Ratio of volume under specified pressure to volume under ambient pressure for a given mass of dust and configuration of dust pile | |
27 | Moisture content in dust | Weight percentage of water content in given dust sample | |
28 | Layer thickness (mm) | Minimum thickness of dust layer of a give particle size needed to cause a deflagration | |
29 | Surface area/volume ratio of dust (1/m) | Ratio of surface area to volume of given dust particles can be used to relate the arbitrary particle shapes to standard shapes like cube, sphere, cylinder etc. | |
30 | Suspension | Ease with which particles can be suspended in air | |
31 | Dispersibility | Degree of dispersion in a dust cloud, depends on cohesiveness of particles, settling velocity, moisture content | ASTM E 1945 |
32 | Agglomeration | A mass conserving, number-reducing process that shifts the particle size distribution towards larger sizes | |
33 | Terminal settling velocity of dust particle (m/s) | Velocity of a particle when the drag force and buoyancy force balance equal the gravitational pull | |
34 | Speed of sound in dust cloud (m/s) | Plays an important role in all compressible flow phenomena | |
Chemical Parameters | |||
35 | Chemical composition | Molecular formula of the sample gives important information like Molecular Weight, acidic or basic nature, special affinity for other chemicals | |
36 | Reactivity with water |
||
Electrical Parameters | |||
37 | Volume resistivity | Measure of electrostatic ignition hazard of the dust | IEC 60093 |
38 | Charge relaxation time | Time duration of charge retention in a dust | IEC 61340-2- 1:2000 |
39 | Chargeability |
Propensity of dust particles to become charged when flowing or air-bourn | IEC 61340-2- 1:2000 |
External Parameters (facility related) | |||
40 | Size of partial volume explosion that can be handled by the construction | This factor will depend on construction type, volume of initial cloud that can be formed, number of vents installed, and nature of dust | |
41 | Type of construction | Based on NFPA 220 standard on types of building construction | |
42 | Room volume (m3) | Total volume of room/enclosure where fugitive dust accumulation is possible | |
43 | Operating temperature (°C) | Certain facilities could operate at a temperature higher than ambient. Thus possibility of autoignition is higher. | |
44 | Operating pressure (bar) | Certain facilities can operate at pressures other than atmospheric. Studies have shown that thermodynamic and thermo-kinetic properties vary with pressure. | |
45 | Relative humidity | Major of quantity of water vapor in ambient air | |
46 | Confinement | Dimensions of the enclosure which is considered to be at constant temperature and pressure and surrounds given test apparatus or control volume under consideration | |
47 | Turbulence | Flow-instability represented by chaotic state of fluid motion with dissipative structure | Reynolds number |
48 | Detonability limit | Condition outside which self-sustained propagation of detonation wave cannot be realized |
* Test methods starting with ASTM and I EC are standard test methods (Some standard test methods are not designed for dust per se but can be easily modified to include dust samples)
- ASTM B761 – 06: Standard Test Method for Particle Size Distribution of Metal Powders and Related Compounds by X-ray Monitoring of Gravity Sedimentation
- ASTM E 1226 - 05: Standard Test Method for Pressure and Rate of Pressure Rise for Combustible Dust
- ASTM E 1491 – 06: Standard Test Method for Minimum Autoignition Temperature of Dust Clouds
- ASTM 1515 – 07: Standard Test Method for Minimum Explosible Concentration of Combustible Dusts
- ASTM E 1945 – 02(2008): Standard test Method for Percent Dispersibility
- ASTM E 2019 – 03(2007): Standard Test Method for Minimum Ignition Energy of a Dust Cloud in Air
- ASTM E 2021 – 06: Standard Test Method for Hot-Surface Ignition Temperature of Dust Layers
- ASTM E 2079 – 07: Standard Test Methods for Limiting Oxygen (oxidant) Concentration in Gases and Vapors
- IEC 60093: Methods of test for volume resistivity and surface resistivity of solid electrical insulating materials
- IEC 61340-2-1 (2002-06): Measurement methods – Ability of materials and products to dissipate static electric charge
- IEC 61340-2-2 (2000-067: Measurements methods – Measurement of chargeability